- Case Studies
- Isostick Case Study: Prototyping Housing for Optical Drive
Isostick Case Study: Prototyping Housing for Optical Drive
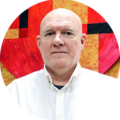
- Star Rapid
- 4 min
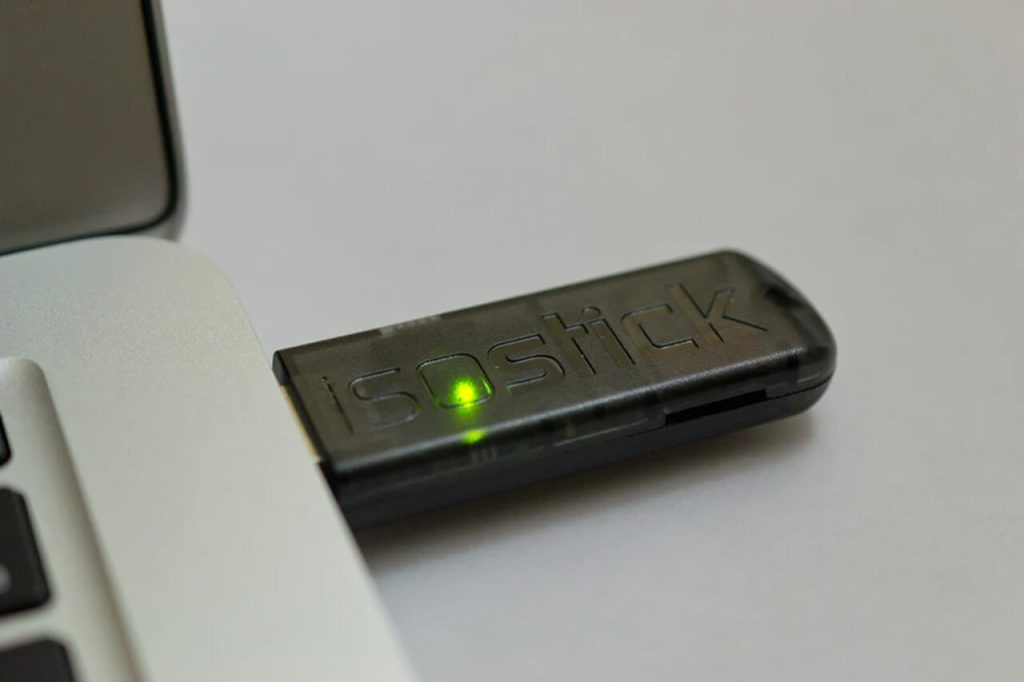
- Case Studies
- Isostick Case Study
Isostick Case Study: Prototyping Housing for Optical Drive
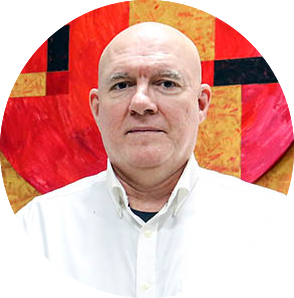
- Star Rapid
- 4 min
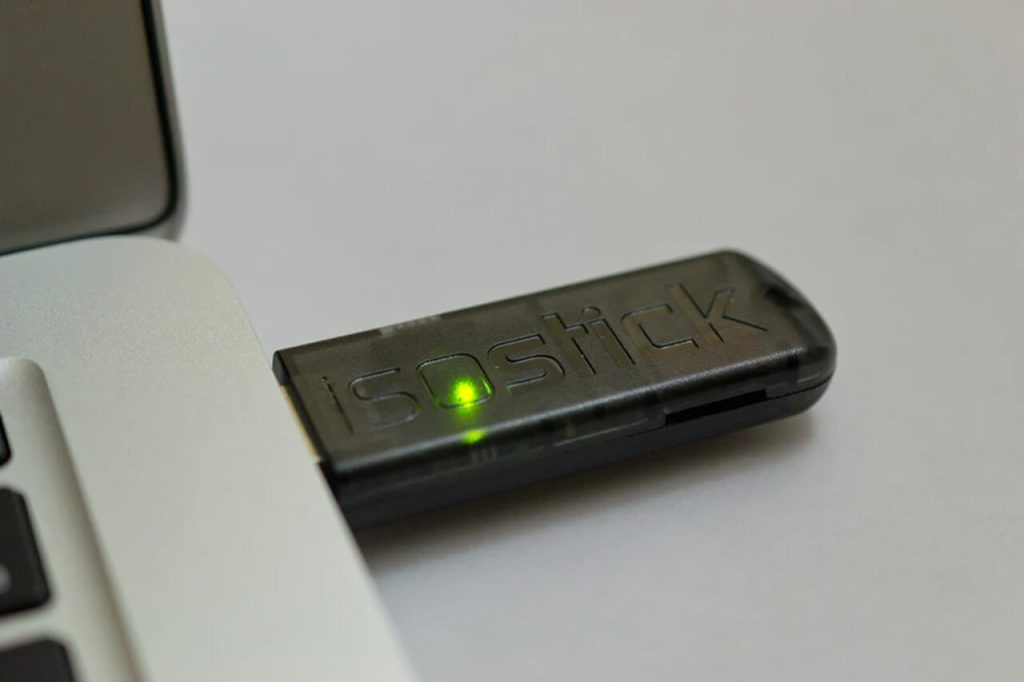
Company
Elegant Invention, LLC
ABOUT
A Technology Company Based in Indiana, USA
Industry
Hardware/Electronics
Components
Flash Drive Plastic Housing
Quantity
3
Lead time
10 Days
Services
Table of Contents
Table of Contents
“I have been impressed by the team at Star Rapid every step of the way. The workmanship and product quality have been consistently excellent, while their initial thinking in terms of translucency helped enhance the visual appeal of the isostick.”
Entrepreneur, Elegant Invention
Prototyping a Drive to Save Your Files in a Flash
Using physical media for booting and installing software can be cumbersome. CDs and DVDs are harder to store and organize, they generate waste, and they’re not the fastest option to work with. The innovative isostick by Elegant Invention solves this problem by combining an optical drive and a flash drive together in one device. See how Star Rapid’s advanced rapid prototyping and tooling services brought this design to life for a crowdfunding campaign.
The Challenge: Overcoming Low-Volume Manufacturing Hurdles
The isostick was launched through a crowdfunding campaign, which typically requires the first samples to be made in low volumes with high enough production quality to impress the early backers.
This approach isn’t without its manufacturing challenges, and the isostick was no exception. We needed to:
- Ensure consistency and quality even at a smaller scale
- Handle design complexities without increasing costs
- Optimize production for quick delivery
- Effectively managing the supply chain and lead times
This required the expertise in rapid prototyping that Star Rapid is known for. We know efficient project management, and we have the engineering teams capable of understanding the uniqueness of the isostick design.
But beyond tackling the typical production challenges, the Star Rapid team also identified opportunities to improve the visual appeal of the samples. In addition to the black version, we suggested working with translucent materials and UV-reactive plastics to achieve a modern and attractive look.
The samples were made using plastic injection molding—the ideal method to make high-quality plastic components because while it has upfront tooling costs, it can allow scalable production in the future.
Our Approach: Making Plastic Cases for the isostick
The isostick plastic cases consisted of three parts: top and bottom shells, as well as an end cap. So, Star Rapid combined our standard procedures with tailored approaches that would best fit the isostick.
As a standard, we provide:
- A Design for Manufacturing (DFM) review, where we analyze the product’s CAD files to find the best manufacturing method, optimize the design for this method, and identify improvements.
- Positive Material Identification (PMI) is used to verify the composition of materials used for tooling and parts fabrication.
- A final inspection is performed in-house in our advanced quality control department. Our specialists analyzed the profile, size, texture, and other specifications of the finished parts before shipment.
We first designed custom-made molds for the parts, and after they were trialed, we started the injection molding by cycling through the following seven steps:
- Raw pellets of plastic resin were dried to the right moisture content.
- Pellets were poured into the hopper of the holding machine.
- Within the barrel, the pellets were mixed and heated until they formed a liquid resin.
- Resin was injected under high pressure through a gate into the mold tool cavity.
- The mold was cooled to solidify the part inside.
- The mold opened, and the part was ejected.
- The tool was prepared for a new cycle.
Molded parts tend to have some excess material that solidifies in the shape of the gate, but they were easily removed by our operators. After that, we sent the samples to our model shop to be painted black. The original plan was to paint them all black, but we suggested fabricating them with a translucent resin.
The result was visible hardware that gave the isostick a high-tech look that resonated very well with its target audience.
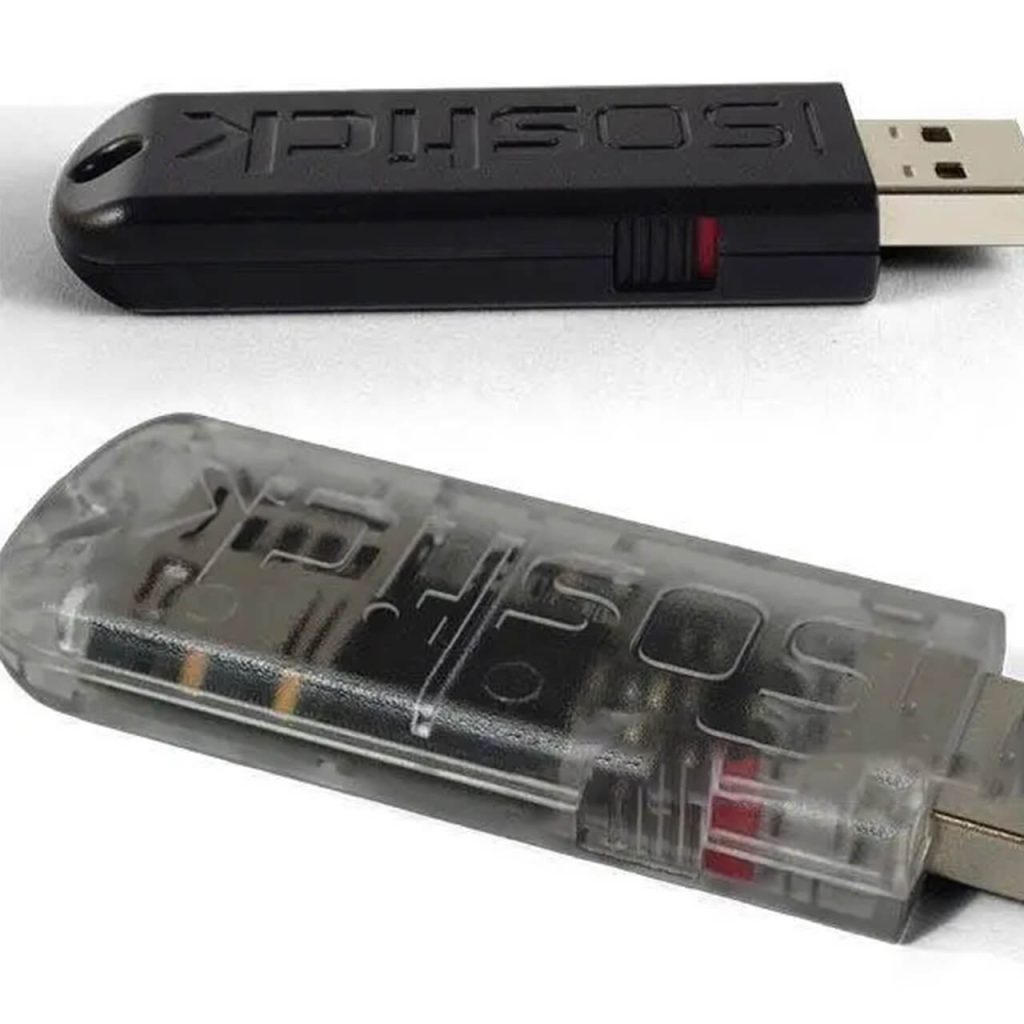
Future versions may also use UV-reactive plastic that glows when in use. And after painting and the final inspection, all samples were ready for shipment.
The Result: High-Quality Parts For a Successful Product Launch
The result of this partnership with Elegant Invention was high-quality parts, produced swiftly and with excellent visual appeal for the promotion of the isostick crowdfunding campaign.
We were pleased to be part of a highly successful launch, with more than 400 people contributing over $66,000 to get the product onto the market. With high-quality tools ready to produce thousands of units, Elegant Invention was well on its way to meeting this demand.
The success of this project highlights the importance of partnering with companies that go beyond production. More than just meeting demand, the ideal manufacturer can enhance your product’s quality through thoughtful decisions on approaches, methods, and materials.
“We always look to provide added value in everything we do. This also includes suggesting novel solutions to a challenge like the material transparency for Elegant Invention—the use of new technology enables us to deliver an order more quickly and competitively. By doing this we feel we can stand out from the crowd and make our mark with each and every client.”
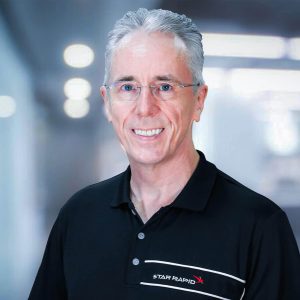
CTO and Founder, Star Rapid
Turn Your Ideas into Market-Ready Products
Star Rapid is the chosen partner for thousands of companies worldwide because of our reputation for creating parts quickly, affordably, and with high quality.
With over 20 years of experience, we offer a wide range of manufacturing solutions to create full-production quality parts, whether you need just one or hundreds of thousands.
Submit your parts today to receive a free quote, and start working with our international team.