Conformal cooling for plastic injection molding is emerging as a technology that could offer some great advantages for making mold tools. Because of this, our team at Star Rapid has been investing in research and development to provide this service in the future. Using advanced manufacturing techniques like metal 3D printing will make this solution more accessible than ever. In this article, we will explore how conformal cooling works and how it will shape the future of manufacturing.
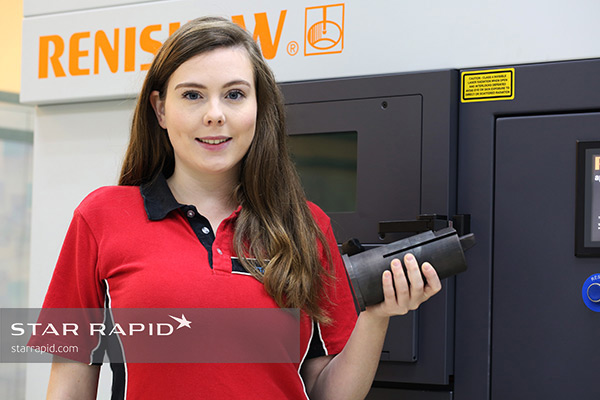
What is Conformal Cooling?
Conformal cooling is the process of using coolant channels in plastic injection mold tools which closely follow, or conform, to the shape of the part being molded. They differ from standard cooling channels in that they are not confined to the line-of-sight, straight holes that are created from conventional drilling or milling. Conformal cooling channels follow the twists and turns of complex part designs, and so offer much better cooling efficiency and faster cycle times.
How are Cooling Channels Made In Most PIM Molds?
The great majority of injection mold tools and dies are made with cooling channels that have been drilled or milled from a block of tool steel. This means the channels are in a straight line. After a part is molded, cold water is pumped through these channels in a circuit, which cools the core and draws heat away from the plastic.
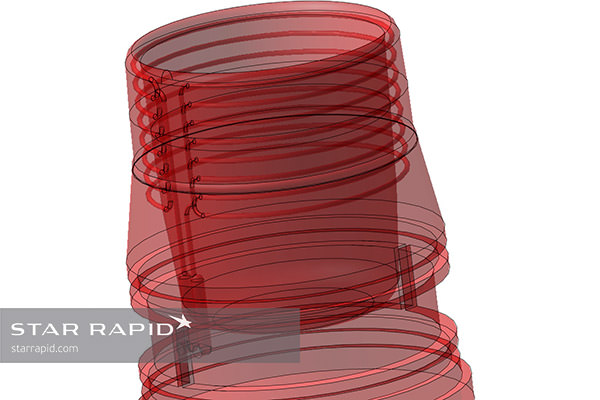
To be effective, these circuits need to be as close as possible to the wall of the tool where it contacts the molten resin. So if the part has nothing but straight walls, like a simple box, this is easily done. But most parts aren’t so simple. Tool designers therefore spend a lot of time trying to orient the build of the design so that the maximum number of straight lines can surround it to provide cooling. This process is usually a trade-off with many variables, but it’s always less than ideal.
Why is Cooling So Important for Plastic Injection Molding?
Successful injection molding depends on both uniform heating and cooling of thermoplastic resin. While it’s relatively easy to heat the resin until it’s molten, it’s much more difficult to cool it quickly and at a uniform rate. But this is critical for creating a finished part that’s free from thermal stress and all the defects that it creates – weld lines, warpage, sink marks, etc.
Cooling is also important because thermoplastic resin doesn’t like to be molten for too long. The chemicals rapidly degrade and can quickly become useless.
How Are Conformal Cooling Channels Made?
One of the best ways to make conformal cooling channels is with metal 3D printing. 3D printing can make complex internal structures impossible to make conventionally, so inserts for mold tools can be customized with cooling channels to fit the geometry of the part. They aren’t limited to a straight line so they can follow any curvature. Just as importantly, the cross-sectional shape of the channel can also vary anywhere along its length, something impossible to do conventionally.
We are researching direct metal laser melting as an ideal way to print next-generation mold tools or inserts, since this process creates finished parts from tool steels that are fully dense and durable – necessary to withstand the pressures of injection molding.
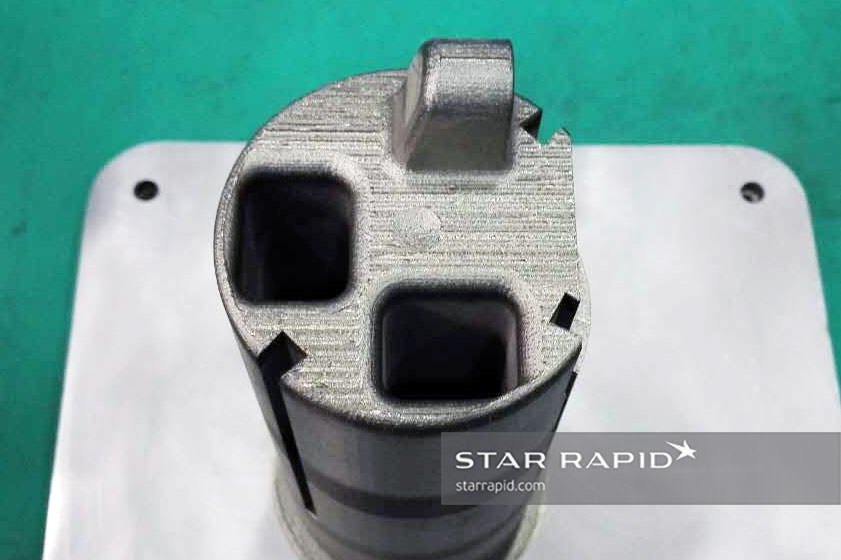
What Are The Other Advantages of Conformally Cooled Mold Tools?
Once the design has been optimized for efficient cooling, a tool or insert can be printed and post-finished in a matter of days, compared to weeks for conventional tools. The process also consumes less raw material.
Finished part quality using this type of tool can be far superior, with fewer molding defects. And because the tool heats and cools more quickly, cycle time is reduced. This can be a real cost savings for high volume production, and can more than make up for the cost of the tool in the long term.
Are There Any Disadvantages To Making Conformally Cooled Mold Tools?
There are some limitations to consider, especially for rapid production. 3D printing is likely to be more expensive than conventional CNC machining, and requires more careful engineering. This may involve using sophisticated analysis software like Moldflow® to determine the optimal design for drawing away heat most efficiently. Because of the careful engineering required to get the best results, preparing a 3D printed tool will take more time than a conventional counterpart.
The tool size will also be limited to the size of the print bed, which on most printers is smaller than a standard machined counterpart. And finally, there are fewer choices of raw materials, so common tool steels like NAK80 or P20 aren’t available as a print media.
Is Conformal Cooling Right For You?
We continue to actively pursue research and development of conformal cooling and hope to offer the service in the near future. If you think this is a process that might work for your tooling project, ask our engineers about the benefits when you next contact us for a free quote.