- Case Studies
- Dr. Scholl’s Case Study: Production for Hard Skin Removal System
Dr. Scholl’s Case Study: Production for Hard Skin Removal System
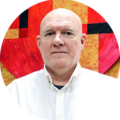
- Chris Williams
- 6 min
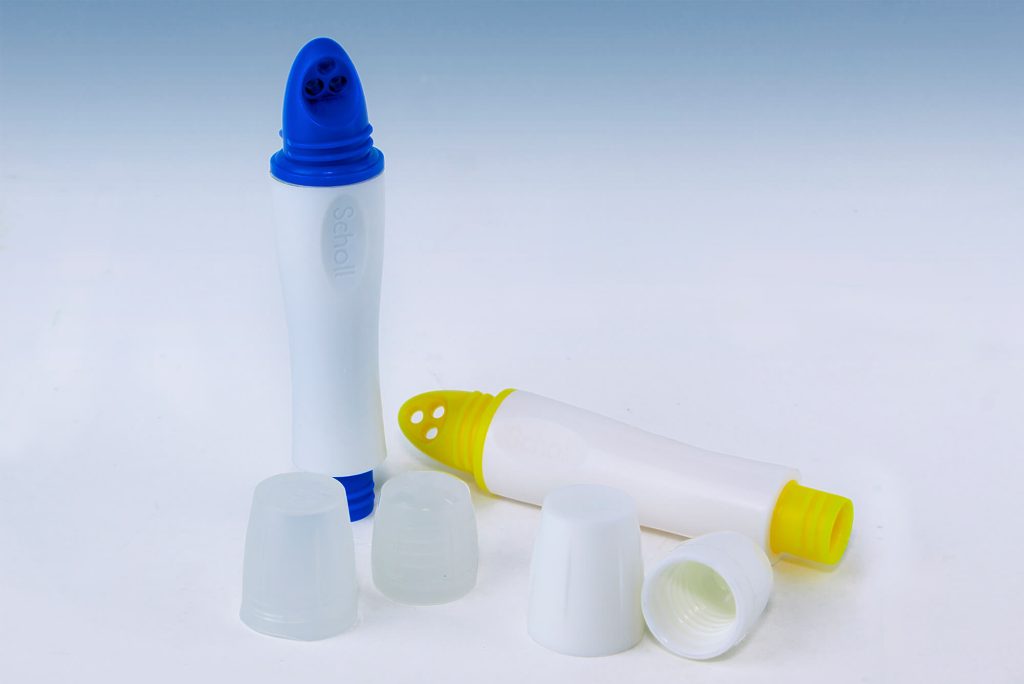
- Case Studies
- Dr. Scholl's Case Study
Dr. Scholl’s Case Study: Production for Hard Skin Removal System
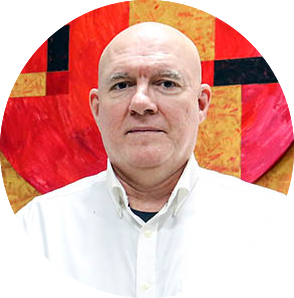
- Chris Williams
- 7 Mins Read Time
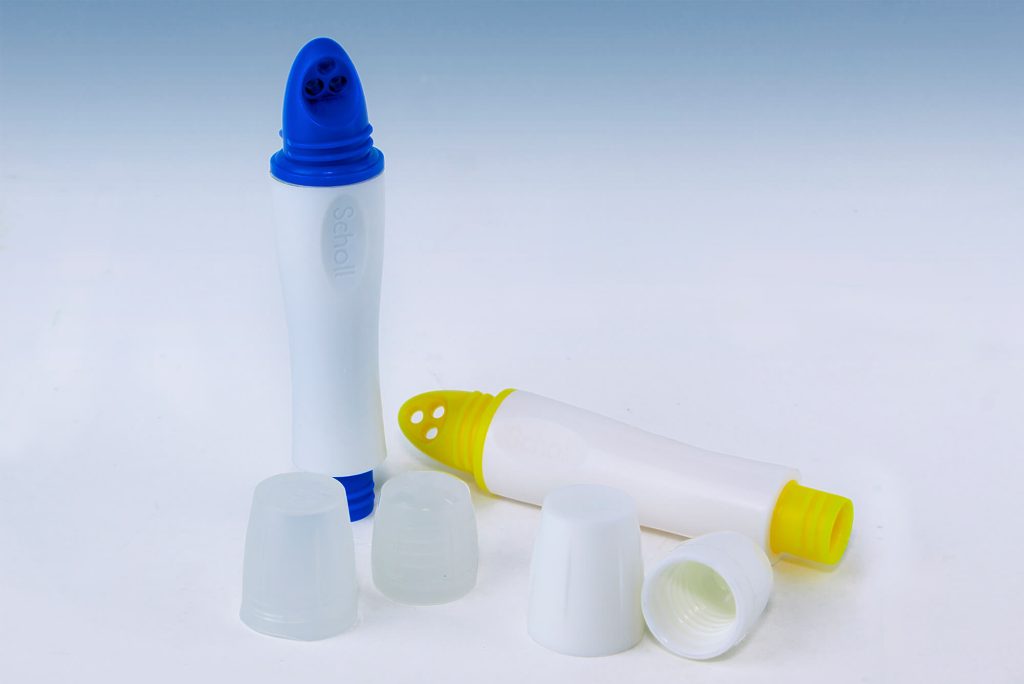
Table of Contents
ABOUT
DCA: Product Design Consultancy
Dr. Scholl's Inc: Foot Care Products
Industry
Consumer Products
Components
Tubular Handles
Threaded Handle Tops
Removable End Caps
Tool Material
Nak80 Steel
Parts Materials
Chimei ABS 757 Plastic
PP 5090T
Quantity
3000 Units
Lead time
4 Weeks
Services
Table of Contents
Table of Contents
“I first worked with Star in 2008 and was extremely impressed by the quality of work and the speed with which Gordon and his team were able to turn things around. When it came to the Scholl 2-in-1 project the complexity of the product and its parts, plus the quantities and timescales required, meant that Star was our first-choice partner for the job.”
Senior associate at DCA Design
Smoothing the Rough Spots with Dr. Scholl's: Creating Revolutionary Foot Care Prototypes
Those pesky patches of hardened skin underfoot seem to reappear no matter what. So Dr. Scholl’s set out to solve this common complaint with their innovative 2-in-1 foot care line. But bringing a revolutionary tool to market requires more than just a bright idea—it demands perfectly crafted prototypes that users can actually test and touch.
When DCA Design needed these crucial pre-production models to wow their first round of testers, they faced a ticking clock and exacting specifications. Enter our team’s expertise in design optimization, precision tooling, and injection molding. The result? A complex prototype that went from blueprint to reality in a few weeks, helping transform the future of foot care one callus at a time.
The Challenge: Optimizing Time and Costs
When DCA Design approached us, they were creating pre-production prototypes, and we understand that at this stage, the main challenges are time and costs. Since their client is a global brand, there’s an added challenge because all prototypes must match the look and feel of Dr. Scholl’s products that are already on the market.
In total, 3,000 parts were produced—which is a massive volume considering the project’s conditions.
And finally, the design of the parts added another layer of complexity to the build.
The white plastic tube shown above was particularly challenging to make, as it requires additional features on the injection molding tools.
Our Approach: Using Plastic Injection Molding for Parts Production
It sounds like a tough job, and really it is. In fact, many manufacturers shy away from demanding projects like these. But Star Rapid was easily up for the task.
In our years of experience with rapid prototyping and low-volume manufacturing, we’ve developed a philosophy and a structure capable of handling the most complex jobs quickly and inexpensively.
Our toolbox to help DCA overcome its production challenges consisted of the following:
- Design for Manufacturing Optimization
- Smart Material Selection
- Project Management
- Advanced Machinery
- Strict Quality Control
The parts were produced via plastic injection molding. This is the fastest and most cost-effective process for producing thousands of plastic parts, and it’s also a repeatable and scalable process, making it suitable for full production as well.
Our Process: Producing the Parts in 5 Steps
We produced the tubular handle, threaded handle tops, and removable end caps. The handle body should have an easy grip, a pure gloss white finish, and be debossed with Dr. Scholl’s trademark name.
To achieve this, we turned to our top 5 steps for stellar production:
- Reviewing Design Files
- Selecting and Identifying Raw Materials
- Tool Making (using CNC machining and wire EDM)
- Plastic Injection Molding
- Final Inspection and Delivery
1. Reviewing Design Files
All our projects start with a careful evaluation of the client’s design files. The goals are to:
- Identify the best manufacturing method.
- Optimize the design.
- Find opportunities to improve quality, performance, and costs.
After ensuring the manufacturability of the designs, we recommended making three mold tools from NAK-80 semi-hardened tool steel.
2. Selecting and Identifying Raw Materials
NAK-80 tool steel was a good choice for this project for a few reasons. It’s a strong tool steel that can withstand thousands of injection cycles with ease, and it’s readily available from local suppliers. We also know it’s not easily damaged by abrasive engineering thermoplastics, like ABS. And it can be finished to a high polish, achieving the glossy surface that DCA needed.
The resins used in the project were Chimei ABS 757 Plastic and PP 5090T. These are general-use thermoplastics with good resistance, stability, and easy processing.
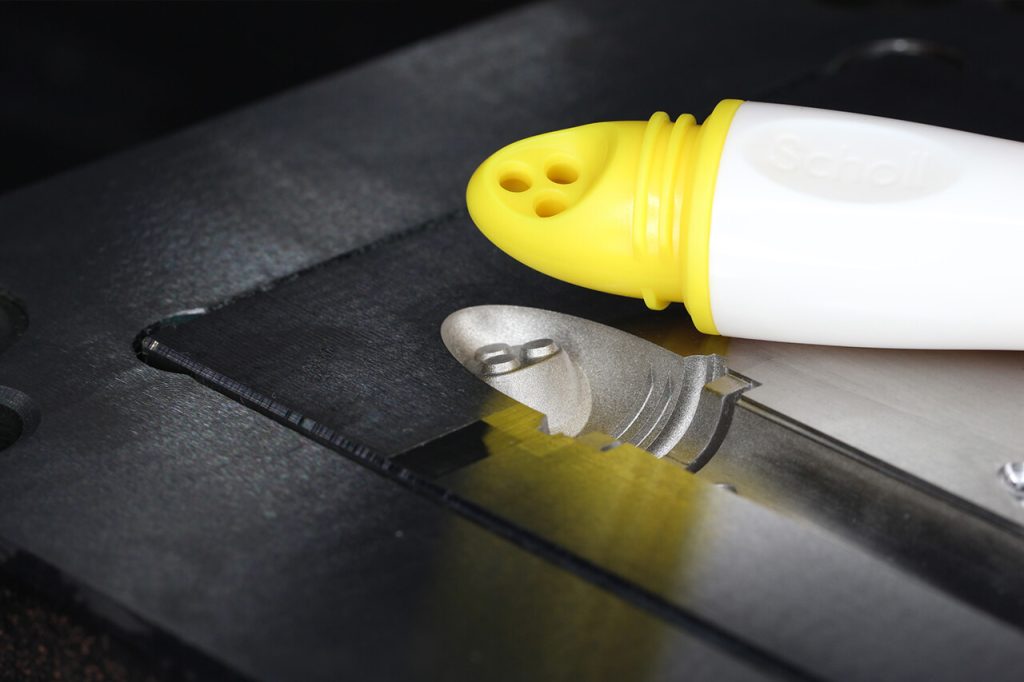
Next up was Positive Material Identification (PMI). We used advanced measurement equipment to analyze the composition of each steel and plastic used so that DCA Design — and all of us — knew we were working with the correct raw materials.
3. Tool Making
Creating the tools for the skin removal device was a complex task.
The central shaft of the Skin Removal System required threads at both ends, so we chose to work with an EDM (Electrical Discharge Machining) electrode that we made in-house.
Two additional molds were made, one for the end caps and one for the outer white handle, both injected from PP (polypropylene) 5090T.
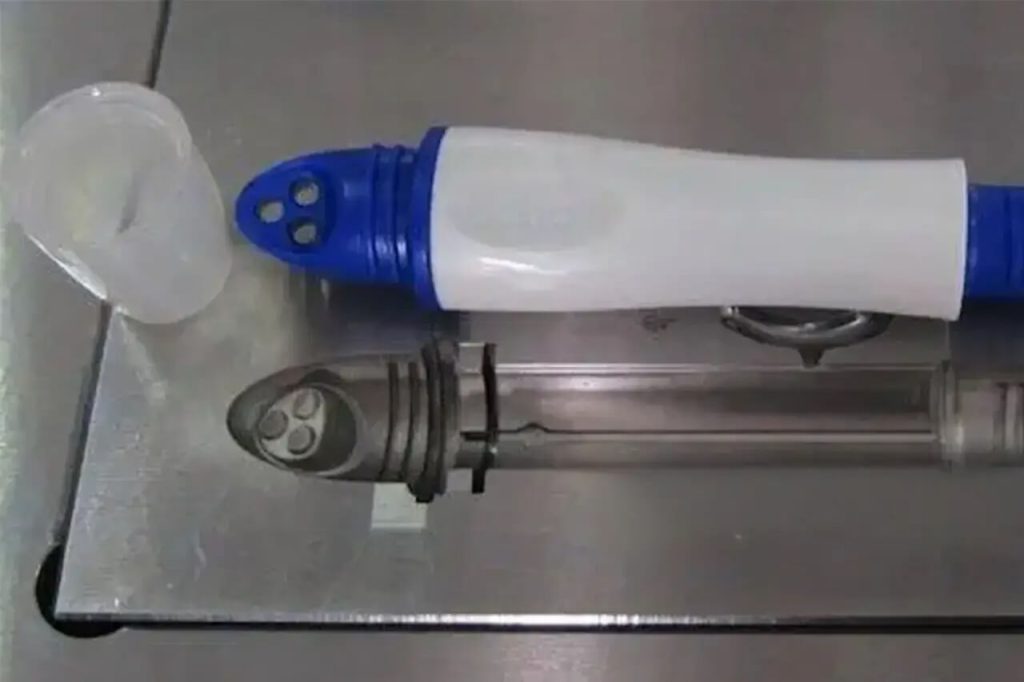
The outer handle required a tool with two cavities. After cutting, we had to hand-finish and machine the cavity side so that the injected plastic would have a glossy surface texture. This piece was then hand-assembled over the colored section to make a one-piece unit.
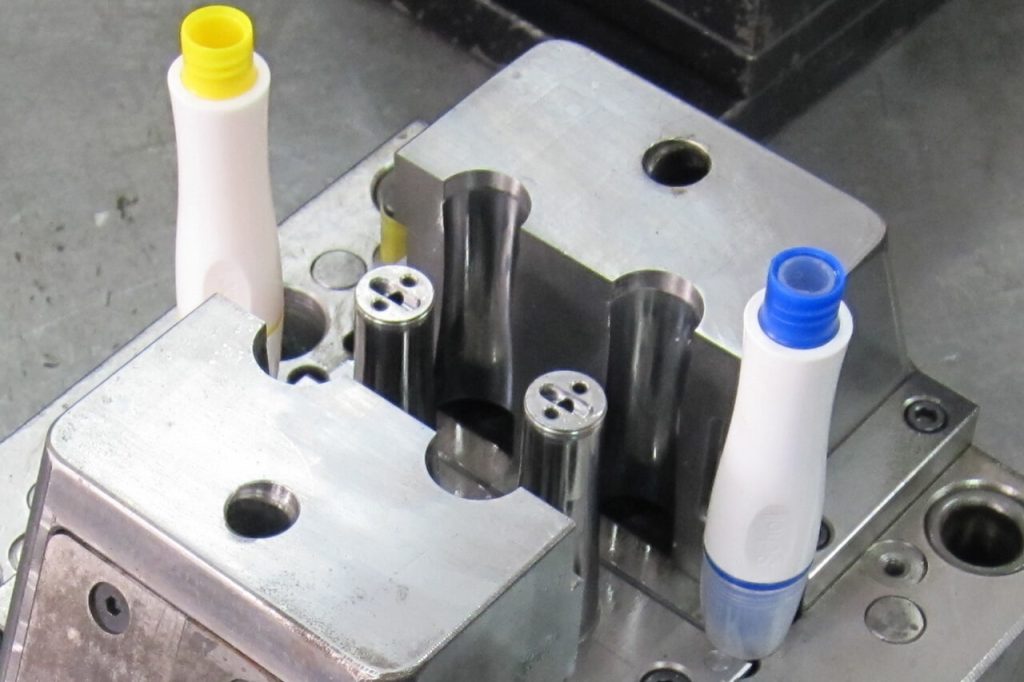
We also used hydraulic sliders on this mold tool to aid in the separation of the core and cavity due to the length of this piece.
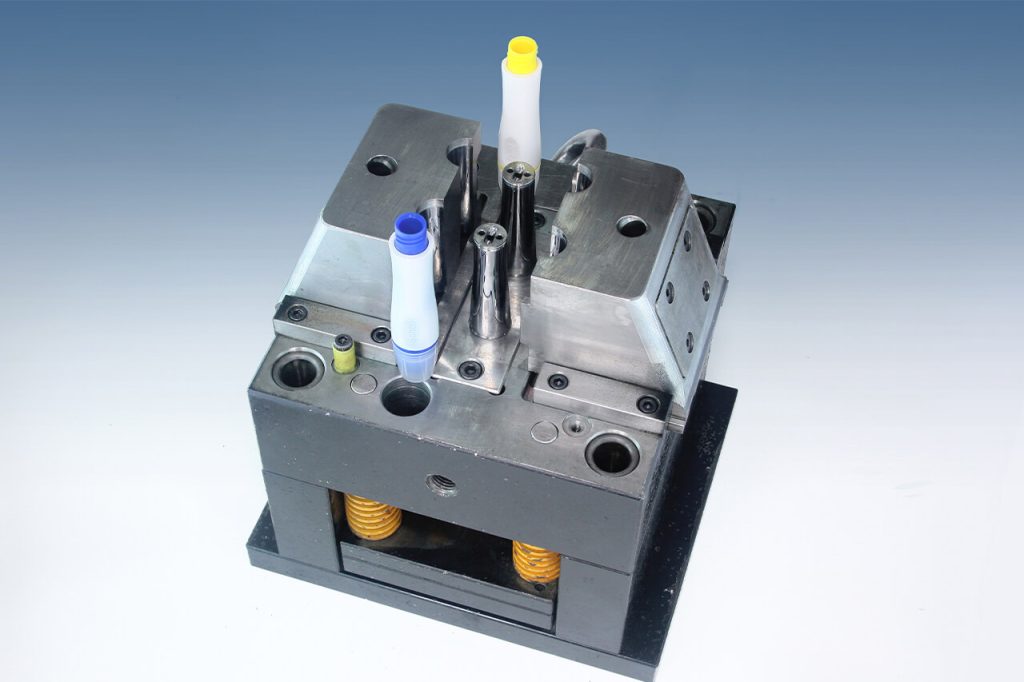
Note that we didn’t need to spend too much time or expense in finishing the cavity of this mold, because it would later be covered by the outer handle.
4. Plastic Injection Molding
The molds were trialed to verify the design and ensure the parts met expectations. Then, the samples were inspected and sent to DCA Design’s office in the UK. They wanted to test different colors of ABS for the end parts of the hard skin remover, so we sent them in blue and yellow ABS.
Upon the client’s approval, we started molding the other units.
The use of a multi-cavity tool was crucial for significantly reducing the cycle time and ensuring good color consistency. We know making these kinds of tools is time-consuming, but it saves valuable time during production.
5. Final Inspection and Delivery
After injection molding, the parts were sent to our quality inspection department for final tests before delivery.
The Result: Production of Quality Parts in 4 Weeks
Despite the complexity of the tools and parts, production fully met the quality, time, and costs expected by DCA.
- The tooling was completed in the first few days.
- DCA received the samples in the UK in only one week.
- 3,000 units were manufactured in four weeks.
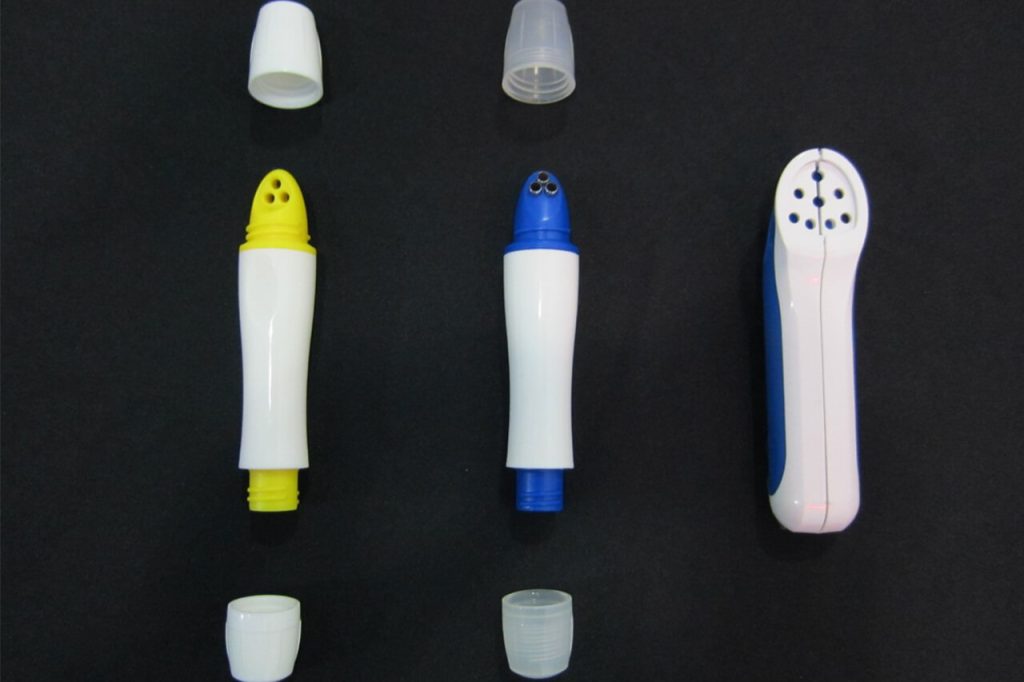
It’s important to note that this agility does not come at the expense of quality. Regardless of the project’s time frame, all parts were made with care in design optimization, tests, machine operation, and final inspection.
This commitment to quality gave us test parts with the same quality as the final version available in stores.
Get Your Custom Parts Today
Submit your CAD files today to get a detailed quote and discuss your project’s needs with our specialist team.
We’re ready to make your parts, no matter their complexity or time constraints, with scalable systems capable of producing one to one million parts with the same efficiency, quality, and refinement.
Whether it’s one-off proof of concepts, small volume samples, or pre-production prototypes, we’ve got the tools and expertise you need to hit the market early, without minimum volume restrictions.