Surface roughness is often described by the term Ra but many of our clients are unsure about what this means, how it’s measured and why it’s important to their product’s designs. So here we’d like to remove any mystery so you’re better able to specify exactly the type of surface roughness you want and need for your next project.
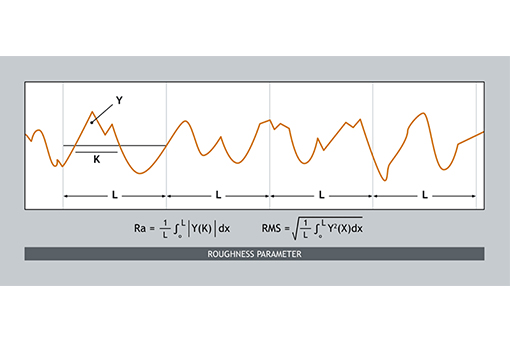
What Is The Ra Value?
Imagine that you’re looking at the profile of a part. If you take a sample length and measure the high and low spots along that length, Ra is just the average height above and below the reference line, or mean. The bigger the Ra number, the more rough the surface. If the Ra value was 0, the graph would show a perfect horizontal line, meaning the surface was absolutely flat. Not possible in this universe.
There are other systems of measurement which are similar but not exactly the same. This can potentially lead to confusion and error, so it’s important to know what system you may be referencing and that it’s the same as that of the factory making your parts. When in doubt, ask. There are conversion charts available to easily translate from one system to another if necessary.
Why Should You Care About The Ra Value?
This is the industry standard for specifying to a manufacturer what the roughness should be – and should not be – on your part. This is used for prototypes, machined parts, and for tooling. It effects the part’s functionality and performance as well as its appearance. For example, many bearing surfaces require a uniform pattern of roughness which helps to retain a film of lubrication. Too smooth or too rough and the bearing would fail. Also, surface roughness should not be confused with surface finish, although the two are related. Therefore understanding the purpose of Ra is essential to getting the part that you want, but it’s not the whole story.
What's The Rest of The Story?
Remember, Ra only tells us the average deviation from the mean, or the highest highs and the lowest lows, averaged out over the sample length. But there are many ways to achieve this same number using different manufacturing techniques, and each of those techniques will impart a unique pattern on the surface. Thus, manufacturers routinely use surface roughness gauges to measure and compare how different machining methods will produce very different looking textures.
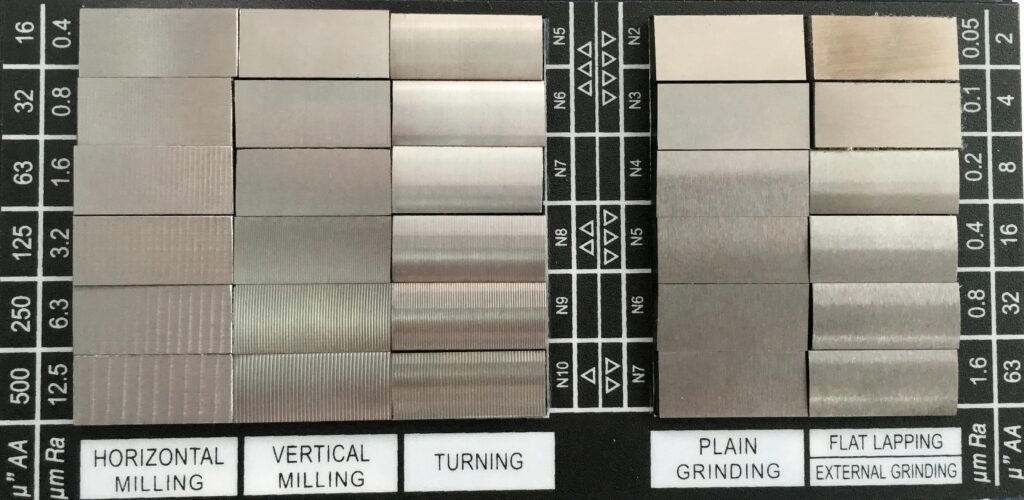
The patterns on the surface of these gauges differ essentially in the spacing of the grooves, or the waves, which is one of the basic determiners of surface texture. The waves on the left are low-frequency, increasing in frequency from left to right. Again, the average height, or Ra value, may be the same but the look is quite different. Various CNC and manual machining processes all impart characteristic patterns on the workpiece, so you should be familiar with them.
That’s why we strongly recommend that, whenever possible, you reference either a gauge such as one of these or, better yet, submit a sample for comparison. Textures are by their very nature very complex and difficult to define. A sample is the best way to ensure customer satisfaction.
How is Surface Texture Measured?
There are many possible methods for measuring surface texture, depending on the size of the part feature, part geometry and material type.
One of the most common ways is with a probe or stylus, called a surfometer, that is slowly drawn across the face of a part or part feature. Every deviation from a nominal or reference line is recorded on a graph for later interpretation.
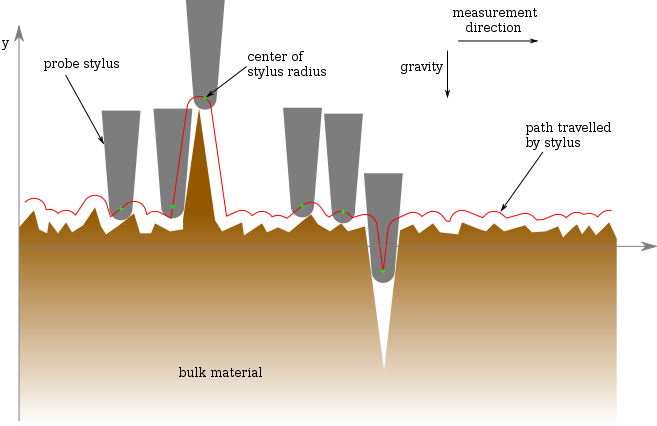
The Ra value can then be calculated easily by such a reading. In addition, it may be desirable to look at the total surface area from a wider view to see if there are any other surface defects, and one of the ways to do this is with optical photometry.
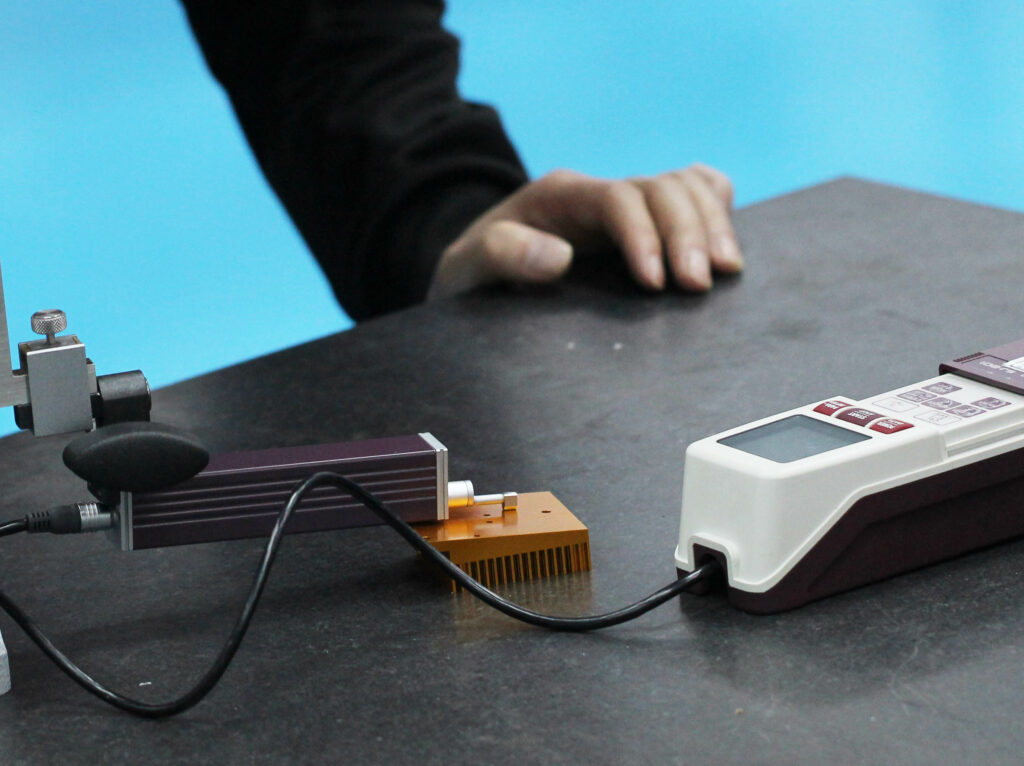
One key use of optical photometry is with the identification of asperities. These might be voids, scratches or inclusions of some contaminant in the raw material. Many mathematically-derived models tend to discount these anomalies as irrelevant, but for increasingly critical applications in aerospace, defense and scientific instruments the presence of any defect could be catastrophic. It therefore requires a combination of human and machine intelligence to make the ultimate decision about surface qualification.
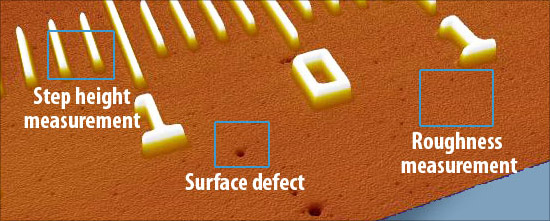
Why Should You Care?
There’s no area of manufacturing that causes more frustration and misunderstanding between client and factory than that of surface texture. It can be difficult to describe or specify, so in all cases it’s best to discuss this aspect of your design in detail before commencing with a quotation or production. And remember that there are many different ways to impart a finish on a surface, which create different mechanical and aesthetic affects. When you contact us for a free quotation we can advise you about the methods we use and how you can best achieve the surface roughness you want.