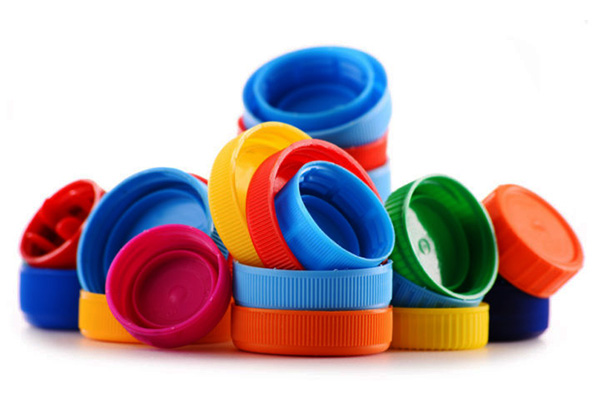
When considering plastic injection molding for a project, product designers and engineers should consider not only what thermoforming or thermoplastic resin to use but also the choice of metal for the injection mold tool.
The choice of tooling raw material influences production lead times, cycle times, finished part quality and cost, among other things. To help you decide which one is best for your next project, here’s a look at our most common tooling material types and the pros and cons for each.
Plastic Injection Molding Materials
Al-7075
Aluminum 7075 is a high-strength aluminum alloy with a relatively large percentage of zinc.
Pros
Aluminum has the best heat transfer properties of common tool metals. Why is this important? It means the tool can be heated and cooled quickly and efficiently. This has two advantages. First, the tool will require the least elaborate (and expensive) engineering for cooling channels. Secondly, it can be cycled more quickly than a steel counterpart, which can save significant time for larger production runs.
Cons
It’s the least durable tool material. It’s not suitable for injecting corrosive resins like POM or PVC, or those with glass fibers added to them, as glass fibers will erode the mold surfaces. This is less important with low-volume or bridge manufacturing where durability is not the chief concern. Also, 7075 is not good for withstanding high clamping pressures repeatedly, such as would be used for large parts or those with many complex features.
Best For
Low volumes of general purpose resins like ABS, PP, PE and nylon.
P20
P20 is a reliable, semi-hardened tool steel and the type we use most often.
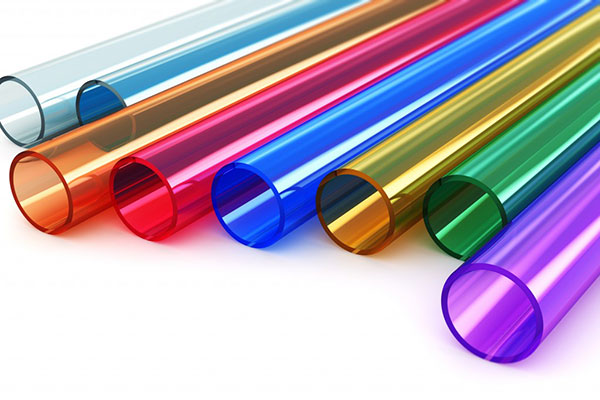
Pros
It’s less expensive than Al-7075 and even with abrasive resins it can last up to 50K cycles or more depending on the part’s geometry and tolerances. It also machines well and can be easily welded for repairing the mold, if needed. It can be polished about as well as Al-7075, but it’s more resistant to scratching than aluminum. It’s also tougher so it can stand up to higher injection and clamping pressures. P20 also fares much better against glass-filled materials than Al.
Cons
There are some plastic resins like PVC which are chemically corrosive. P20 steel is not very resistant to these so this can impact tool life. In some cases, aluminum can be slightly superior.
Best For
General purpose resins, abrasive resins with glass fibers, larger parts, higher injection and clamping pressures. Volumes up to 50K.
General purpose resins, abrasive resins with glass fibers, larger parts, higher injection and clamping pressures. Volumes up to 50K.
NAK80
Pros
It’s tougher than P20, while also machining much faster. It holds tight tolerances and doesn’t need to be stress relieved, even after 250K cycles. It’s also more corrosion resistant.
Cons
A potential disadvantage is that it has poorer heat transference so it needs to be cooled more carefully, and it will cost more than AL-7075 or P20.
Best For
Engineering-grade plastics like Delrin or acetal (POM), corrosive resins, high-volume production with high clamping pressures, resins with glass fibers.
H13
Another excellent choice for larger volume production orders or where aggressive plastics are used is H13 air-hardened tool steel.
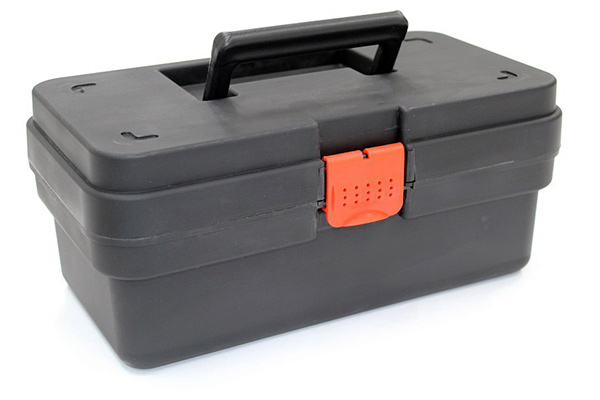
Pros
This is considered a “hot work” steel, meaning that it has excellent resistance to the stress of continuous heating and cooling cycles while holding close dimensional tolerances. H13 is easy to machine prior to heat treatment when the metal is relatively soft. Once heat treated, molds are further processed and finished using EDM and hard machining techniques. H13 can be used a million times or more per mold. It can also be polished with a mirror finish for clear or optical parts.
Cons
Its disadvantage is that it has only average heat transference ability and it will be more expensive than Al-7075 or P20.
Best For
Aggressive resins, optical parts made of clear plastic like acrylic or polycarbonate, high volumes.
S136
S136 is a high-purity stainless steel that comes in various degrees of hardness.
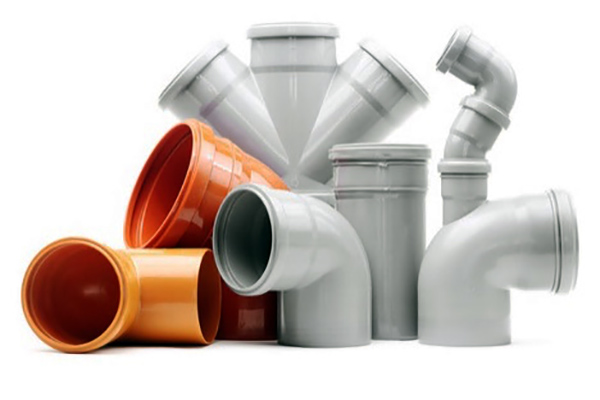
Pros
It’s the most corrosion resistant when injecting PVC or POM plastics which can potentially eat away at other metals. Also, it can be polished to the highest degree, ideal for making optically clear surfaces in transparent plastics like polycarbonates and acrylics.
Cons
These advantages will be offset by the highest cost of our available tool materials, and the lowest thermal efficiency.
Best For
PMMA, PVC, PP, PC and other optical-grade transparent resins. We recommend this steel when surface finish is the primary consideration.
Still not sure which one is right for you?
When you upload your 3D CAD files for a free quotation on your next plastic injection molding project, we’ll review your design and your choice of resin, and work with you to help ensure you choose the material that fits your budget, timeline and expected results.
Tagged: