Conservify Develops Award-Winning FieldKit with Star Rapid
Services: CNC machining Services, Electrical Discharge Machining, Chemical Photoetching, Plastic Injection Molding Services, Light Assembly
Material: HRA222F PC + ASA Plastic Resin, Brass Inserts, Stainless Steel, Silicone Rubber
Quantity: 1000 units
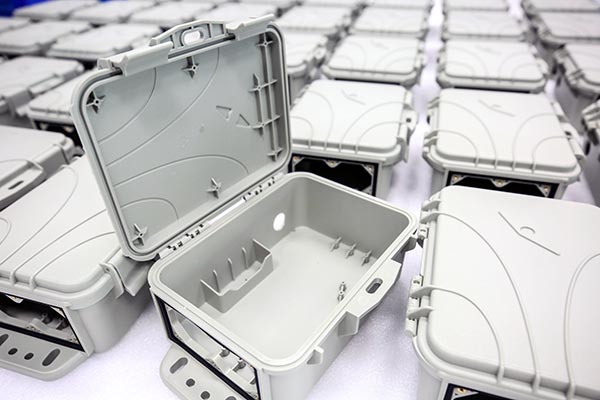
Conservation And Protection for Ecosystems
Conservify is dedicated to making environmental research and conservation available to small communities where it’s needed most. They do this by combining open-source software and digital apps with easily configured hardware to empower citizens everywhere to monitor and protect their natural resources.
What is the FieldKit?
Conservify’s latest project is the FieldKit, a solar-powered case that supports many kinds of devices needed for conservation work in remote locations.
Some examples of connected electronics are cameras and microphones, batteries, pressure and temperature sensors, microcontrollers, data storage cards, WiFi routers and many more. The FieldKit is designed to be flexible and adaptable while also being rugged enough to protect vital electronics in any environment.
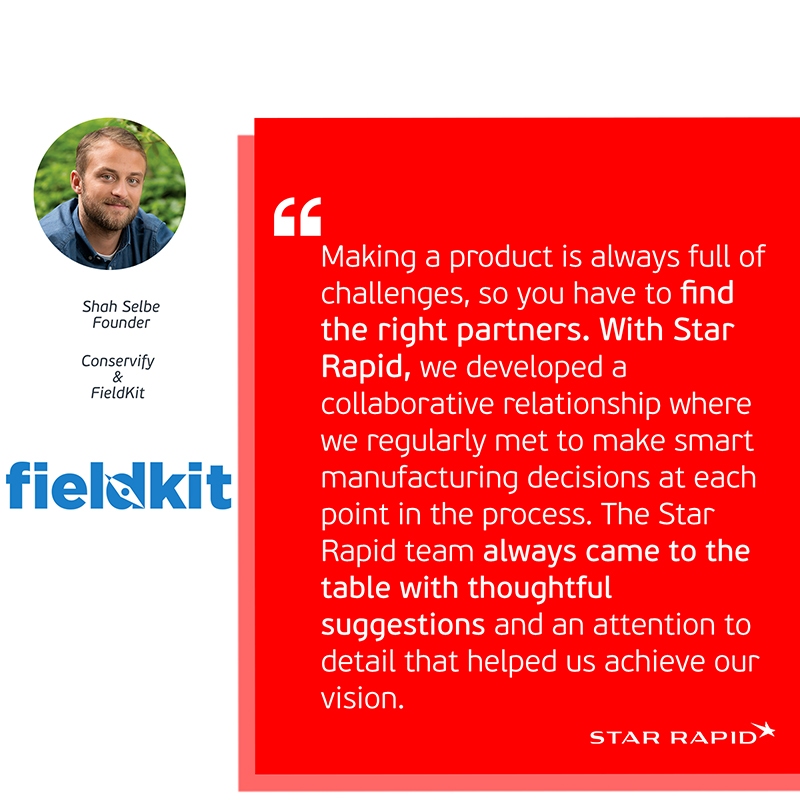
Conservation And Protection for Ecosystems
Conservify is dedicated to making environmental research and conservation available to small communities where it’s needed most. They do this by combining open-source software and digital apps with easily configured hardware to empower citizens everywhere to monitor and protect their natural resources.
What is the FieldKit?
Conservify’s latest project is the FieldKit, a solar-powered case that supports many kinds of devices needed for conservation work in remote locations.
Some examples of connected electronics are cameras and microphones, batteries, pressure and temperature sensors, microcontrollers, data storage cards, WiFi routers and many more. The FieldKit is designed to be flexible and adaptable while also being rugged enough to protect vital electronics in any environment.
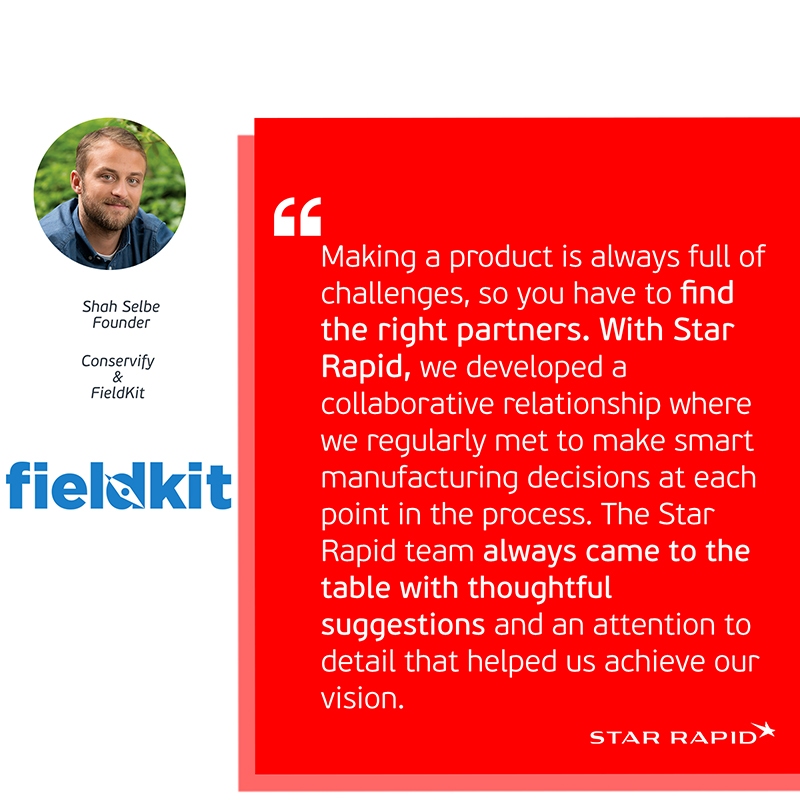
Conservify Teams up with Star Rapid
The engineering team at Star Rapid collaborated closely with Conservify at every step of the manufacturing journey. The most important factor is understanding the needs of the client through clear communication and finding solutions together.
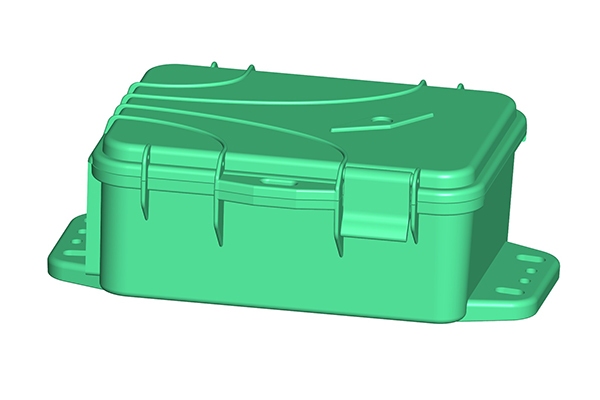
We want to share some of the highlights of this project, which was especially satisfying to work on because it represents such a worthy cause. We hope these manufacturing insights can also help product developers like you to optimize your designs to achieve superior results.
Plastic Resin HRA222 F PC + ASA
Conservify also asked that we recycle the plastic sprues during molding. Sprues are the remnants of the mold’s gate and runner system and they usually represent waste material. Recycling them instead helps to not only save money but, more importantly, conserve resources. This is of course very much in line with their goal of environmental protection.
FieldKit Design for Manufacturing Review
Our tooling engineers worked closely with Conservify to examine all of the details of their CAD drawings while always being mindful of the product’s final application. This careful evaluation often reveals areas where a design can be modified, even slightly, to enhance both its appearance and fitness for purpose. We are happy to share these insights in the hope that they can also help you.
Draft Angles
The case, lid and clasps all have a molded-in textured surface. In order to remove heavily textured parts from plastic injection molds it’s necessary to add draft angles, and the heavier the texture the more draft that is needed. Without draft, the parts will either drag against the tool wall and be damaged or they will be impossible to remove altogether. In this case we recommended at least 2 deg.
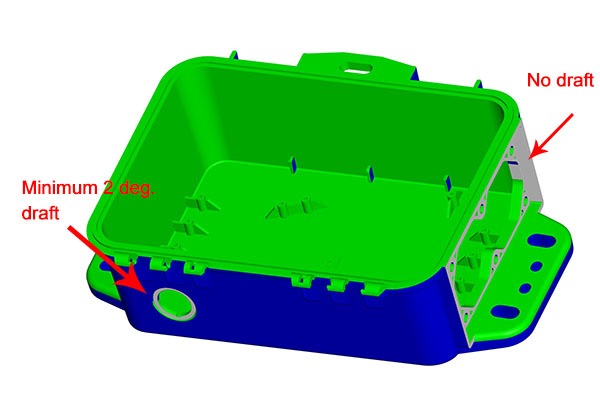
Notice that one side of the case has an access port, and this is oriented at right angles to the bottom of the base. This feature and many others in this design must therefore be made with sliders.
Sliders
A slider is one part or section of a plastic injection mold tool that can be opened and closed in a direction different from that of the cavity / core. Sliders are used to make right angle features or undercuts that can’t be formed conventionally. In the case of the port for example, the slider is held in the closed position during injection but is then withdrawn at 90 degrees. This makes a right angle without a draft.
We used a black marker to indicate areas that still hadn’t been touched up yet.
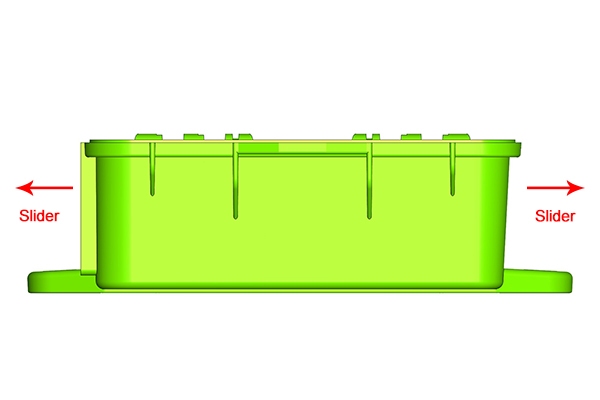
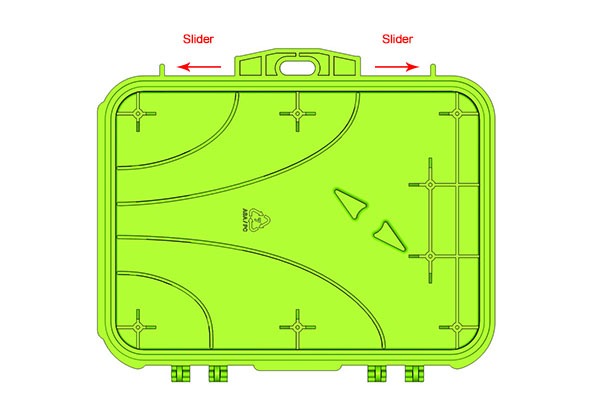
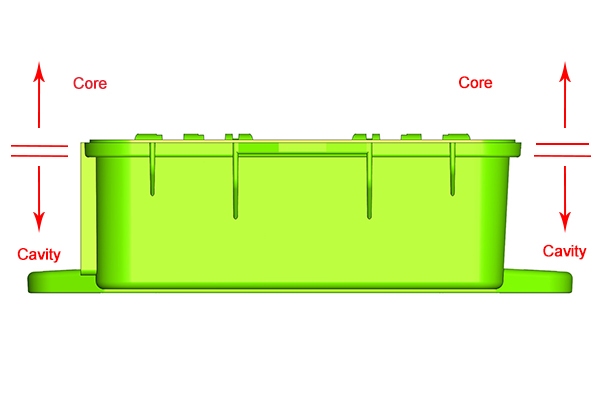
The purpose of sliders is to form undercuts and other features that would otherwise interfere with the mold opening. Several sliders were needed to make all the features of this part successfully. The use of sliders is often unavoidable but they do add cost and complexity to the tools and dies.
Gate Witness Marks
The gate is where the nozzle of the injection molding machine forces liquid resin into the empty cavity of the mold. Gates come in many varieties, but ultimately their purpose is to fill the mold cavity as quickly and efficiently as possible before the resin has time to solidify and the gate “shuts off”.
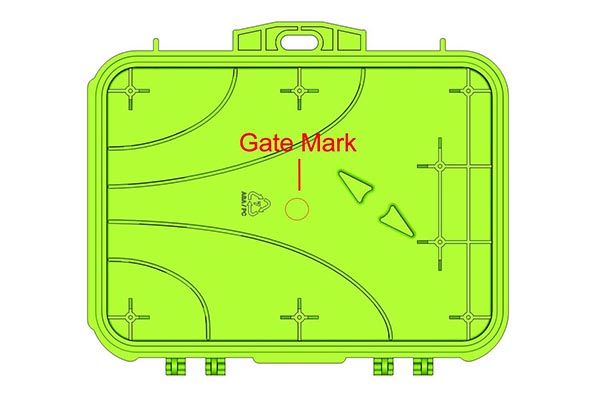
Initially the customer wanted to use a side gate for injecting the case cover. But from this location it proved difficult to fill all the features before gate shut-off. Instead we used centrally-located pinpoint gate which left behind a characteristic witness mark in the center of the part.
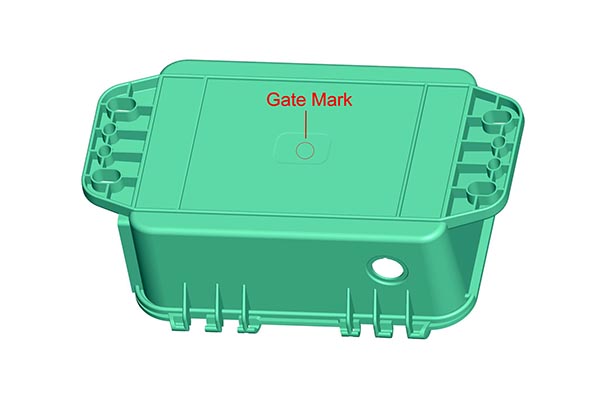
Witness marks are often unavoidable but they can be diguised by heavy texturing or, as with the base, they can be put in a relatively unimportant location where they won’t affect the appearance or performance of the finished part.
Hinge Detail of the FieldKit
The most challenging part of this project was perfecting the design of the hinges that join the lid to the base.
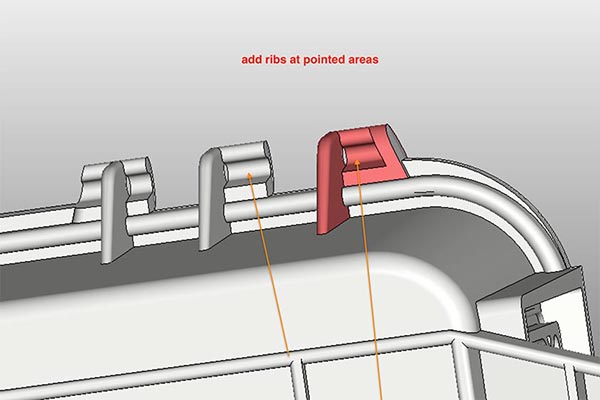
In the initial design, the pass-through for the hinge pin was a smooth bore. We felt this would not hold the pin securely, which turned out to be true during early testing. We added ridges to the inside diameter of the bores and this increased the grip enough to hold the hinge pin securely.
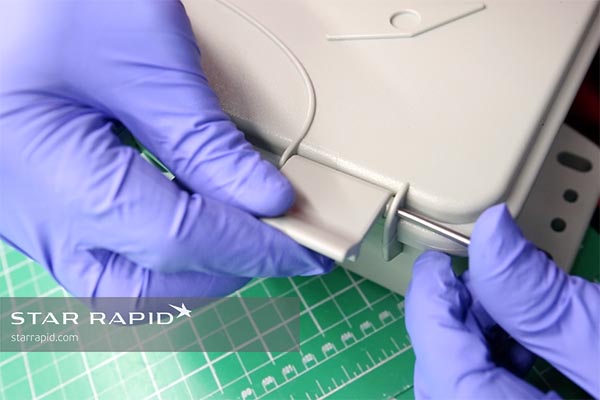
In the initial design, the pass-through for the hinge pin was a smooth bore. We felt this would not hold the pin securely, which turned out to be true during early testing. We added ridges to the inside diameter of the bores and this increased the grip enough to hold the hinge pin securely.
Machining the Plastic Injection Mold Tools for the FieldKit
We used sink EDM to make some of the deeper features in the mold tools. This is the only practical way to make deep holes, pockets and other recessed features in tool steel. We used copper electrodes immersed in a conductive dielectric fluid such as water or oil which carries the electric charge.
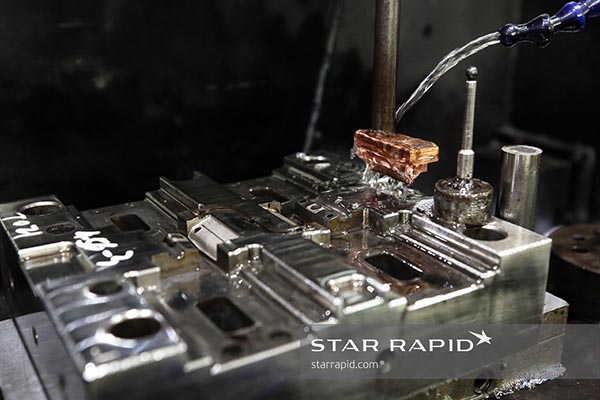
Adding Texture to the Mold Tools
Mold textures at one time were produced with a “spark finish”, created with a single large EDM electrode to etch the tool wall. However, a spark finish is hard to control uniformly.
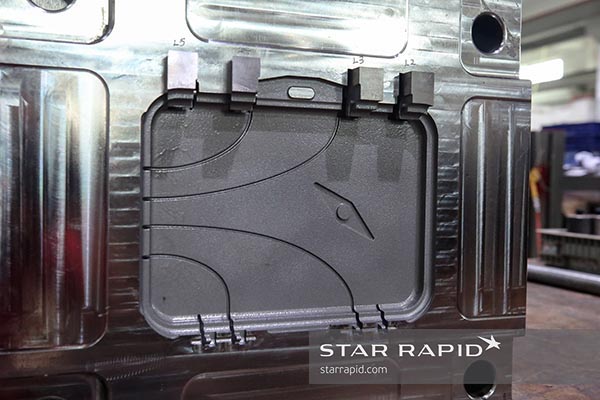
Now it’s common to use chemical etching to produce a uniform patterned finish on tool steel. There are thousands of stock patterns available for duplicating the textures of stone, wood, leather or other geometrical designs.
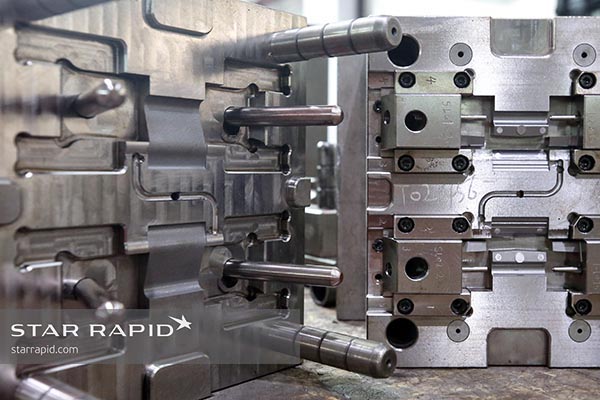
Now it’s common to use chemical etching to produce a uniform patterned finish on tool steel. There are thousands of stock patterns available for duplicating the textures of stone, wood, leather or other geometrical designs.
Compression Molding for the FieldKit
We also made compression molds to form the silicone sealing gaskets. These seals help to keep dirt and water out of the case.
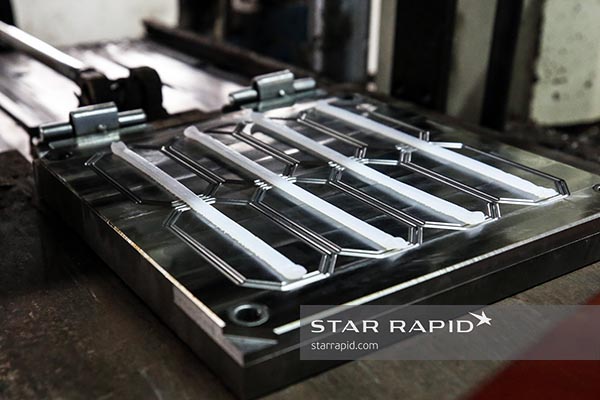
Compression differs from plastic injection molding in several ways. First, the molds themselves are relatively simple clamshells. Secondly, the raw material is introduced into the pre-heated mold already in a semi-liquid state, but it’s uncured. And the raw materials are thermosets, meaning they undergo a permanent change of state and cannot be reformed. After clamping, the heat and pressure force the material to fill the voids in the mold. The process is fast and wastes little material.
Ready for the Most Challenging Environments
We also made compression molds to form the silicone sealing gaskets. These seals help to keep dirt and water out of the case. We hope you enjoyed this case study overview and perhaps have gained some insights that can help you on your next project. We look forward to following the progress of the FieldKit as individuals and groups make use of it to collect valuable data. Do you have a great idea you also want to make into reality? We’re standing by to offer a free quotation and project review when you upload your CAD files today.
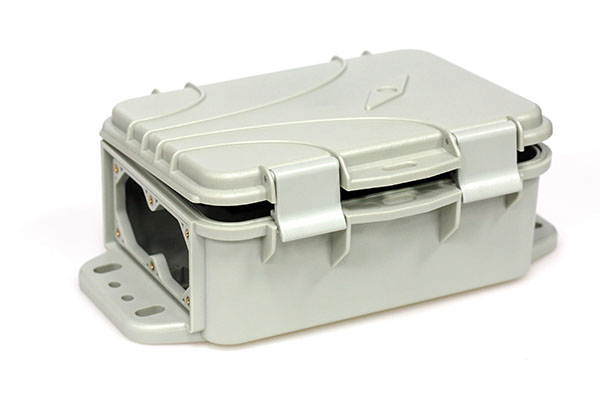