- Case Studies
- Biometric Vein Reader Case Study: Plastic Housing Fabrication
Biometric Vein Reader Case Study: Plastic Housing Fabrication
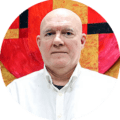
- Star Rapid
- 5 min
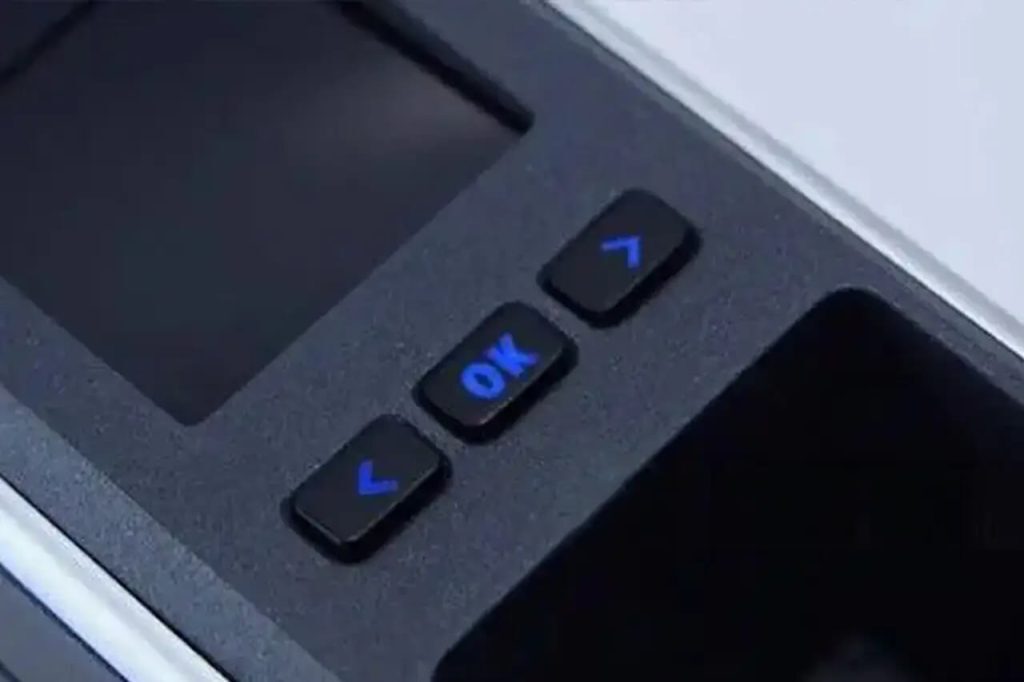
- Case Studies
- Biometric Vein Reader
Biometric Vein Reader Case Study: Plastic Housing Fabrication
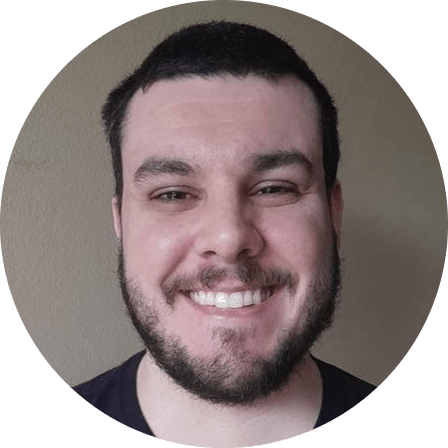
- Star Rapid
- 5 min
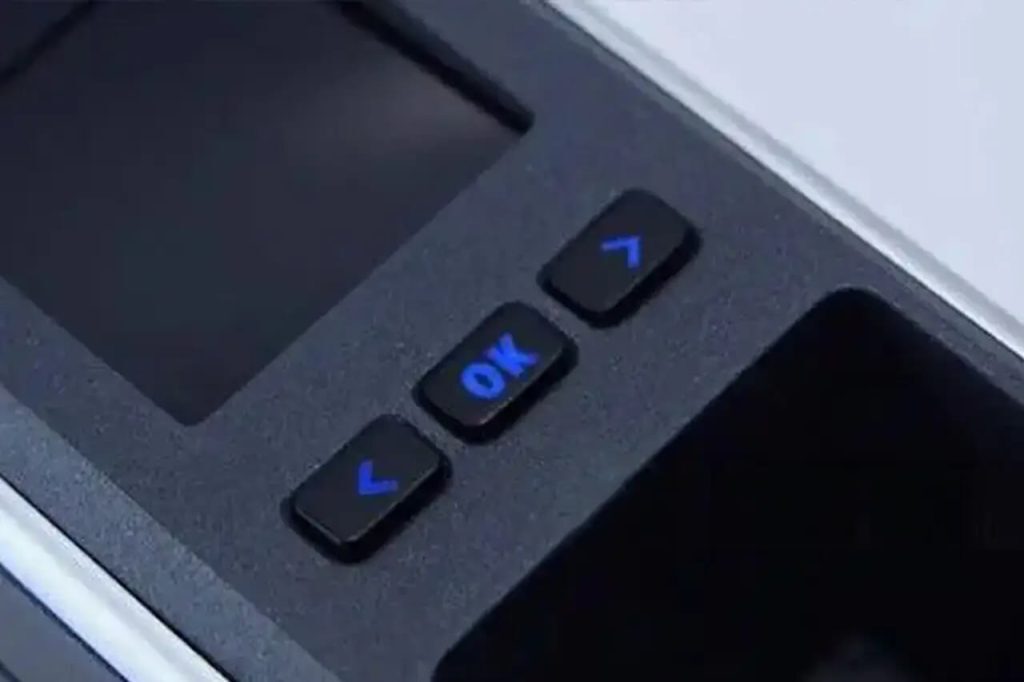
ABOUT
Biometric Vein Readers Enhance Security by Analyzing Unique Finger Vein Patterns
Industry
Security Devices / Electronics
Components
Plastic Housings, Pads, and Key Locks
Materials
UP4280
UPX8400
PX522HT
Polycarbonate
Quantity
15 Units
Services
Table of Contents
Next-Level Security: Fabricating a Biometric Scanning Prototype
Imagine a security system accessed not with a key or password, but with the intricate network of veins beneath your fingerprint. Cutting-edge biometric readers can now map these patterns to create virtually impenetrable security. While the technology itself is revolutionary, its success hinges on a crucial challenge—transforming complex security hardware into sleek, user-friendly devices. That’s where Star Rapid’s expertise came in.
Here’s how our rapid prototyping services helped bring this James Bond-worthy security system from science fiction to reality.
The Challenge: Overcoming Manufacturing Obstacles for Biometric Finger Vein Readers
Manufacturing the finger vein reading device was challenging due to the very nature of the product, the biometric method itself, the manufacturability of the parts, and some specific order requirements.
To fabricate the parts, both the manufacturing and design teams had to consider that:
- Door opening mechanisms, even digital ones, require many discrete parts working seamlessly together.
- The parts must not only be durable but also aesthetically pleasing and match different types of environments. This is even more important when adopting new identification methods, such as vein reading.
- Creating high-quality prototypes in small quantities is naturally challenging due to the cost per piece.
- Some materials can lead to an even more complex project—like resins that are more difficult to process or require more intensive post-treatment.
Our Approach: Creating High-Quality and Functional Device Housing
When the client provided us with the design specifications, our engineering team carefully analyzed the CAD files to address each of these challenges. Together, we defined a set of solutions, techniques and materials to make the parts with maximum quality.
- We identified alternative materials that were equally functional but better suited for certain manufacturing challenges.
- We used CNC machining and vacuum casting to make high-fidelity copies of each part. These methods are the fastest and most economical solutions for creating low-volume plastic prototypes.
- We applied various surface finish treatments according to the needs of each part.
We discussed the details and possible design changes with the client before advancing with production. And every option we gave was supported by our extensive theoretical and practical expertise in manufacturing parts.
Material Selection and Identification
Based on our exploration of the project and our experience in the field, we made the following material suggestions:
- UP420 and UPX8400 to make the main part of the device’s housing. UP4280 is a polyurethane with mechanical properties similar to ABS plastic, and UPX8400 mimics a rubber elastomer.
- Polycarbonate (PC) to make the scanner pads. Originally, the project called for PMMA, but this would require an exhausting hand-finishing process for each piece, which would increase the time and cost of the project.
- PX522 HT to make the keypads. It is a UV-stable material that allows light to pass through.
Communication is key, so we made sure to share the composition data of the materials obtained through Positive Material Identification (PMI) with the client and get approval before we moved forward.
PMI is a method to ensure the project uses only conforming materials. It’s a crucial step that guarantees the performance of finished parts, appropriate behavior during production, and ensures regulatory compliance.
Take a look at some of the advanced measuring equipment used by Star Rapid to identify plastics in practice.
Once we verified all incoming raw materials, we could start fabrication.
Our Process: Manufacturing and Finishing the Vein Reader System
Part of the complexity of this project lies in the different methods required to create the finished parts. We can divide the project into two stages:
- Manufacturing the parts using CNC machining and vacuum casting.
- Finishing by polishing, painting, silk screening, and engraving.
Parts Manufacturing
Most of the project was carried out through a combination of CNC machining to cut blocks of rigid plastic and vacuum casting to make high-fidelity copies of the security system.
Vacuum casting is performed by:
- Creating a 3D solid of the CAD design for each part. This is the master pattern, which can be created through CNC machining or SLA/SLS 3D printing.
- Casting molds made from liquid silicone, resulting in an empty cavity in the exact negative shape of the master pattern.
- Filling the silicone molds with resin to produce high-quality, perfect copies. Silicone molds begin to degrade after about 20 casts, which is more than enough for the volume required in this project.
