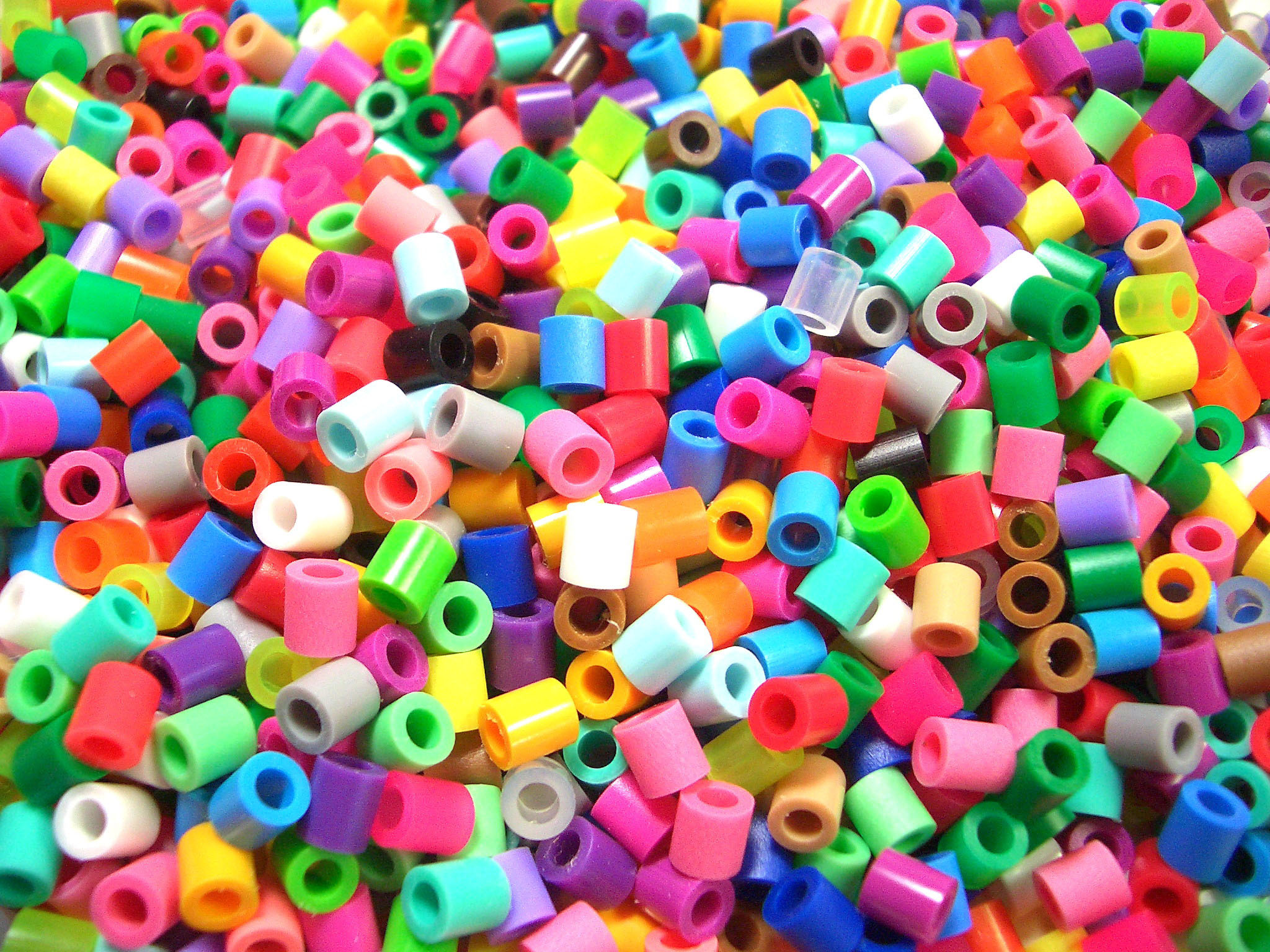
A truly revolutionary new class of material successfully combines the best attributes of thermoforming and thermosetting plastic. This could change the way we make rubber ducks, jumbo planes and everything in between. It might also greatly effect and improve our impact on the environment.
What Are The Most Common Plastics?
Polymers, generically called plastic, used in injection molding come in two distinct flavors. One type is thermoforming, which is a class of material that is heated to a liquid state, molded, and then solidifies when cool. The other is thermosetting, usually a resin and a catalyst which undergo an irreversible chemical reaction during the molding process. More about both kinds of plastics and their uses can be found here.
Pro’s And Con’s Of Thermoforming Plastics
Thermoforming plastics come in the widest variety, and by far most plastic objects commonly found in our world are made of this type. They can be recycled but the relatively weak bonds mean such plastic is easily deformed and can break down under continuous loads, and they are prone to destruction by solvents and acids.
Pro’s And con’s Of Thermoset Plastics
Thermosets are more expensive and there are fewer choices than for thermoforming. They cannot be recycled and must be formed in situ in the mold since they cannot be modified once they set up. They are mechanically strong, durable and insoluble so this type of plastic is the most common choice for demanding engineering applications, but they cannot easily be welded or otherwise repaired if damaged.
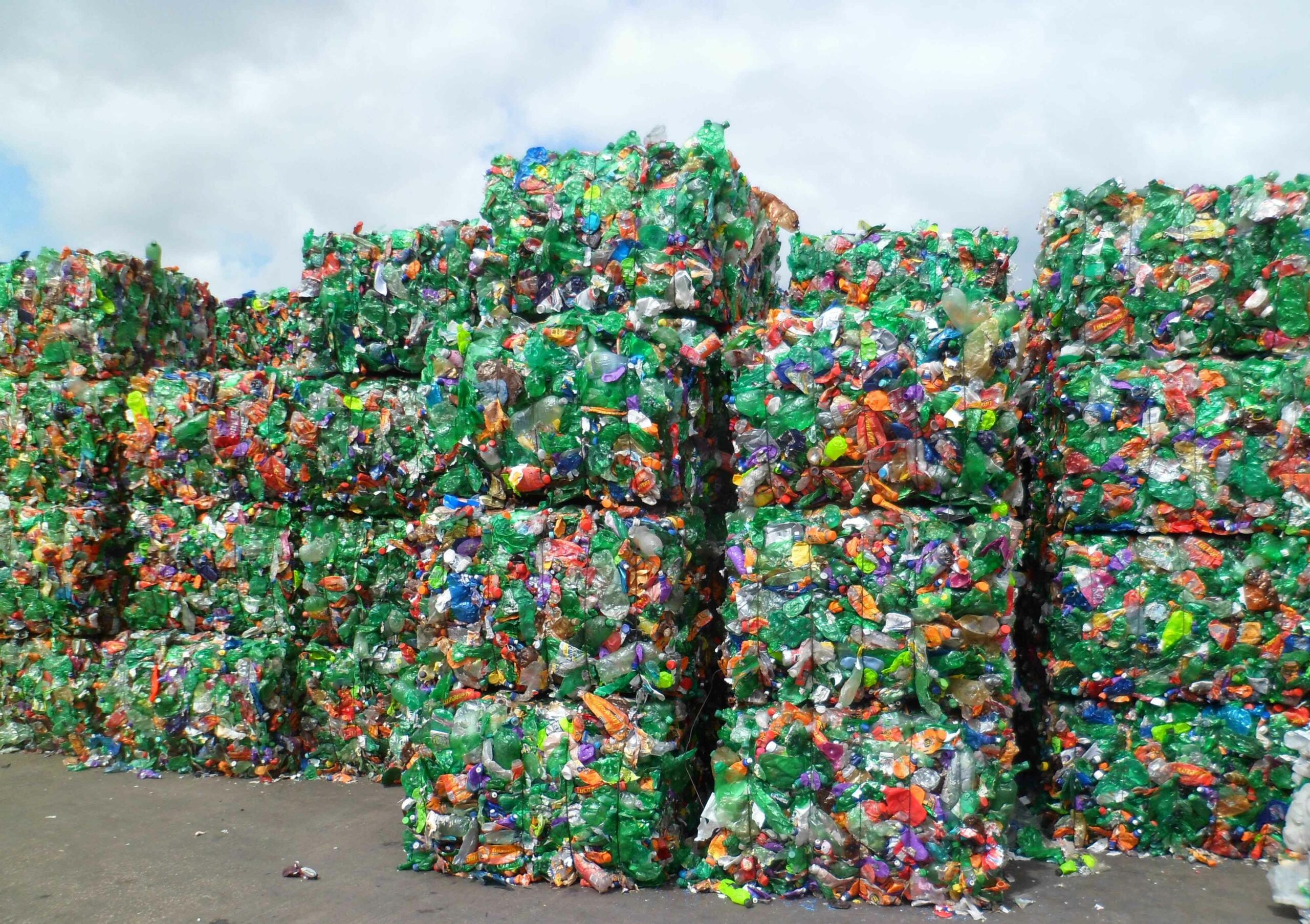
The Big Issue With Plastic: Waste
About 300 million tons of plastic is produced each year, a number that is growing larger all the time. Of that, less than 10% is recycled. That means the rest gets dumped in a landfill or washed out to sea, more than 8 million tons per year in the later case.
