Plastic injection moulding is the industry’s most common way to manufacture parts. This production method is particularly popular when manufacturing in large quantities. Weld lines are a common imperfection to be found in most plastic injected molded parts. They are the result of fundamental physical effects taking place inside of the mold tool cavity. Although they often cannot be avoided it’s possible to minimize their cosmetic effects to an acceptable degree through careful product design and manufacturing process control. Let’s first look at what the weld line is and how it’s caused.
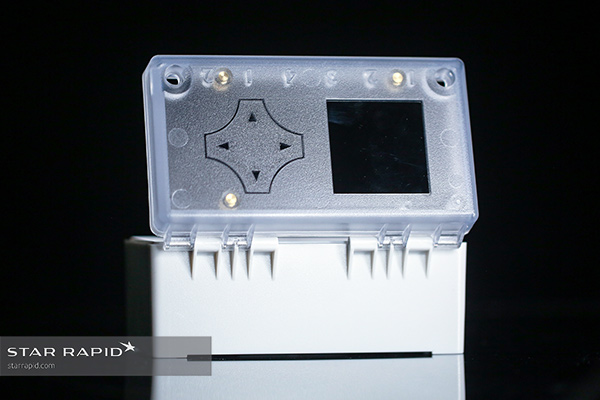
What Is A Weld Line?
A weld line is a mark left on the surface of a plastic injected molded part. Usually it’s a straight line, and often to be found radiating away from a hole, inclusion or other such part feature. This gives a clue as to how it was formed.
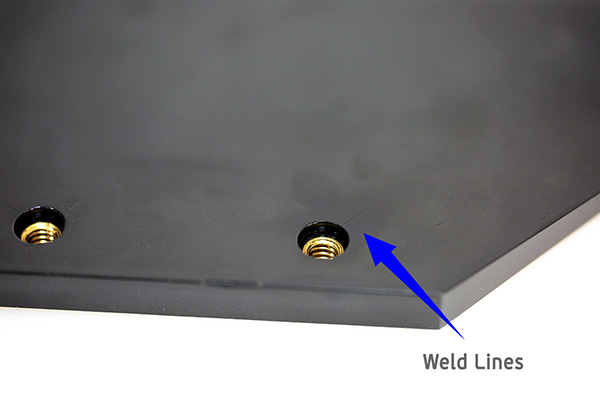
How Are They Formed?
Molten plastic resin is injected into a mold cavity through an opening known as a gate. From this gate the plastic is pressurized to fill the entire cavity to the limit of the cavity walls. These walls are cooled via cooling channels in the tool.
When molten plastic contacts these relatively cooler surfaces it will begin to harden and form the solid plastic shape that’s desired. However, what happens when the flow of liquid resin doesn’t move in one continuous unbroken path from the gate, but rather is forced to proceed around an obstruction such as a hole?
Then the path diverges into two channels, which meet up again on the side away from the gate. These two faces are pressed together, but they will be at unequal temperatures. Why? Because the plastic resin has already had time to contact the cooler tool walls and therefore has already begun to partially solidify. This solidification prevents the two faces from mixing completely and causes the characteristic weld line.
The process becomes more complicated with additional part features and gates, each of which introduces new flow fronts and hence weld lines.
How Can They Be Controlled?
The molding machine operator can mitigate the effects of weld lines by some combination of controlling the molding temperature, varying the gate pressure, and increasing the dwell time – all of which are intended to balance out thermal stresses as much as possible. There are trade-offs, however. Longer molding time and higher temperatures tend to degrade the plastic resin and will increase processing costs. Alternately, more advanced methods of cooling can be used, like using cyclic cooling or conformal cooling channels. However these will also add to the cost of the tool.
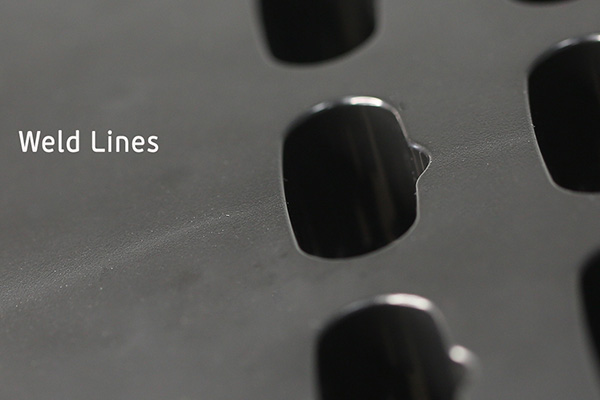
How To Design For Weld Lines?
Weld lines can be partially hidden by incorporating them into the product design. That is, masking their presence by integrating fins, lines, raised/recessed lettering or heavy textures into the surface where a weld line would be formed. It’s possible to apply some finishing techniques after the part’s been molded to hide the weld line.
For example, roughing up the surface by sand blasting or painting can both help hide the weld line. Depending on the design, plastic resin and plastic color, some combination of all of the above may be needed to achieve a satisfying result. Also bear in mind that the weld line represents an area of comparative weakness, so if a part fails under mechanical stress it will most often fail at this location. A careful engineer may want to therefore add reinforcements at these critical areas.
A good manufacturing partner will always try to work with you to discuss practical molding issues in advance and will suggest corrective actions before the tool is built. It’s important for you to know the physical limits to what can be done and how to allow for them in your design.
If you’d like to get started on your next project, send our customer service engineers your product design for a free quotation.
Tagged: