- Case Studies
- OTTO Case Study: Manufacturing Front & Back Camera Covers
OTTO Case Study: Manufacturing Front & Back Camera Covers
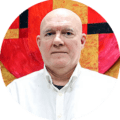
- Star Rapid
- 5 min
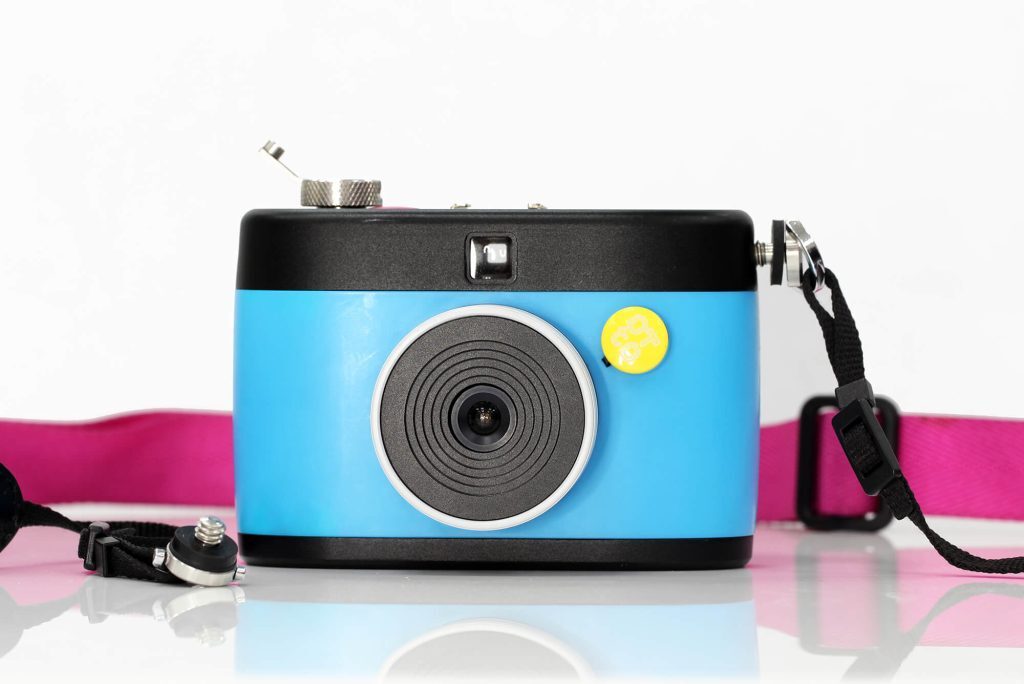
- Case Studies
- OTTO Case Study
OTTO Case Study: Manufacturing Front & Back Camera Covers
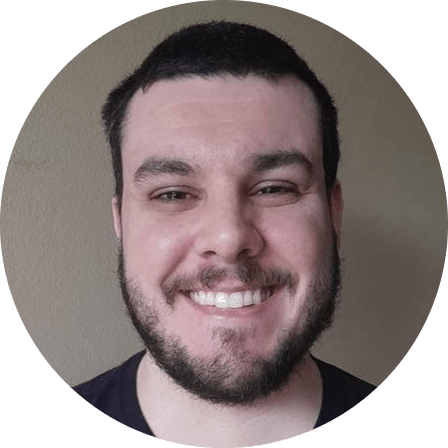
- Star Rapid
- 5 min
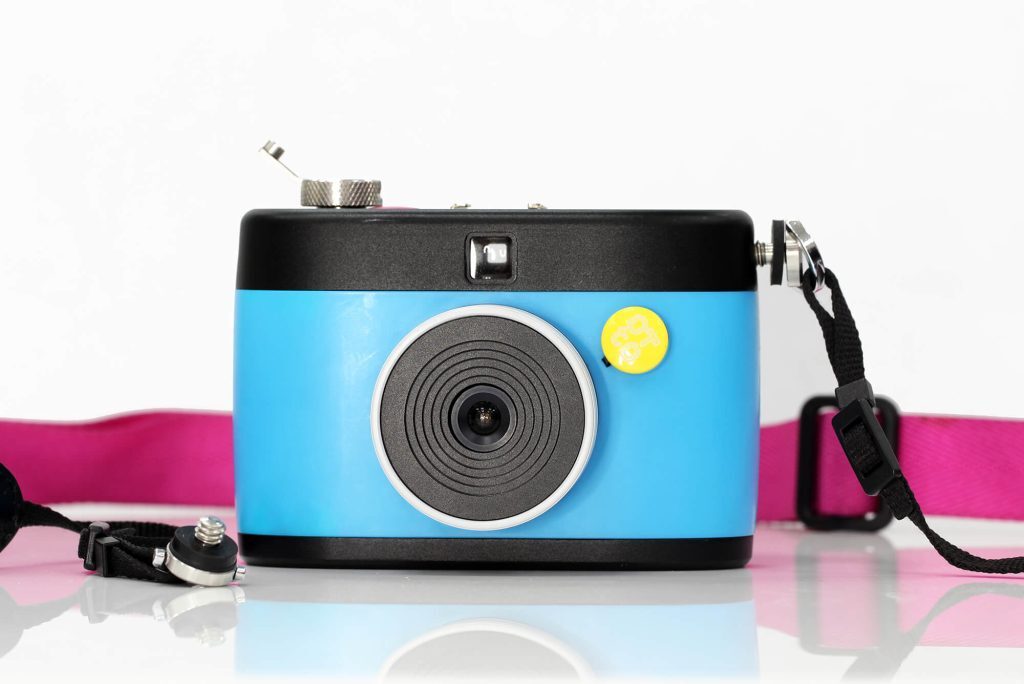
Company
Next Thing Co.
ABOUT
A Startup from Oakland, California
Industry
Consumer Products
Components
Front and Back Camera Covers
Mold Material
P20 Tool Steel
Parts Material
ABS/PC
Quantity
530 units
Lead time
19 days
Services
- CNC Machining
- EDM
- Plastic Injection Molding
- Assembly
Table of Contents
“We worked with Star to produce some of the components for our OTTO prototypes. We were so impressed with these pieces that when it came time to order injection mold tooling for our production run, we knew we could count on Star to deliver. It was my first time designing and producing injection-molded parts (OTTO’s blue, front, and rear housing), and I wasn’t sure how it would turn out. But Star’s team made a fantastic mold, and, aside from some texture and polish, the parts came out perfectly the first time!”
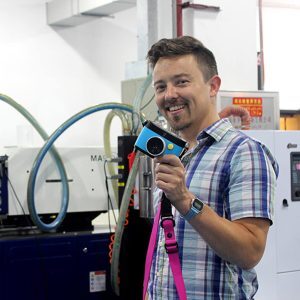
Next Thing Co., CEO
From Click to Code with OTTO: Manufacturing Plastic Housing for the GIF Camera
Few digital cameras create GIFs, the intermediate format between photos and videos. Even fewer allow users to customize every configuration to their own taste. The OTTO camera by Next Thing Co. fills these gaps, being a fully customizable camera that easily creates and shares short videos. Discover why Star Rapid was the ideal manufacturing partner to create the plastic housing for this innovative camera.
The Challenge: Optimizing the OTTO Camera for Production
Since this project was the company’s first product created using plastic injection molding, our partnership started by helping Next Thing Co. optimize their design files for manufacturing.
When making new products, not all design ideas transfer seamlessly to tool drawings and molded parts. So, the support of experienced manufacturing partners can make all the difference.
Four challenges we see when optimizing designs:
- There are many different types of resins, each with specific properties.
- It’s necessary to understand and optimize the effects of heat in the molding process.
- Tooling requires the consideration of many variables, such as draft angles, ejector pins, parting lines, gate locations, corners, etc.
- Each project has its own particularities, so there is no one-size-fits-all solution.
Star Rapid’s engineers carefully analyzed the OTTO files and discussed the best approach with creator Thomas Deckert and his team. For this project, our engineering team built a two-cavity mold to inject both the front and rear parts of the housing simultaneously in order to produce more parts in less time and reduce the cost per part.
Our Approach: Making Plastic Parts for the Camera
The manufacturing of the OTTO was divided into:
- Mold making using EDM and CNC machining to cut and apply texture to steel.
- Plastic injection molding to make the parts from ABS/PC.
After this, the parts underwent final inspection and were delivered to the Next Thing Co. office in California.
Mold Making
We made the molds from P20 tool steel, a semi-hardened steel frequently used in tooling because it is durable and easily machinable. Production started by eroding the material using EDM machining, a technique that employs custom-made electrodes to make cuts or apply textures to the molds. We finished the molds with CNC machining.
We also made custom electrodes to create textured patterns on the cavity of the molds, which are responsible for the distinctive grain on the camera’s body. Below is a drawing of the molds, highlighting the runner—the channel through which the plastic is distributed evenly to each cavity for consistent molding.
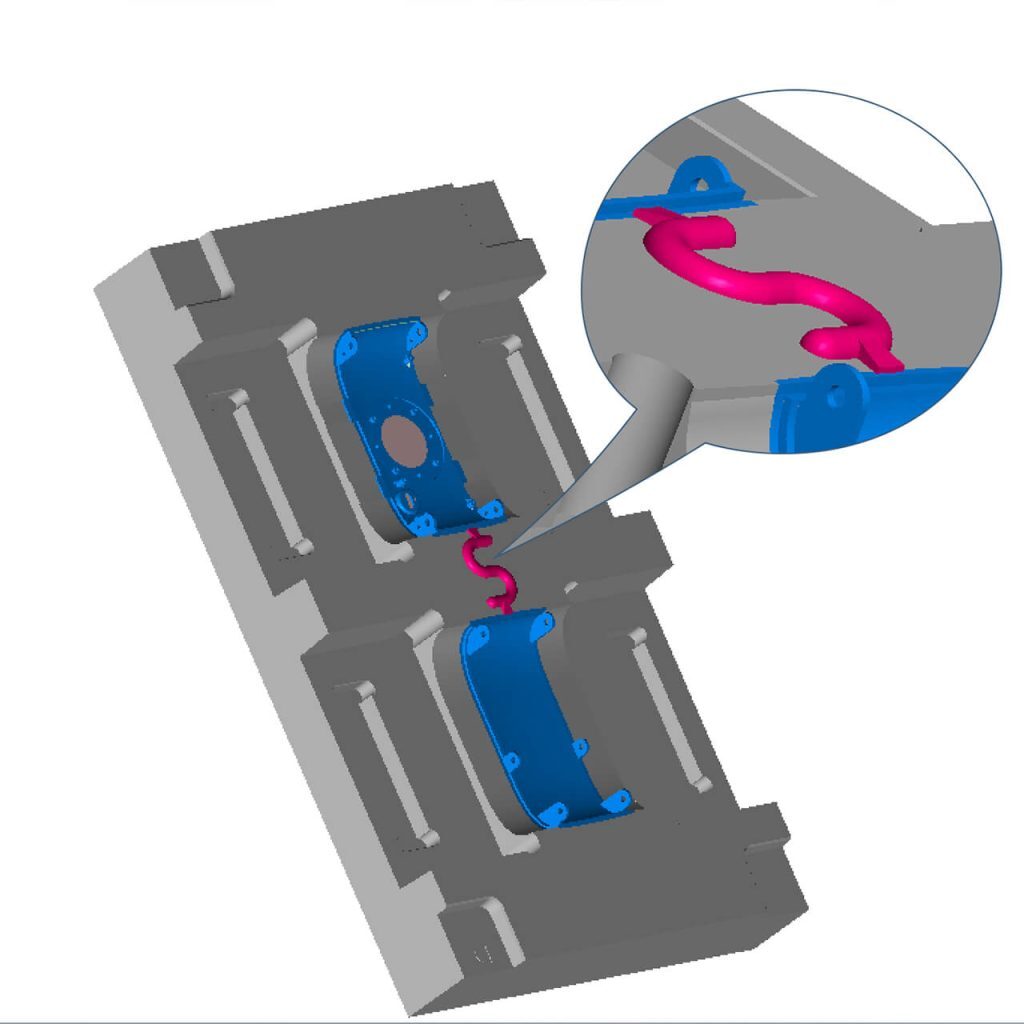
Finally, we tested the molds to identify potential issues and assess performance.
Plastic Injection Molding
It took only a few days to plastic injection mold the entire order since it was relatively small, and we used two-cavity tools. The parts were made from ABS/PC, which combines the high processability of ABS with the excellent mechanical properties, impact resistance, and heat resistance of PC.
After injection, a simple finishing process removed the excess plastic material from the parts and trimmed them flush.
The Results: A Few Weeks Later, OTTO is Ready to Shoot
Next Thing Co. received 530 units of the charming OTTO housing in less than 20 days—all ready to support its crowdfunding campaign.
As usual, for multi-cavity tools, the most time-consuming part was the tooling. But it took Star Rapid just 14 days for toolmaking and only 5 days to make the molded parts.
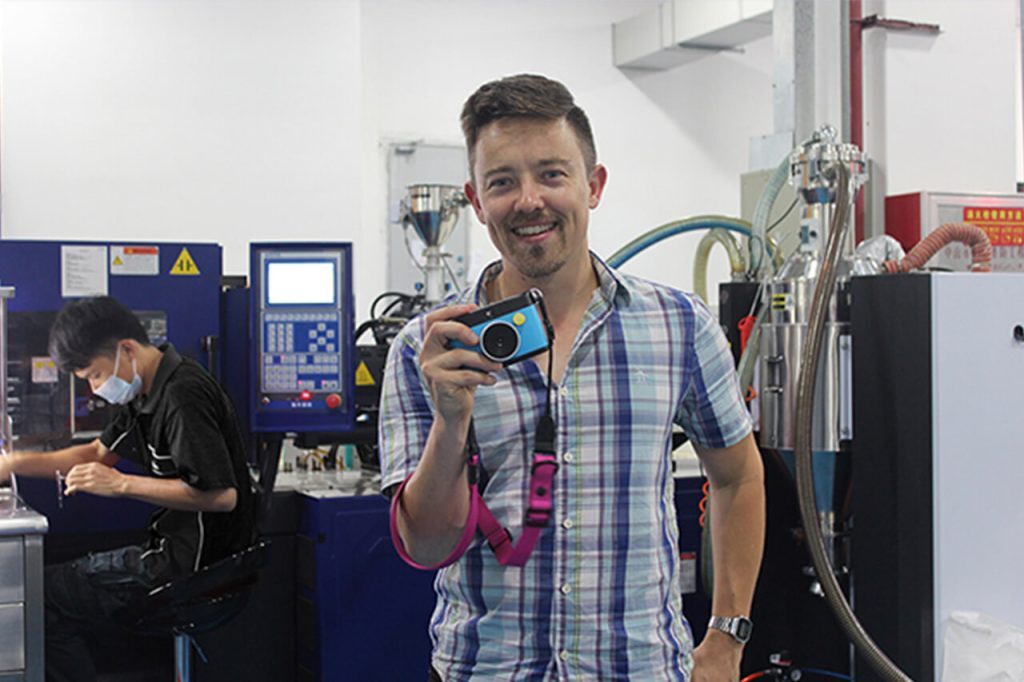
Notably, production is ready to scale up for potentially larger volumes if needed. The quality of the tool steel used is sufficient to reliably produce many thousand more pieces, and the benefits of multi-cavity tools become even more notable for larger volume productions.
Depending on the success of the initial units, Next Thing Co. is already set up for production.
Our years of experience manufacturing orders of all volumes made this all possible. Whether you’re looking for proof of concepts, a few prototypes, or a small volume run, we can understand the specificities of each project and recommend the best path.
We are proud to have been part of OTTO’s successful journey. The camera’s launch received media attention in various countries and raised $71,559 for production from 414 backers.
Make Your Parts Today
Submit your parts today and learn why we are the best partners to turn your product ideas into high-quality parts.
See for yourself why Next Thing Co. and more than 1,000 companies worldwide, including Fortune 500 businesses, trust us when it comes to manufacturing.