Though the world of parts manufacturing is large and complex, all manufacturing processes use one of four primary production strategies: volume-based production, strategy-based production, platform-based production, and method-based production. Each strategy consists of manufacturing methods showing how virtually everything is made in the modern world.
To truly understand these processes, we’ll explore the mechanics of converting raw materials into finished products on an industrial scale—everything from physical fabrication and project planning to ideation, design, and prototyping.
Here, we’ll examine the logical organization of the different types of manufacturing processes, giving you insights into how to prepare for your next product development project.
Understanding Custom Parts Manufacturing
By understanding the four main production processes for parts manufacturing and taking a closer look at the types of manufacturing strategies within each, you’ll notice that some strategic approaches are better suited to one kind of process than another. Soon, you’ll be better equipped to make an informed decision when producing your own custom parts.
Production Strategy 1: How to Choose the Right Volume-Based Production
Your strategic manufacturing method may depend on the volume of custom parts needed. Low-volume prototyping is great for small batches or highly customized products, while medium-sized production runs and full-scale continuous mass production may require discreet, continuous, or repetitive manufacturing strategies. Each category of volume-based production is optimized to provide efficient and cost-effective manufacturing techniques.
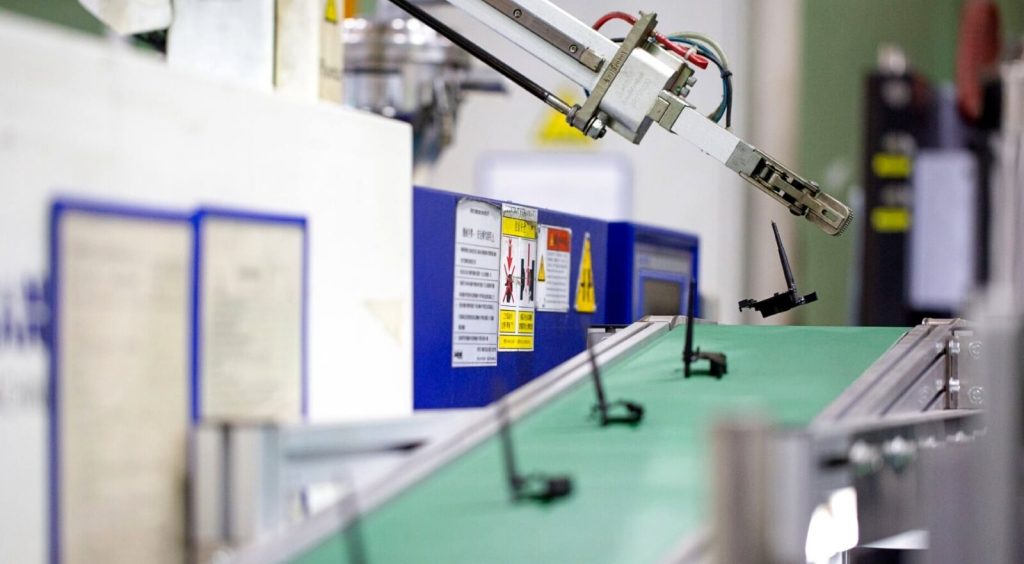
When to Choose Low-Volume Manufacturing
Suppose you need a single part or up to 1,000 parts. In that case, low-volume manufacturing requires a highly flexible environment ready for rapid process alterations, short production lead times, limited fixed tooling, and unrestricted access to various raw materials without minimum order quantity restrictions.
The price per piece tends to be higher for low-volume parts, and each part may have a longer lead time because the service isn’t optimized for throughput. This method of manufacturing is supported by these two types of output:
Batch Manufacturing
Publishing is a good example of batch manufacturing, where a single print run might represent the total volume of books of that type that will ever be printed. This production process handles the total volume of one product in a single batch, and the order may be shipped to the customer right away or held in storage for partial shipments.
Job Shop Manufacturing
Job shop manufacturing is typically used for highly customized products made to order in limited quantities. Instead of a production line, individual specialists make each part separately. This production process works best on fast turnaround orders to serve small, localized geographical regions, but it’s not suited for mass production.