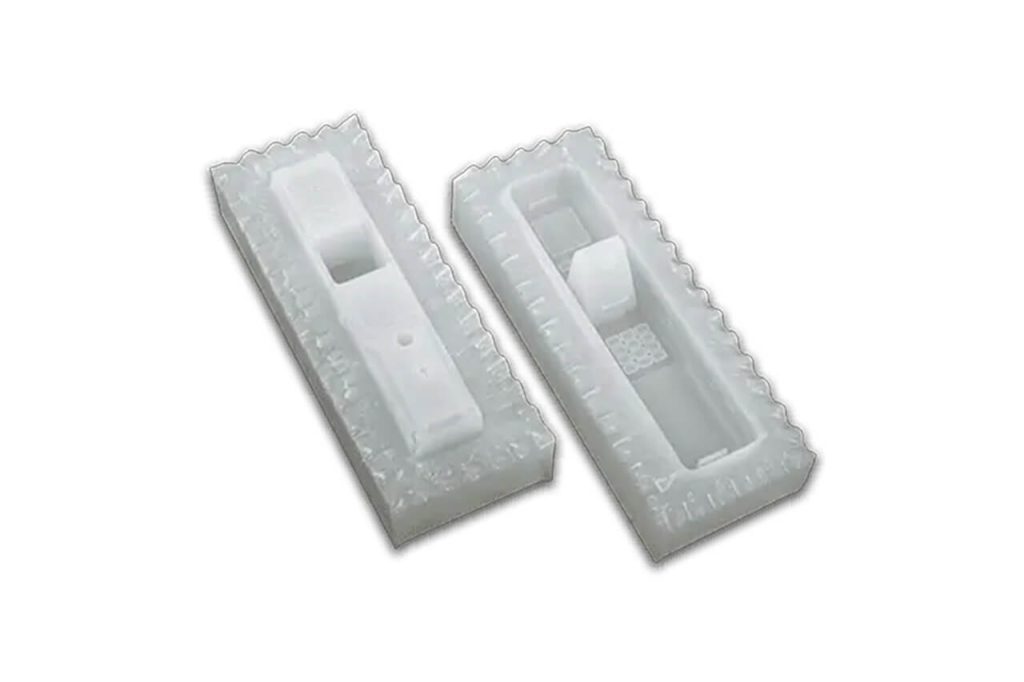
What’s interesting about the vein reader device is that fine surface details and textures were picked up directly from the mold. This approach requires careful work in building and polishing the master pattern, as any defect, burr, or machine marks would be replicated throughout production.
So after being removed from the mold, all vacuum copies needed to undergo some type of finishing treatment.
Surface Finishing
You typically have to remove excess material in the form of flash — which is created due to vacuum action during casting and is easily trimmed by our operators.
The housing’s main body needed additional hand painting on the light silver accented areas, but the pads for finger scanners needed to be transparent. To achieve that, we carefully vapor polished the polycarbonate pieces under tightly controlled conditions, resulting in perfectly clear plastic panes. The keypads were also painted, and the letters were laser engraved into the surface, allowing light to pass through. This approach is similar to production key manufacture.
Our skilled operators handled everything either in-house in our model shop, or with our partners under our direct supervision. Once finished, the parts were sent to our quality control department for final inspection before delivery.
The Result: Production Quality Prototypes—Done Fast
Our customers received 15 sets of the finger vein reader security system. These are complex parts, but they were created quickly and reliably due to:
- Smart material selection.
- Careful creation of master models and silicone molds that replicate them with precision.
- Open communication throughout the entire project.
All of this provided the client with real competitive advantages. They received parts ready for assembly and commercial presentation much faster and more economically, which means earlier market testing and fully finished products to be presented to potential investors or customers.
These results are impressive, but they’re not easy to achieve. They’re the product of millions of dollars invested in facilities, machinery, equipment, and highly trained personnel capable of conducting different manufacturing processes with the highest level of skill.
It’s all in the details. For example, consider our suggestion to replace PMMA with PC. In terms of functionality, both materials could meet the project’s needs, but the manufacturing of each one is an entirely different story. Our team knew that PMMA would require painstaking hand polishing on every small area of the part. With PC, we vapor polished it to the same result in a shorter amount of time.
Many manufacturers might lack the technical expertise to propose such a change. And many would prioritize speed over quality, disregarding design optimization opportunities. That’s not an issue with Star Rapid. We take the time to analyze every detail of the project before jumping into production.
We applied a similar approach in another project for creating security devices for doors. Read more in our case study on the Gate smart lock, where we developed a series of discrete parts for an all-in-one solution for home access.
Exceeding Expectations in Parts Manufacturing
Star Rapid has the expertise and technology needed to bring your products to life accurately, quickly, and cost-effectively.
Whether you’re in a rush or have a product with highly complex parts, submit your CAD files, and our engineers will get in touch and discuss what you need to achieve your goals.
You’ll receive an affordable quote with no minimum volume requirements. Once accepted, our specialists will help optimize your project, produce the parts, and deliver them right to your doorstep.