Lean manufacturing helps identify and eliminate the seven types of waste typically found in manufacturing environments: transport, inventory, motion, waiting, overproduction, over-processing and defects. To combat this, manufacturers are increasingly adopting lean systems to become more efficient, more reliable and to provide higher quality. How to identify if your manufacturing partner is lean? Look for these six key ingredients.
Are They Organized?
The heart of the lean system is embodied in the Japanese concept of kaizen, or continuous improvement. These six principles are Set, Shine, Sort, Standardize, Sustain and Safety.
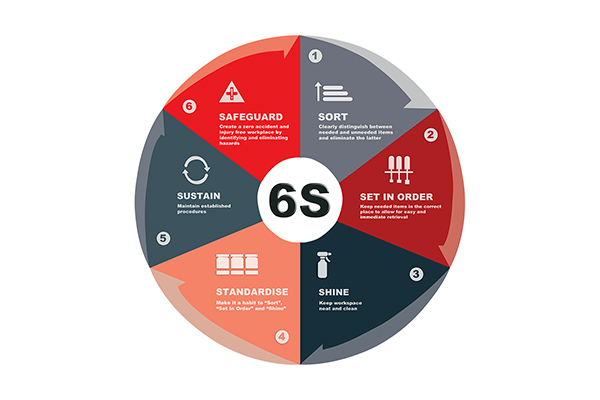
Smart manufacturers use a system everyday to remind themselves of the importance of setting good organizational habits and maintaining them. Over time, this encourages the entire workforce to always look for a better way to do things. And it lays the foundation for the most critical, yet often overlooked, aspect in any lean system: changing the culture.
Do They Support a Lean Culture?
No program, plan or methodology is going to work unless everyone makes it a habit. That takes time, discipline and leadership throughout the organization. Remember, lean doesn’t happen overnight. It’s a process that evolves and never really ends.
Have They Mapped Their Value Chain?
Value is any process that improves a product and for which the customer is willing to pay. Lean manufacturers will reduce non value-added steps to the barest minimum. To visualize this more clearly, they use value stream mapping to graphically represent how a facility is arranged.
Value stream maps typically use standard symbols that indicate common tasks such as movement, storage, processing, measurement, shipment, etc.
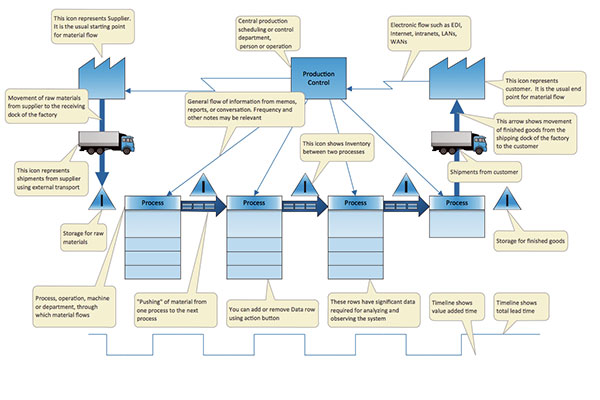
A good map shows where an organization is now, and points to where it wants to go. Value stream mapping clearly shows areas of waste, for example maybe a place where parts are stored for too long awaiting further processing.
Value stream mapping can also be used with other visualization tools to virtually rearrange the workspace to test out alternate setups in order to optimize resources. Smart decision makers do this before making any investments in new processes or equipment.
Is Their Data Reliable?
Intelligent manufacturing relies on making strategic decisions using accurate data. Employing connected technologies like RFID tags or NFC chips can help a factory track physical inventory automatically and reliably, eliminating the need for tedious manual counting and sorting.
This real-time data can then be fed into sophisticated Manufacturing Executions Systems (MES) software, allowing managers greater awareness than ever before of the actual conditions, at every moment, on the factory floor. But this knowledge is useless until it can be acted upon, and that requires connection.
Are They Connected?
Connected systems form the backbone of Direct Equipment Access. All critical machinery and processes in a smart factory can be tied together electronically, so that operators can not only see what’s happening on the floor but can interact and optimize with the touch of a button.
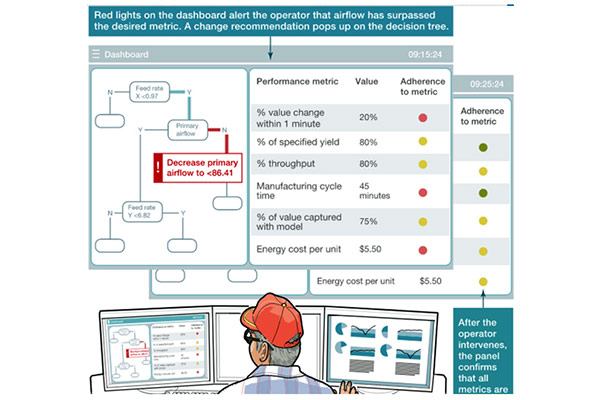
In a connected factory where every production cell is talking to the whole, some decisions can be fully automated.These might include ordering material when stock runs low, switching to a new CNC program after the previous one is finished, or contacting a shipping company to pick up an order waiting in a finished goods warehouse.
Connected systems can move more quickly than people if they’re set up properly, saving time and money. Systems work properly when they’re no longer merely reactive but preventive. And that happens when they get smart.
Are They Smart?
Lean and intelligent manufacturing places a premium on constant improvement. This happens when operational parameters are fed back into the system to enable artificial intelligence and machine learning. The smarter the system is, the better it will predict when a machine needs downtime for maintenance, alert you to replace a worn cutter head before it goes dull, even monitor the weather to control temperature and humidity in the factory before it has a chance to impact product quality. Preventive, not reactive.
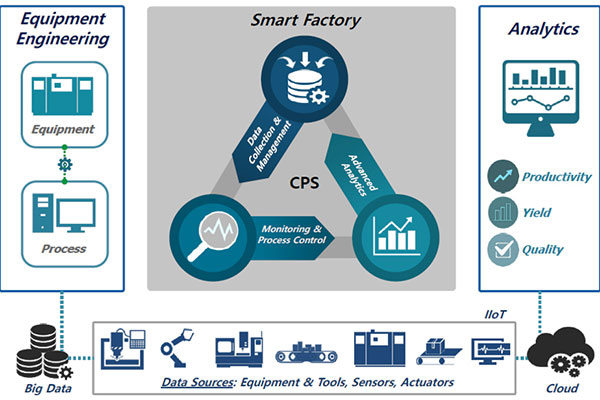
Moving to lean and intelligent manufacturing takes time, diligence, and the cooperation of the entire workforce. This is the direction that all advanced industries are taking, and it’s also where Star Rapid is placing all of its resources to better serve your needs for the best rapid prototyping and low volume manufacturing services. Find out more when you upload your CAD files for a free quotation.