There are many reasons for this degree of wastefulness, but one major cause is simply that the plastic item is broken in some fashion and is no longer fit for its purpose – a leaking plastic bucket, a broken plastic chair leg. Both thermosets and thermoforming plastic are hard to repair and are prone to UV degradation so they crack. Even recyclable plastic requires controlled conditions and can produce noxious fumes so it’s not done by individual consumers, who also aren’t prepared to deal with remolding a broken object.
What’s The Alternative To Plastic?
What if there was an alternate material that was durable, non-porous, insoluble, non-toxic, infinitely recyclable, plentiful and cheap? There is, and it’s called glass. Glass, or “inorganic silica”, has some wonderful attributes, but as we all know it can be heavy and it’s brittle. Glass, by the way, doesn’t form a solid crystalline structure but is rather more like a very, very slow-flowing liquid when at room temperature.
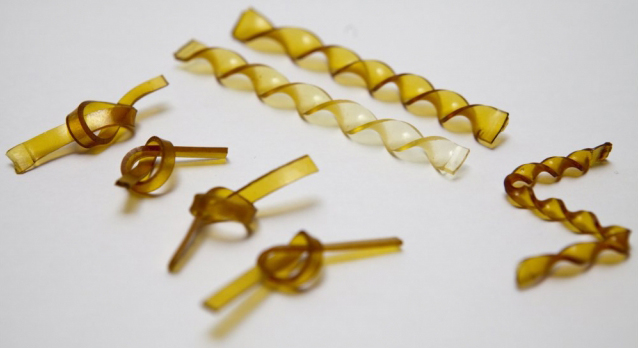
Vitrimers
Now Ludwik Leibler and his team at the Paris laboratory CNRS have managed to create a new class of materials that combines the best of both thermosetting and thermoforming plastics using a glass-like transitional form called vitrimers.
Like with other plastic types, the exact composition can be modified to produce a rigid metal-like structure or a softer and more flexible rubber which is stable at room temperature. But under the influence of heat it can be re-molded, repaired and reformed with no loss of strength. The secret lies in the chemical bonds, which can be rearranged without decreasing the total number of cross links in three dimensions, thereby preserving strength.
Imagine everyday objects that no longer need to be tossed out, but can be easily repaired in the field with something as simple as a heat gun or cigarette lighter. Car panels made with lightweight vitrimers that can be repaired easily to deal with those little dents and scratches we all know so well. Coupled with 3D printing, the number and type of applications is incalculable.
Vitrimers are still in the testing stage, but that they exist at all is something of a miracle since it was previously thought impossible to combine the distinct qualities of thermoforming and thermosetting plastic. As you can tell, we love to keep up with the fascinating progress being made in materials science and when new – and better – raw materials come along we will no doubt make use of them. Better products that are better for the Earth – sounds good to us. Check back with us soon for more reports on the cutting edge of manufacturing and engineering.