When to Choose Medium-Volume Manufacturing
As volumes increase, it may make more sense to invest in fixed tooling, like injection dies or holding fixtures, and allocate resources for semi-permanent production lines. Medium-volume projects that require between 1,000 and 50,000 pieces can also take advantage of pricing discounts on raw materials and other input costs, an option that isn’t available for low volumes.
When to Choose High-Volume Manufacturing
The highest volumes of mass consumer goods—commodities like toothpaste or water bottles—are made in dedicated factories that are set up to maximize economies of scale with purpose-built machine tools and optimized supply chains.
The 3 Medium-Volume and High-Volume Manufacturing Strategies
1. Discrete Manufacturing
Smartphones and other smaller consumer goods require flexible machinery and equipment that can be reprogrammed quickly to work with many materials, shapes, and sizes. This discrete manufacturing resembles an assembly line, easily altered to suit different varieties or types of products.
2. Continuous Manufacturing
The factory that manufactures your breakfast cereal runs all day, every day. This continuous production process in manufacturing is highly automated, and there are usually multiple parallel fabrication lines that can continue output even if one of the lines experiences a temporary failure.
3. Repetitive Manufacturing
Similarly, repetitive manufacturing also runs for long periods of time at high volumes but may be switched on or off depending on cyclical demand. Large daily newspapers use this method to print millions of copies per day, but printing will pause between each day’s news cycle.
Production Strategy 2: Making Strategy-Based Production Decisions
The demand for a product, the level of personalization, and even the complexity of its assembly can all affect how you prepare for future orders. So, a full understanding of the manufacturing processes or platforms that best suit them is critical to strategy-based production.
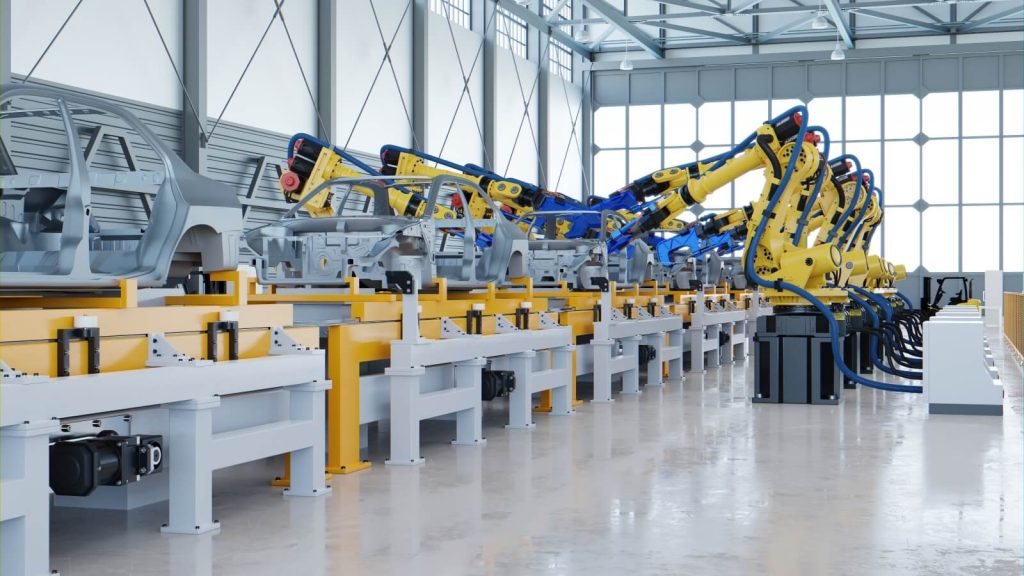
Made to Assemble
For things like home appliances that require complex assembly, the best strategy is to make all the separate components in advance and place them in stock until an order arrives. However, this type of manufacturing requires discipline and careful control of the supply chain. The high number of discrete components poses a risk since these parts may come from many different vendors, each with different production lead times or who might face supply chain interruptions. If even a single component is missing, the assembly can’t be completed.
Made to Order
For very personalized or custom orders, a made-to-order strategy where the end-user can specify their exact requirements in advance is often the most appropriate. The piece price may be higher, with a longer delivery lead time—but that’s the cost of personalization. However, manufacturers who offer this service, say for custom furniture, can compensate by mixing and matching modular components.
Made to Stock
In the case of items like respirator masks, where the demand can be reliably anticipated before cold and flu season in winter, manufacturers may choose a made-to-stock strategy. In this case, the entire production volume is made in advance and held until the orders come in. But while the manufacturer has time to avoid delays in production or raw material delivery, they also run the risk of having unsold stock.
Production Strategy 3: Intro to Platform-Based Production
New production platforms combine emerging technologies like AI and augmented reality with integrated systems like Industry 4.0 and the Internet of Things, creating hybrid manufacturing processes combining the best digital and conventional solutions.
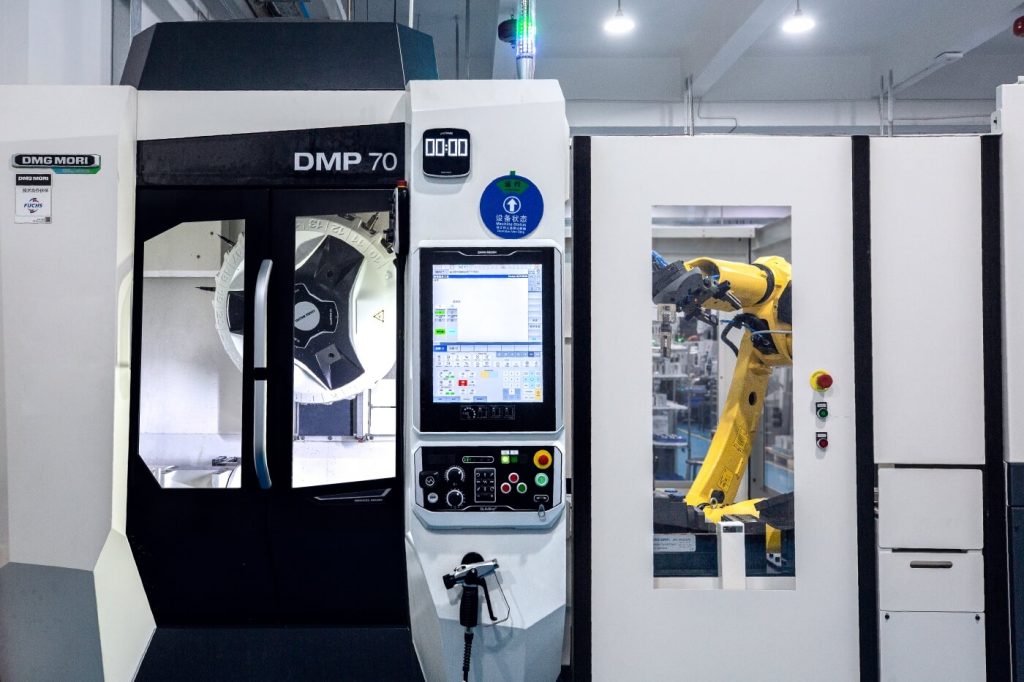
Digital Manufacturing
Processing equipment, machinery, materials, and human resources can all be tied together into a virtual network using computers, sensors, and software. This helps managers to plan and allocate resources efficiently, thereby minimizing waste, reducing cycle times, and quickly spotting bottlenecks. Our digital manufacturing guide explains this manufacturing method in more detail.
Cloud Manufacturing
In this platform, the customer uploads electronic drawing files to a cloud server managed by a manufacturing service provider. This provider has access to hundreds or even thousands of partner factories that can bid on and execute the project.
Cloud manufacturing is a cost-effective solution for making relatively low volumes of simple designs with short production lead times. But, it’s not ideal for complex parts that require more stringent testing and quality control.
Conventional Manufacturing
Conventional manufacturing is stable and produces reliable quality, but it’s not as flexible in terms of design or materials. Many traditional factories still operate according to the older model, with large industrial equipment operated by skilled technicians who consistently make the same or similar products.
Production Strategy 4: Understanding the 6 Main Manufacturing Methods
With a wide array of manufacturing methods used to produce consumer and industrial goods, we’ll focus on the six that apply to discrete finished objects, leaving out, for now, any continuous process manufacturing that involves liquids, gasses, oils, powders, or other substrates that are modified via chemical or biological reactions.
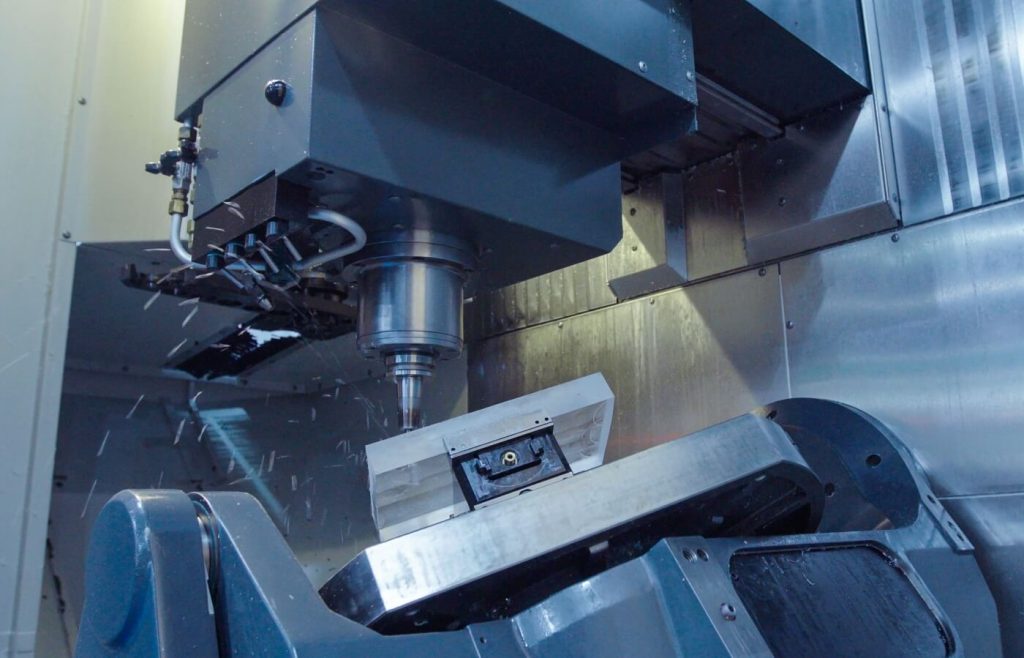
1. Additive Manufacturing
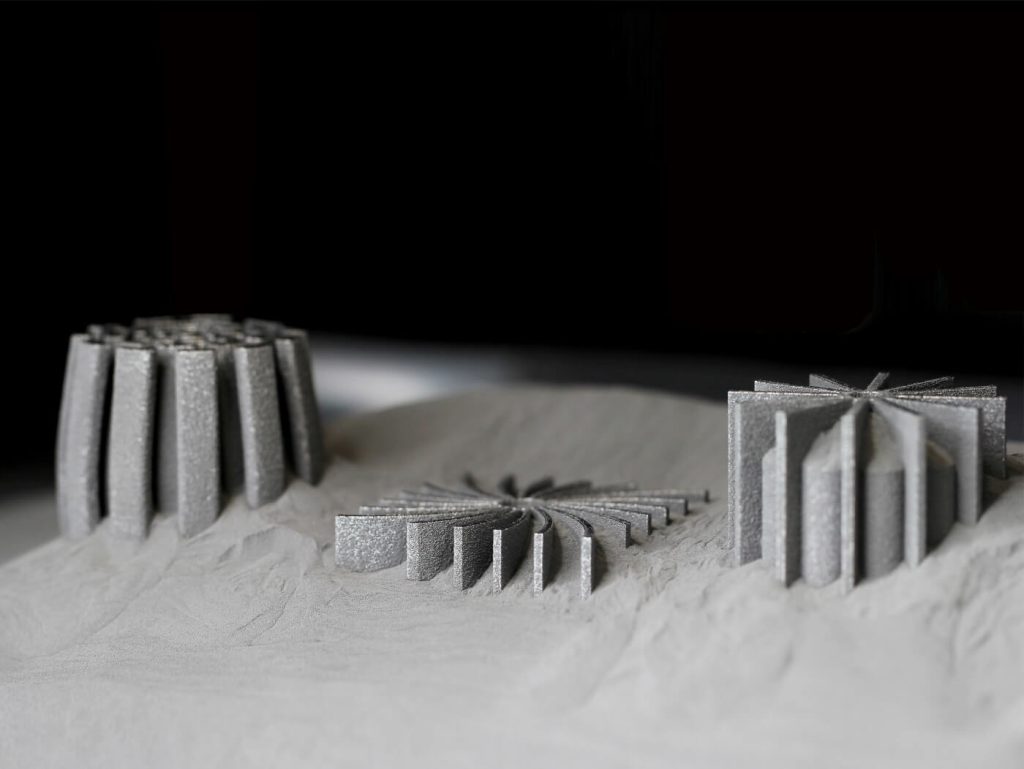
Typically called 3D printing, additive manufacturing can produce finished geometries that are difficult, if not impossible, to make conventionally. This method of manufacturing is used to create a part using the controlled deposition of two-dimensional layers of a substrate, which are then fused together to form a three-dimensional whole. It’s ideal for low-volume production or rapid prototyping. But, the part quality usually requires secondary finishing, and it’s not recommended for high-volume production.
2. Subtractive Manufacturing
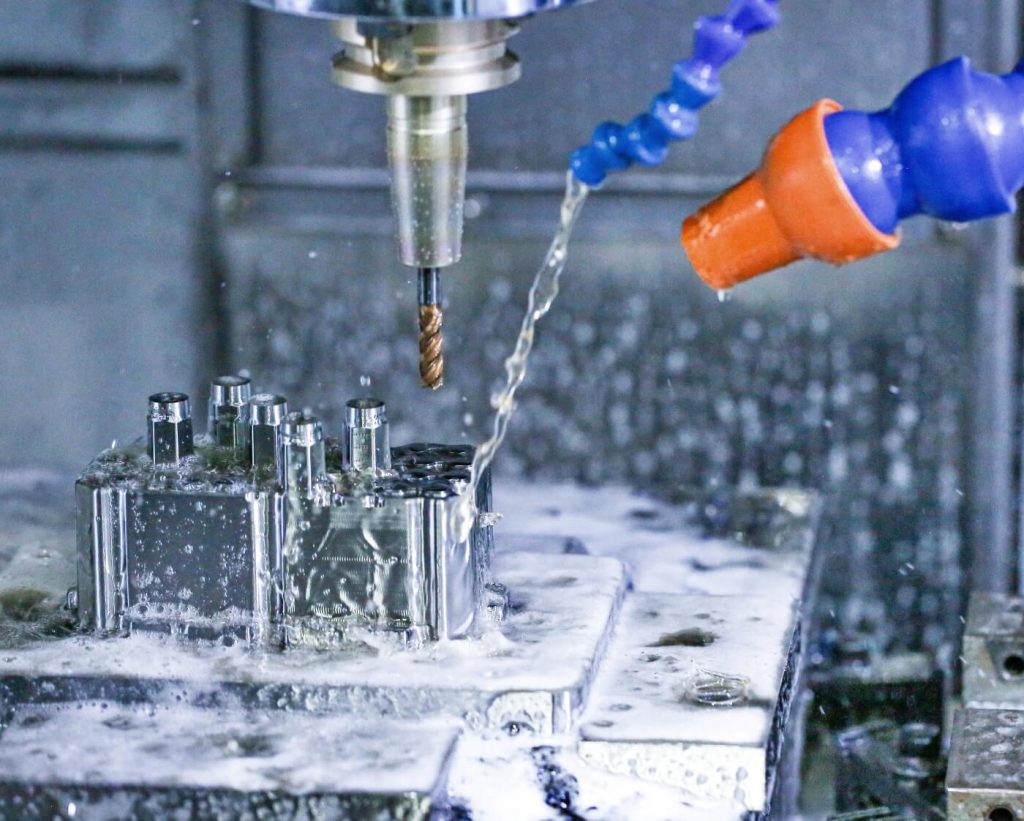
Manufacturing techniques like CNC machining are subtractive processes that create finished parts by selectively removing stock from a block of solid raw material substrate. These techniques include:
- Chemical Machining: Chemical solvents and masks are used to etch away hardened surfaces quickly.
