- Case Studies
- Claris Case Study: Prototyping a Medical Rehabilitation Aid
Claris Case Study: Prototyping a Medical Rehabilitation Aid
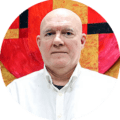
- Star Rapid
- 4 min
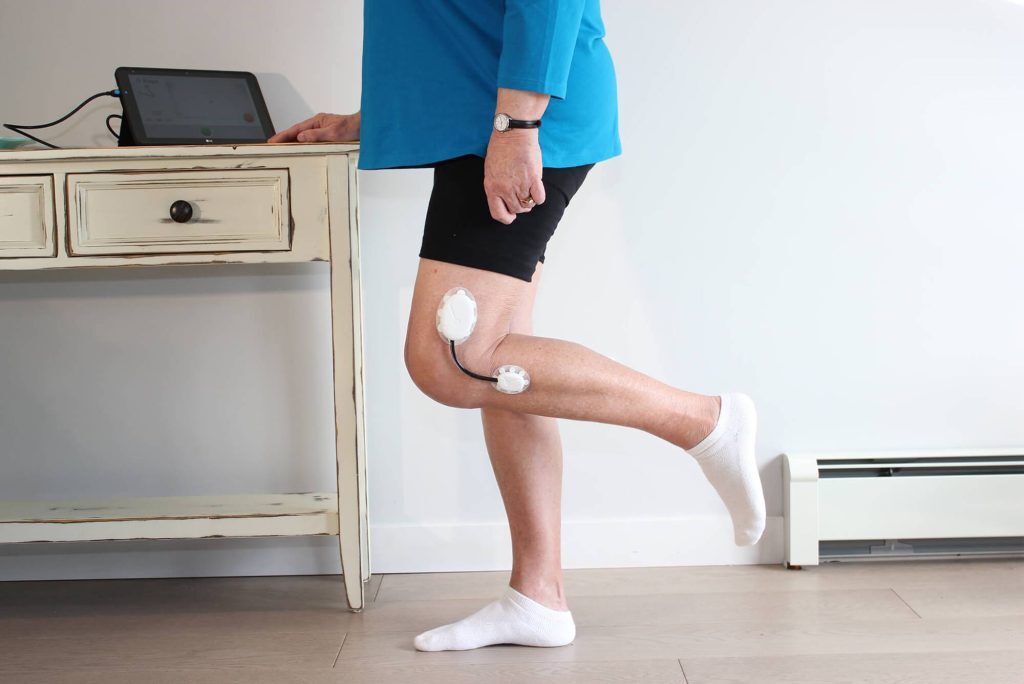
- Case Studies
- Claris Case Study
Claris Case Study: Prototyping a Medical Rehabilitation Aid
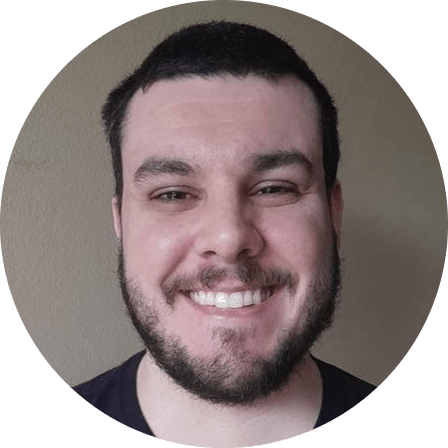
- Star Rapid
- 4 min
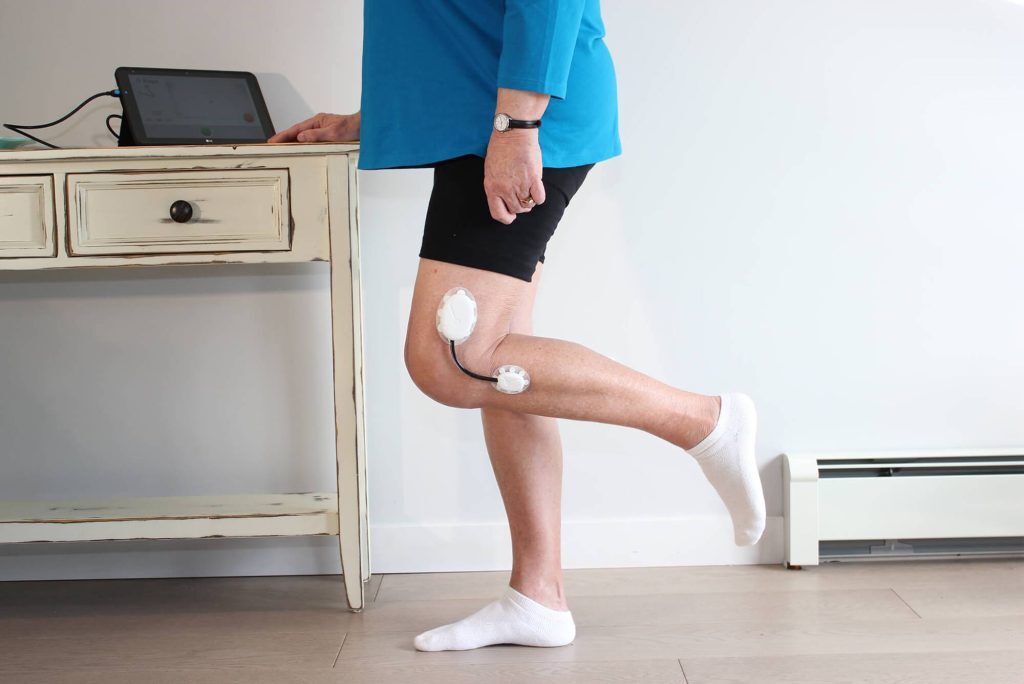
ABOUT
Claris Healthcare: Software Company for Remote Care Solutions
StarFish Medical: Provider of Medical Device Design and Development Services
Industry
Medical
Components
Plastic Injection Molding Tools for Pads and Main Sensor Housing
Services
Table of Contents
ABOUT
Claris Healthcare: Software Company for Remote Care Solutions
StarFish Medical: Provider of Medical Device Design and Development Services
Industry
Medical
Components
Plastic Injection Molding Tools for Pads and Main Sensor Housing
Services
Prototyping a Medical Rehabilitation Aid
Recovering from knee replacement surgery is challenging and requires constant monitoring by healthcare professionals and a rigorous, sustained commitment to physical therapy to regain mobility and strength in the knee joint.
Claris Reflex is a device that facilitates this process by monitoring progress and sharing data with healthcare professionals. We are honored to have played a crucial role in this innovative launch, along with Claris Healthcare and StarFish Medical, by improving the design for manufacturing and creating the tools for plastic injection molding.
The Challenge: Optimizing Design for Manufacturing
- Calculating draft angles to ensure parts are easily released from the mold
- The shrinkage rate of the plastic resins used
- The placement of runners, gate marks, and parting lines
- Wall thickness to ensure proper resin flow during injection
We identified potential improvements, discussed and approved them with the product development team, and only then started making the molds and parts.
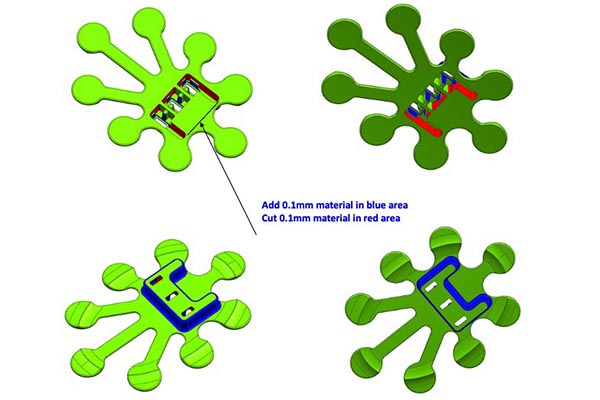
Our Approach: Tooling for the Claris Reflex
We started by carefully reviewing the CAD files provided by StarFish Medical — because there is no one-size-fits-all solution. While there are best practices for optimizing designs for plastic injection molding, each part must be analyzed in detail to improve the project’s results.
During the review, we made some modification suggestions in certain areas. In the image below, you can see where we recommended reducing material in some areas and increasing it in others to achieve better performance during injection molding.
Before proceeding to part creation, we worked on identifying the raw materials used in tooling and injection — analyzing each batch of incoming material to confirm its composition. This step ensures that all materials behave as expected during production.
Next, we made mold tools. This is a custom solution that must consider many variables, such as tooling material, production volume, tolerance and precision required, mold tool durability, tool changing time, and more.
Once completed, the mold tools were trialed and analyzed for these aspects of performance:
- Mold appearance and any irregularities that could affect the surface of the parts
- Filling and flow of the molten resin
- Part ejection
- Vent and cooling systems
- Performance during injection
- Appearance, texture, dimensions, and other parameters of the injected parts
Only after confirmation are the mold tools considered ready for production.
The Result: Low-Cost Production with a Rapid Turnaround
Star Rapid’s approach directly helped reduce costs and lead time during tooling. Most importantly, this was done without rushing through quality control stages.
Our international team is experienced in tooling for new products across many industries, including the medical field. This expertise enables us to collaborate effectively on each new project, ensuring that production is as efficient as possible.
This partnership brought to the market a Class I medical device that is easy and comfortable to wear and provides a continuous stream of useful information to improve patient recovery.
According to Geof Auchinleck, CEO of Claris Healthcare, Claris Reflex was a pioneer in the at-home treatment of total knee replacement surgery. And we are thrilled to collaborate on breakthrough inventions like this! Watch the system in action.
A Trusted Partner in Medical Device Manufacturing
Star Rapid is the chosen partner for medical device designers from around the world who need fast turnarounds with the most professional service. We’ve developed a full range of services to create high-quality tools and parts faster and at lower costs, from fabrication to surface finishing.
Your project will be handled by a team of engineers experienced in optimizing and making high-quality medical handheld devices, wearables, telemedicine equipment, rehabilitation devices, diagnostic and clinical research tools, and more.
Upload your CAD files today to receive a personalized quote and start working with our expert team.