All metal prototyping and CNC machined components will leave behind a pattern of characteristic scratches on the workpiece. These are caused by the type of cutting tool, how sharp it is and the material it’s made from. In some cases these scratches can be ignored but usually to make a truly “finished” part one or more secondary processes need to be applied. Below are brief descriptions of the 7 main finishing processes to remove these scratches to make your final piece look perfect.
1. Sanding
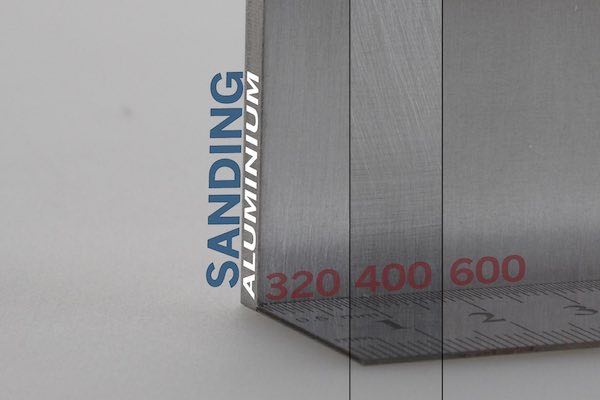
Sanding is simply a method for rubbing abrasive particles against the surface of a workpiece to create a random, non-linear surface texture. Different abrasive media are used, glued onto a backing paper or plate. The size of the cutting grains is referred to as “grit”: the higher the grit number, the smaller and finer the particles are and hence the finer the surface finish they are able to achieve.
Very coarse grits can remove a lot of material quickly, while finer grits are able to achieve a mirror polish. Water or some other lubricant is often used to flush material away and expose a fresh cutting surface. Sanding is especially useful for contoured or curved surfaces, but it’s not ideal for getting into very tight corners or pockets.
2. Ultrasonic Polishing
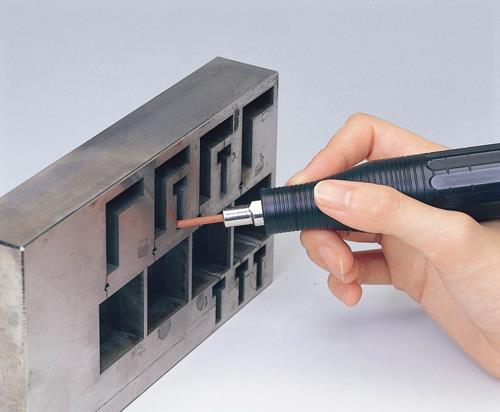
When making a tool for plastic injection molding or pressure die casting, it’s often necessary to give the inner cavity a fine polish to make a beautiful finished part. But tool steels are heat-treated and very hard, so polishing them is difficult. It’s also not easy to reach into holes, pockets, and other complex shapes.
Ultrasonic polishing is used in these cases. A soft, fine-tipped tool is mounted onto an ultrasonic spindle that vibrates at 30KHz. In combination with an abrasive slurry medium, the tool tip does not actually touch the work surface but it induces a pressure wave that safely works away at the surface to create a fine polish. This technique works even on hardened steels and there’s little chance of damaging the workpiece.
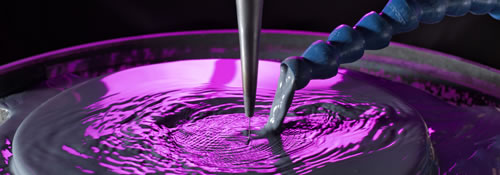
3. Rumbling And Tumbling
Similar to sanding, both rumbling and tumbling use an abrasive media but in this case the sanding particles are “loose” and not fixed onto any backing paper. Depending on the workpiece and the type of finish desired, many different types of media can be used, including garnet, walnut shells, stones, or coarse sand.
In tumbling, components are placed into a box or tub along with the abrasive particles, which is then rotated to mix everything together randomly. This is often used for “deburring”, or to remove the sharp metal points left on a part’s edge after it’s been machined.
Rumbling is much the same but the parts and abrasive are in a trough that is then vibrated to increase the cutting action.