- Electrical Discharge Machining (EDM): High-energy electrical sparks erode material from the surface of a mold tool. It’s beneficial on very hard materials that are almost impossible to machine conventionally. Learn more in our EDM machining guide.
- Grinding: In this manufacturing technique, a precision abrasive wheel removes layers of material from the workpiece, resulting in extremely flat and smooth surfaces.
- Milling: Cutting tools are rotated on high-speed spindles to form complex geometries on solid materials. Our CNC milling guide has all the details on this manufacturing process.
- Turning: CNC turning is a natural complement to milling, but in this case, the cutter remains rigid while the workpiece is rotated on a central axis. Both milling and turning are typically controlled by digital CNC programs.
Other manufacturing techniques used to selectively remove material include water jet cutting, laser cutting, and wire cutting.
3. Casting
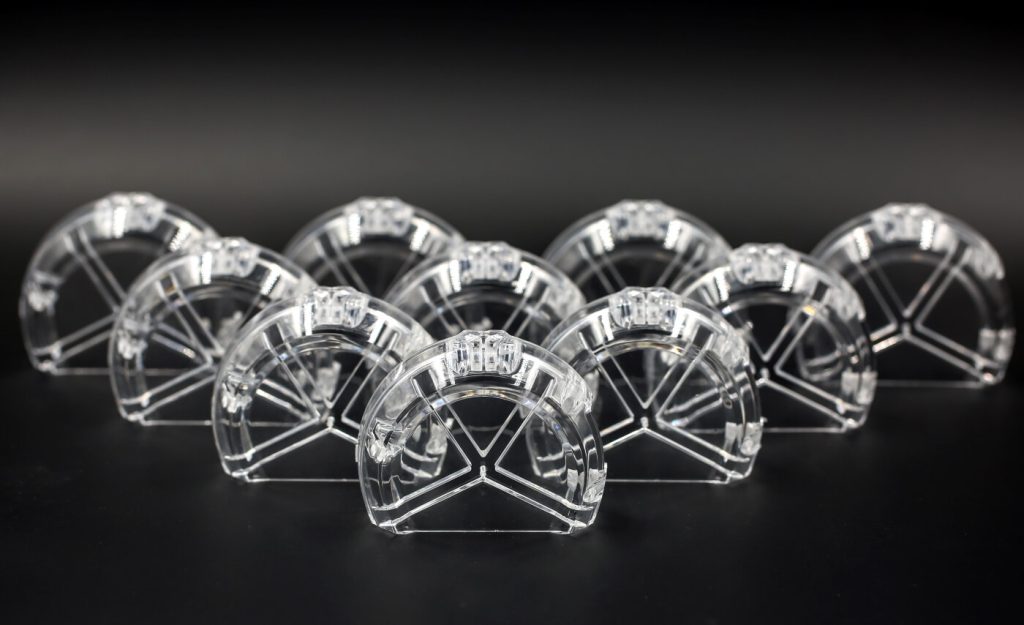
Casting is an ancient manufacturing method in which a liquid substrate is poured into a dedicated mold called a casting die and allowed to harden, thereby forming a negative image of the die’s internal shape.
- Centrifugal Casting: A mold is continuously turned while hot metal is poured inside. It’s used for producing cylindrical and round objects like pipes and ball bearings.
- High-Pressure Die Casting: In this high-volume manufacturing process, molten metal is injected into a two-part die made of hardened steel. Die casting is fast, wastes little material, and creates excellent details and surface finishes.
- Investment Casting: First, a wax pattern of the desired finished product is made, then surrounded with a refractory material to create a mold. Molten metal is poured into the mold, destroying and displacing the wax pattern to form a copy of the design.
- Vacuum Casting: A silicone rubber mold is formed around a master pattern. Once the mold is cut open and the pattern is removed, a cavity is revealed that can then be filled with pourable plastic resin analogues. Read more in our vacuum casting guide.
4. Plastic Molding
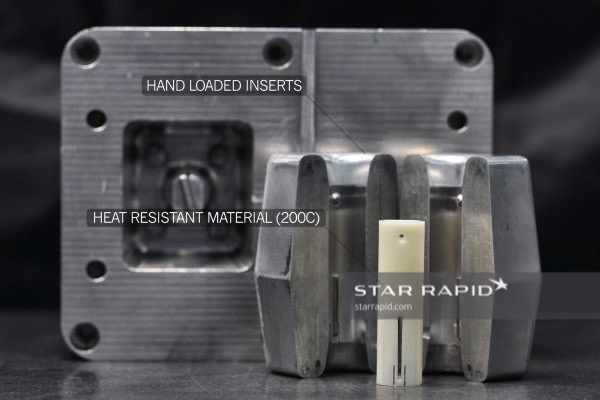
Plastic molding converts raw plastic resin substrate into solid finished parts through one of the following manufacturing methods:
- Blow Molding: Softened plastic is placed into a mold and inflated with air to form hollow cavity shapes, such as containers.
- Compression Molding: Sheets of semi-cured elastomer (rubber-like) plastic are placed into a clamshell mold, which is closed and heated to form flexible membranes and gaskets.
- Extrusion: Soft plastic is pushed through a die to form products with a continuous cross-section, like pipes, tubes, and weatherstripping.
- Injection Molding: Plastic resin granules are melted and injected into a dedicated die, where they are cooled into a finished solid part.
- Rotational Molding: Plastic resin pellets are placed in a hollow mold, heated, and rapidly spun to form large, hollow vessels and enclosures.
- Thermoforming: A thin, heated sheet of plastic is draped onto a forming mold and allowed to cool and solidify. This manufacturing technique is used for many types of disposable packaging.
5. Forging
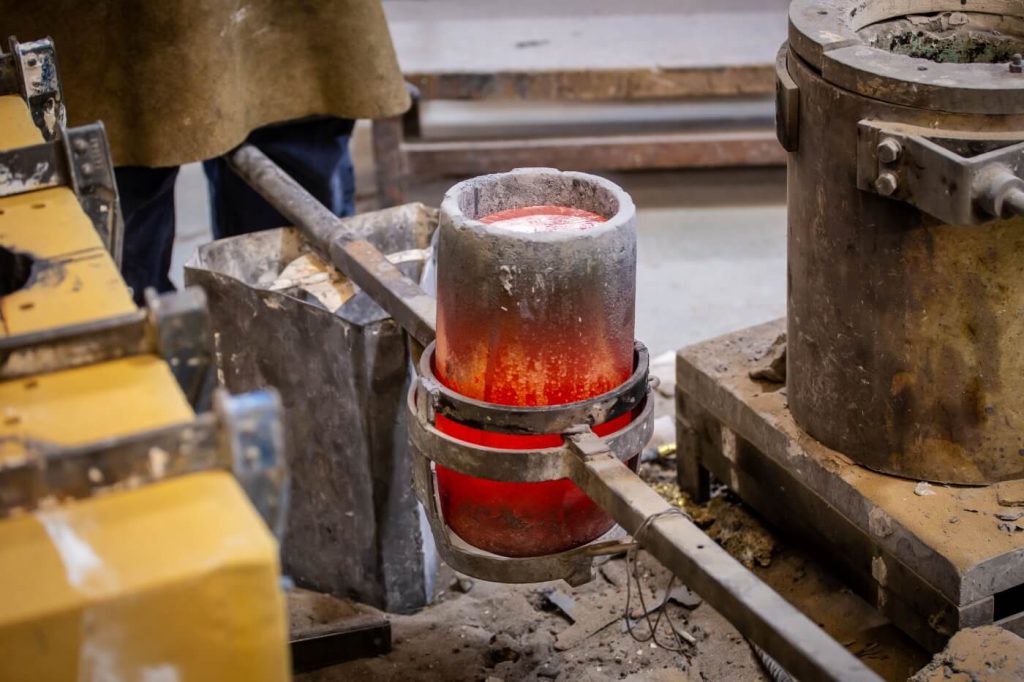
Forging is used to shape metal and is one of the earliest manufacturing methods. It requires the metal to be heated until soft and then reworked using a hammer.
- Closed-Die Forging: This process encases the material fully in a die except for where the hammer strikes. This process is generally used for highly specialized tools and parts.
- Open-Die Forging: This process heats and strikes the workpiece with a hammer, as with blacksmithing.
6. Powder Metallurgy
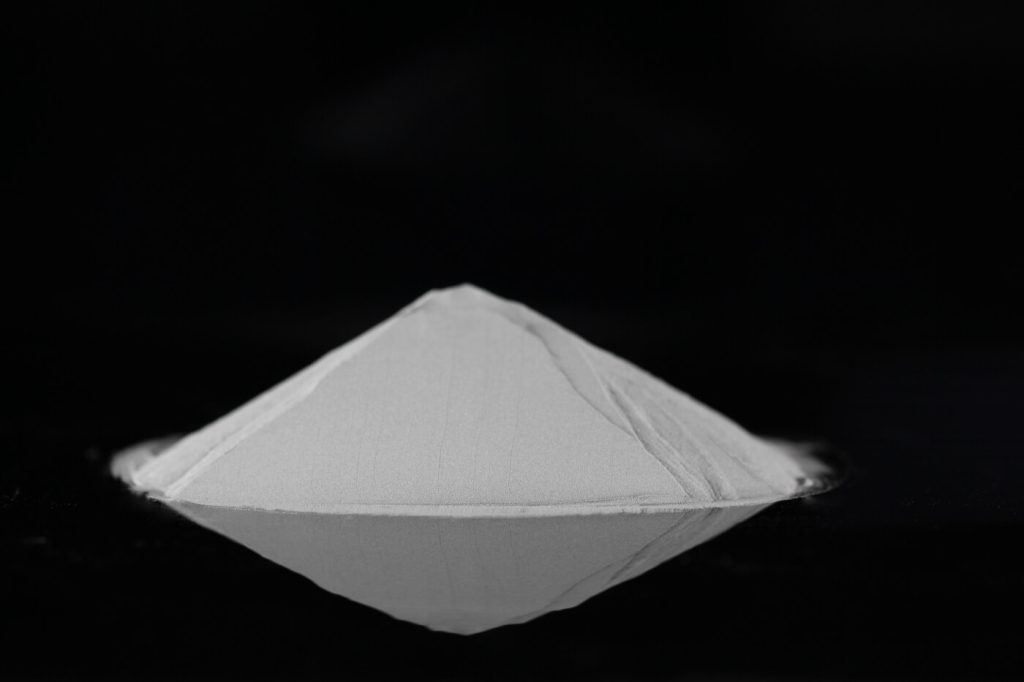
Fine metal powder can be formed into complex solid parts by:
- Powder Compaction: Compressing metal powder under extremely high pressures inside of a forming die.
- Powder Injection Molding (PIM): Metal powder is mixed with a binder, injected into a mold under high pressure, then treated to remove the binder. This technique is well-suited to small machine parts and can also be a form of 3D printing.
- Sintering: Heating a powdered metal to the point where the atoms chemically bind themselves in a coherent shape. It’s often used to create small electrical parts.
Taking the Next Steps in the Manufacturing Process
By sorting the types of custom parts production into four main categories, it’s easier to break down the complexity of the volumes, strategies, platforms, and methods used in the manufacturing process. Diving into each of these categories not only gives us a broader picture of the methods used but it also helps us understand which techniques are more suited to mass production of commodities and which ones are best for making smaller volumes of custom parts or prototypes.
Now that you’ve got a solid foundation, you’re ready to plan your custom parts manufacturing project. Check out these comprehensive guides to take the next steps on your product development journey on the Star Rapid Blog.