4. Magnetic Polishing
Deep holes, pockets, or large interior chambers sometimes need to be highly polished in order to make a smooth surface with a low frictional resistance to air or liquid. But these areas can be difficult or impossible to reach by hand, so a different method is needed.
Like with tumbling, metal parts can be put into a box or chamber that’s filled with magnetized particles. Using a focused magnetic field, these particles can then be directed to abrade away against the interior surface to achieve a fine polish.
5. Sandblasting
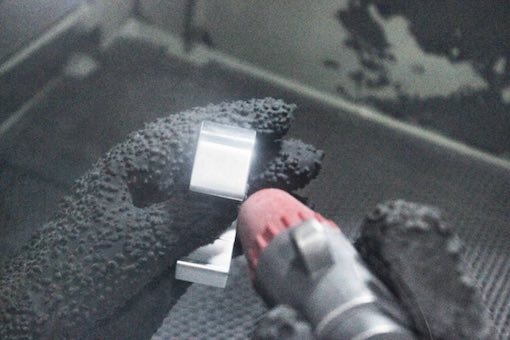
This is the process of treating the surface of a part by blasting it with an abrasive media under high pressure. The type of media used again will determine the quality of the resulting finish. Sandblasting, or blasting with a combination of air and water, can cover a large surface area quickly. It can also improve some of the mechanical properties of metal, by increasing fatigue strength and improving corrosion resistance through shot-peening.
6. Lapping
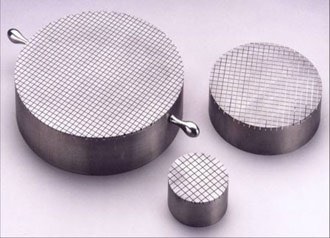
Lapping is a precision technique for achieving the highest degree of surface refinement and flatness. It involves a skilled craftsperson who uses a soft iron tool together with a mild abrasive slurry to slowly work the surface with random, light and non-linear motions by hand. This fills microscopic surface voids and flattens high spots.
Machines can also be used for this process but it requires a very slow speed to avoid heating the workpiece.
7. Filing
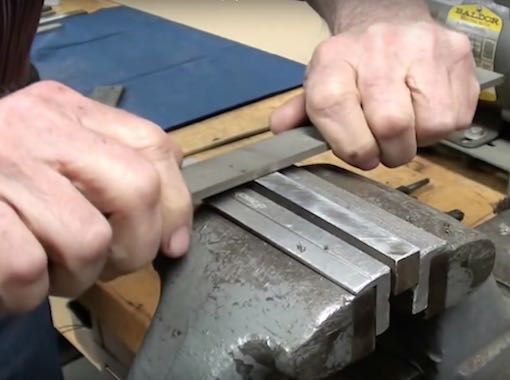
A file is a piece of very hard steel that has a series of parallel grooves cut into it, which leave behind rows of sharp cutting teeth. Files are typically used by hand and, depending on how coarse the teeth are, can aggressively remove material and shape metal quickly. The surface finish is somewhat rough and imprecise and often needs additional sanding or polishing for good results. But files are still versatile, easy to use and can produce fine results in skilled hands.
Which Finishing Process Is Right For You?
At Star we use all of these finishing methods and more to produce any kind of surface you want on your metal prototypes or CNC machined parts. Contact us today for a free quote and project review and we will show you how we can put these methods to work on your next project.
Want to learn more about surface texture?
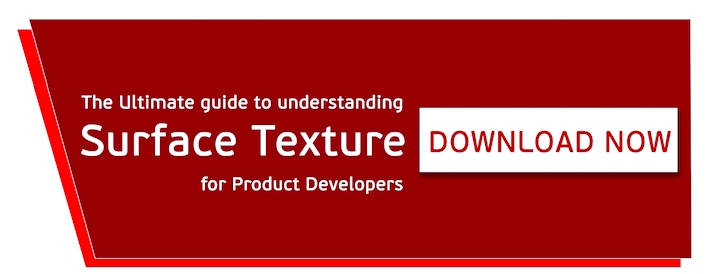
Tagged: