- Case Studies
- Technology Meets Fashion: 3D Printing Custom Jewelry Designs
Technology Meets Fashion: 3D Printing Custom Jewelry Designs
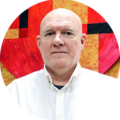
- Star Rapid
- 7 min
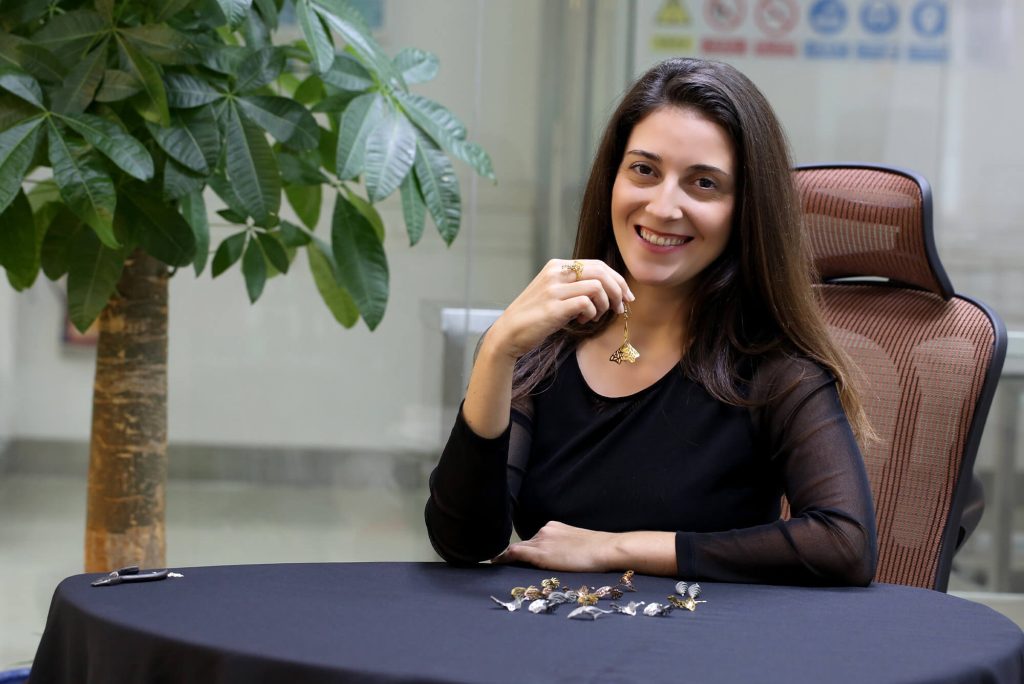
- Case Studies
- 3D Printing Jewlery
Technology Meets Fashion: 3D Printing Custom Jewelry Designs
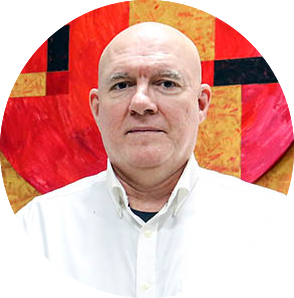
- Star Rapid
- 7 min
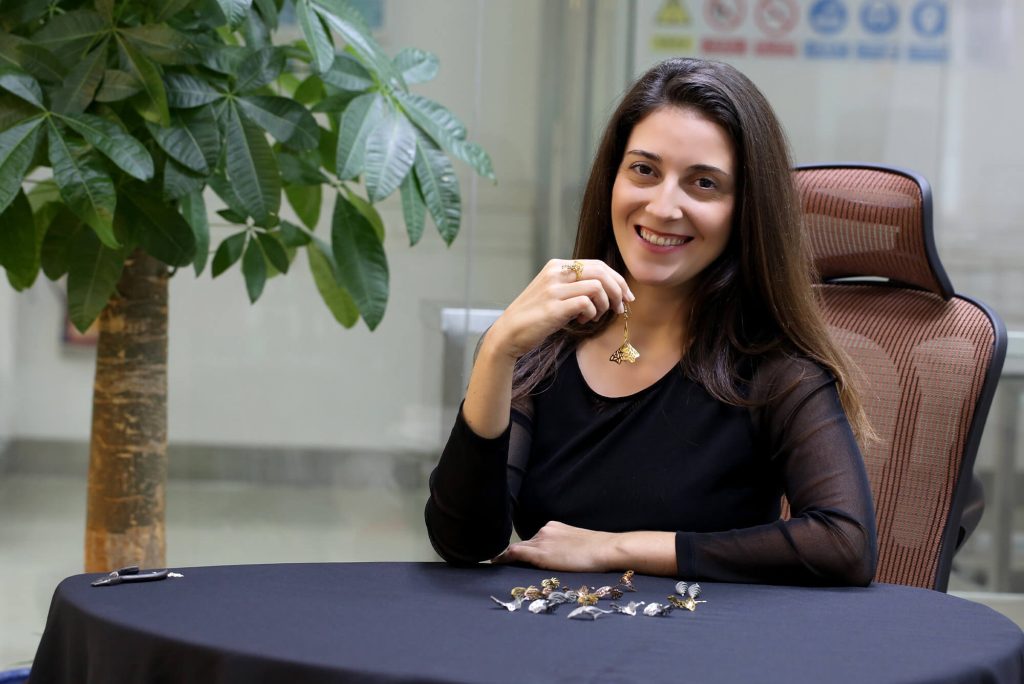
Company
V Nunes
ABOUT
A Jewelry Brand Based in New York City
Industry
Consumer Products Jewelry
Components
Necklaces
Rings
Earrings
Material
Ti6Al4V
Quantity
45 pieces
Services
- 3D Metal Printing
- Polishing
- Physical Vapor Deposition
Table of Contents
Company
V Nunes
ABOUT
A Jewelry Brand Based in New York City
Industry
Consumer Products Jewelry
Components
Necklaces
Rings
Earrings
Material
Ti6Al4V
Quantity
45 pieces
Services
- 3D Metal Printing
- Polishing
- Physical Vapor Deposition
“It was great that I could turn to Chloe [Kow, DMLM manager at Star Rapid] to bring my design concepts to life and create a line of one-of-a-kind pieces with carefully refined profiles and proportions. I was very happy to partner with Star Rapid to produce my 3D jewelry printed collection. Their machinery and facilities are state-of-the-art.”
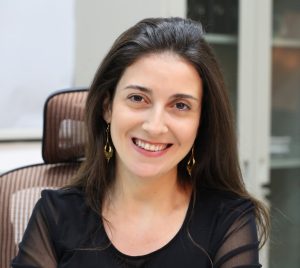
Jewelry Designer
Technology Meets Fashion: 3D Printing Custom Jewelry Designs
Veronica Nunes, a goldsmith and jewelry designer, wanted to experiment with 3D printing for a new jewelry collection. It was her first experience using this method, so she needed the right partners to handle the printing and polishing. Star Rapid fine-tuned the designs and printed and finished the pieces. Our partnership launched a collection ready for release.
The Challenge: Optimizing Designs for Additive Manufacturing
Veronica’s designs were unique, and they needed to be optimized for 3D printing, which usually requires design adaptations. Optimization has some requirements that are not always intuitive, so for this project we focused on improving the following areas:
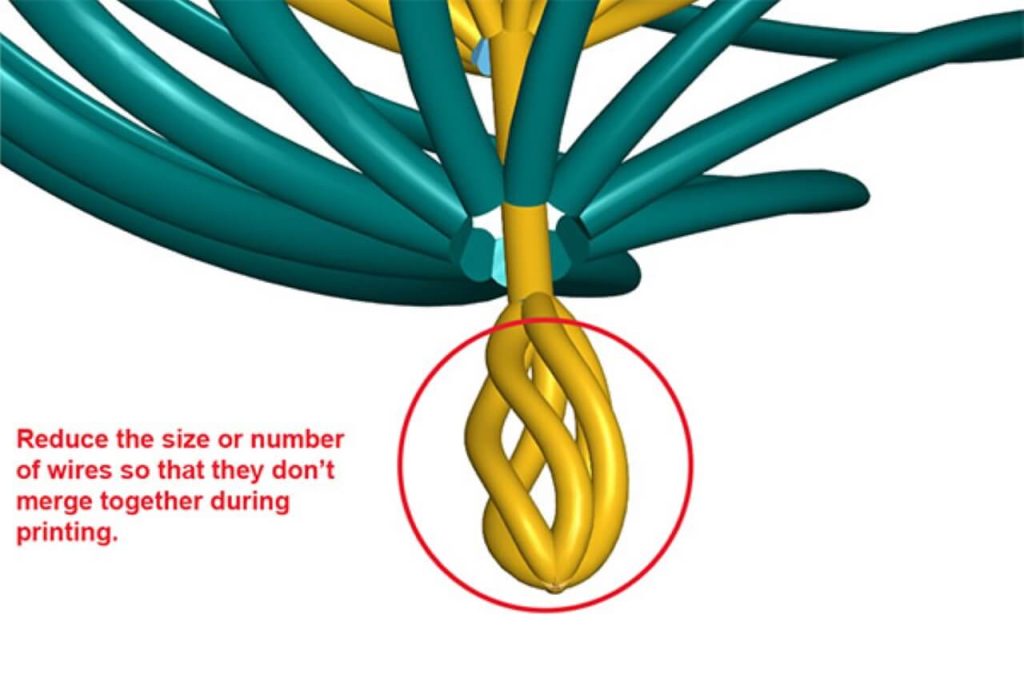
Wire Details of the Necklace:
The original design featured gaps smaller than 500 microns (or .5mm), which may blend in a single mass when printed. We suggested reducing the number of twisted lines so they’d be more clearly separated.
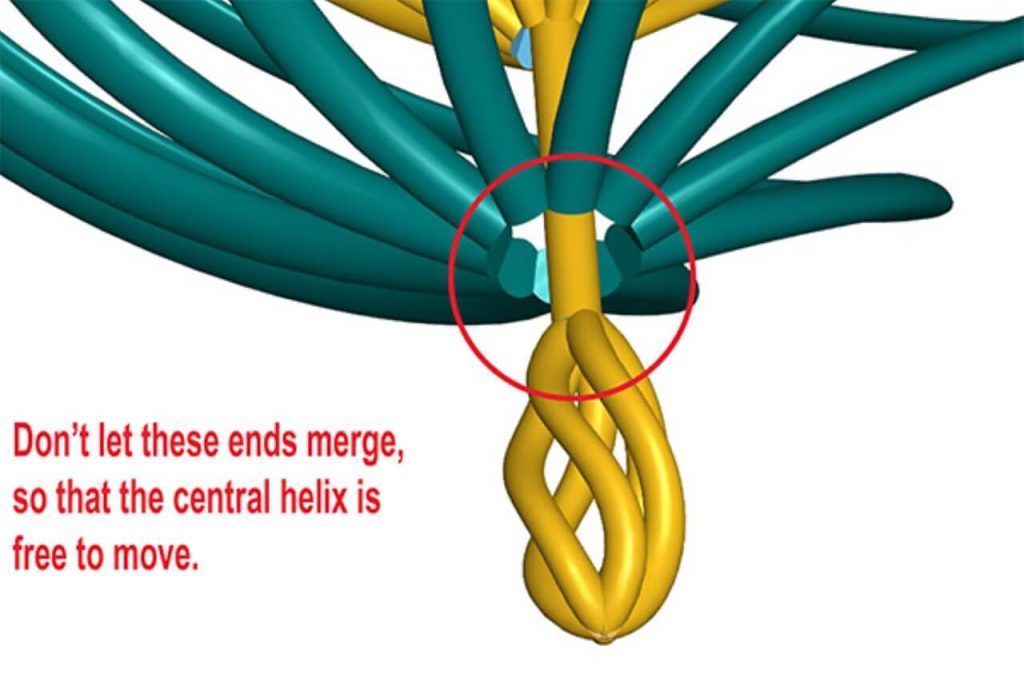
Moving Parts:
One design featured a moving part within a part that required sufficient clearance for the desired effect. Without the necessary clearance, the parts could become welded together during printing, impacting the functionality and aesthetics.
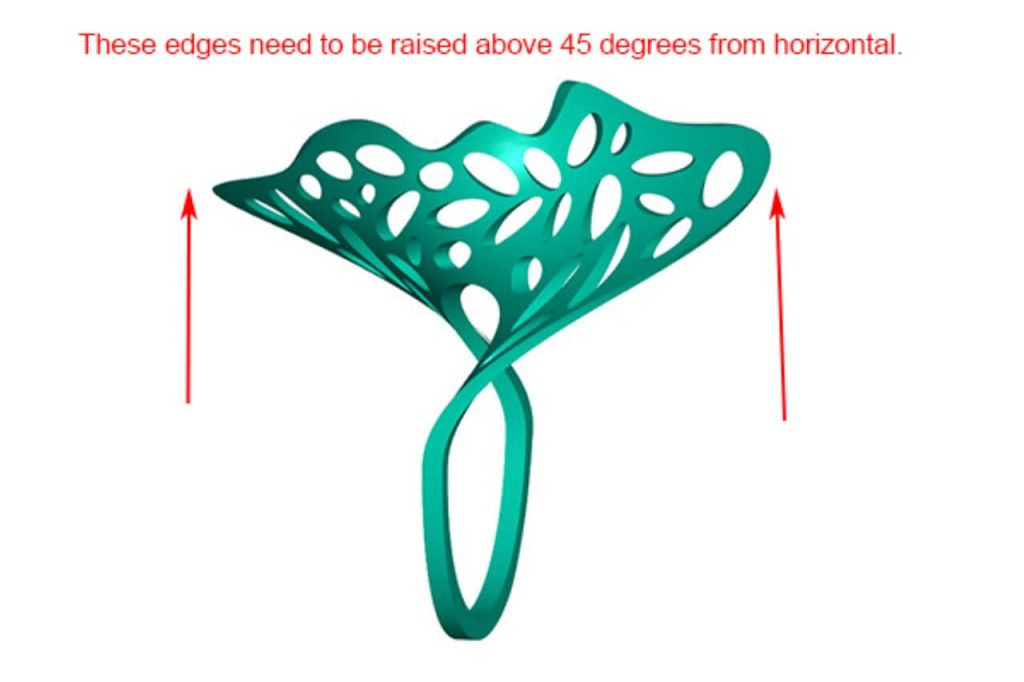
Overhang:
Overhanging features with less than 45 degrees may collapse under their own weight during printing due to the pull of gravity. We recommended elevating these sections, especially in thin areas that are not able to support themselves.
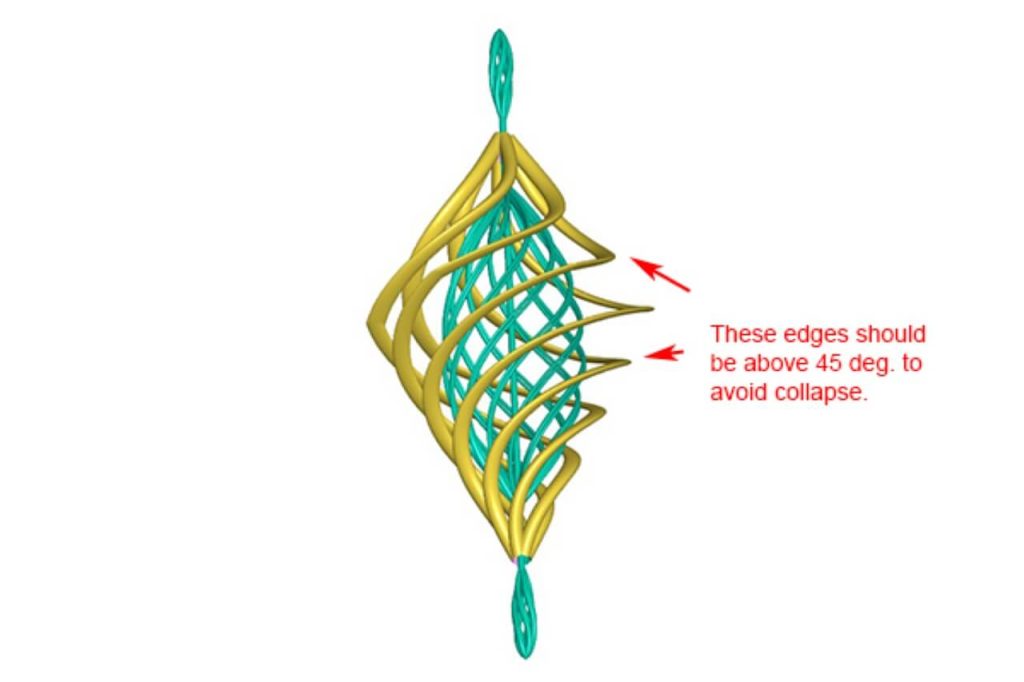
Blade Details:
These thin coils forming the outer helix are not actually round in cross-section but rather flattened out, like thin blades. It is the same as the overhangs: the leading edges of the blades should remain above 45 degrees horizontally to give it structural integrity when building.
The partnership between the designer and manufacturer was crucial for this project. Designer Veronica Nunes collaborated closely with Chloe Kow, Manager of Direct Metal Laser Sintering at Star Rapid. Together, they made slight modifications to the designs to ensure each area would perform as expected.
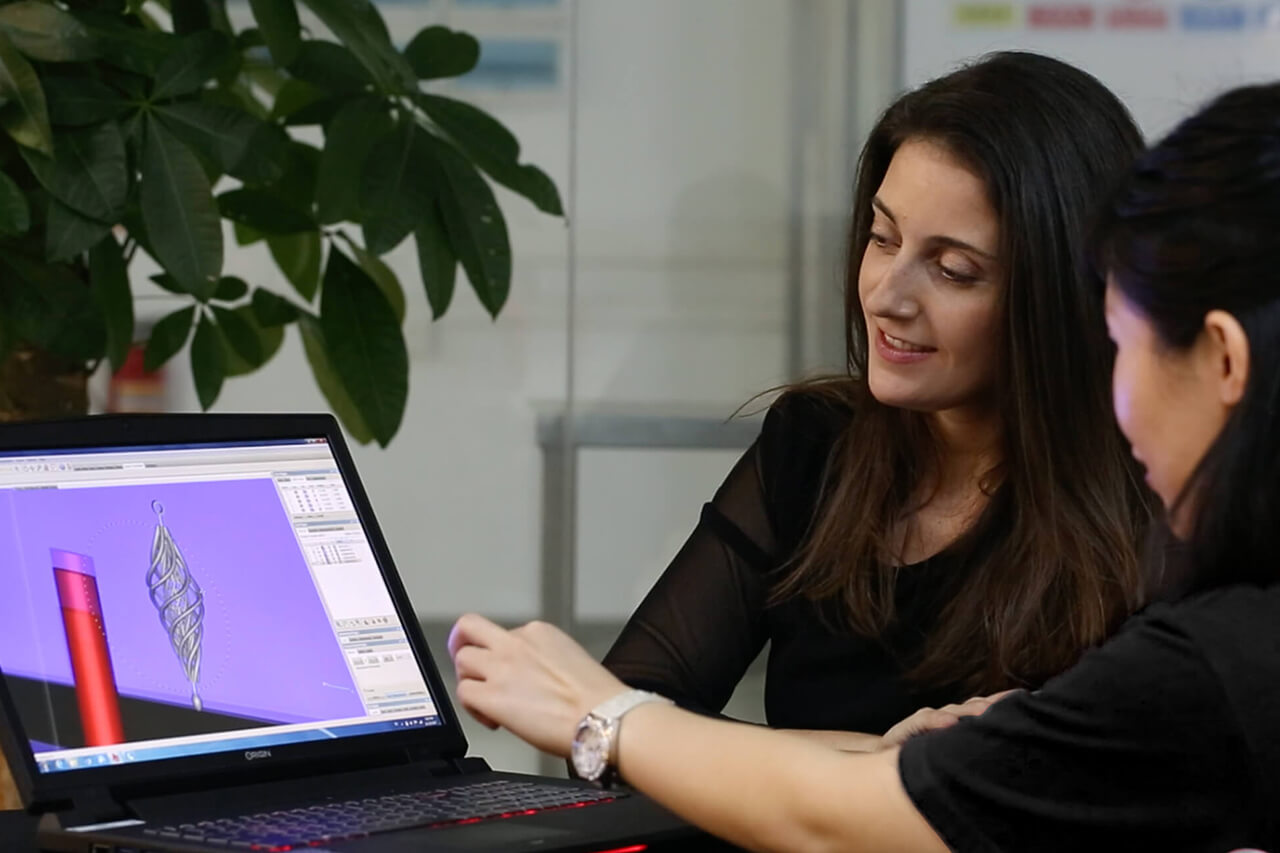
Without this partnership, parts might blend or deform unexpectedly during printing.
The Material: Ti6Al4V
For this build, Renishaw’s blend of Ti6Al4V powder was used. This high-purity titanium alloy is mixed with up to 6.75% aluminum and 4.5% vanadium, along with other minor elements.
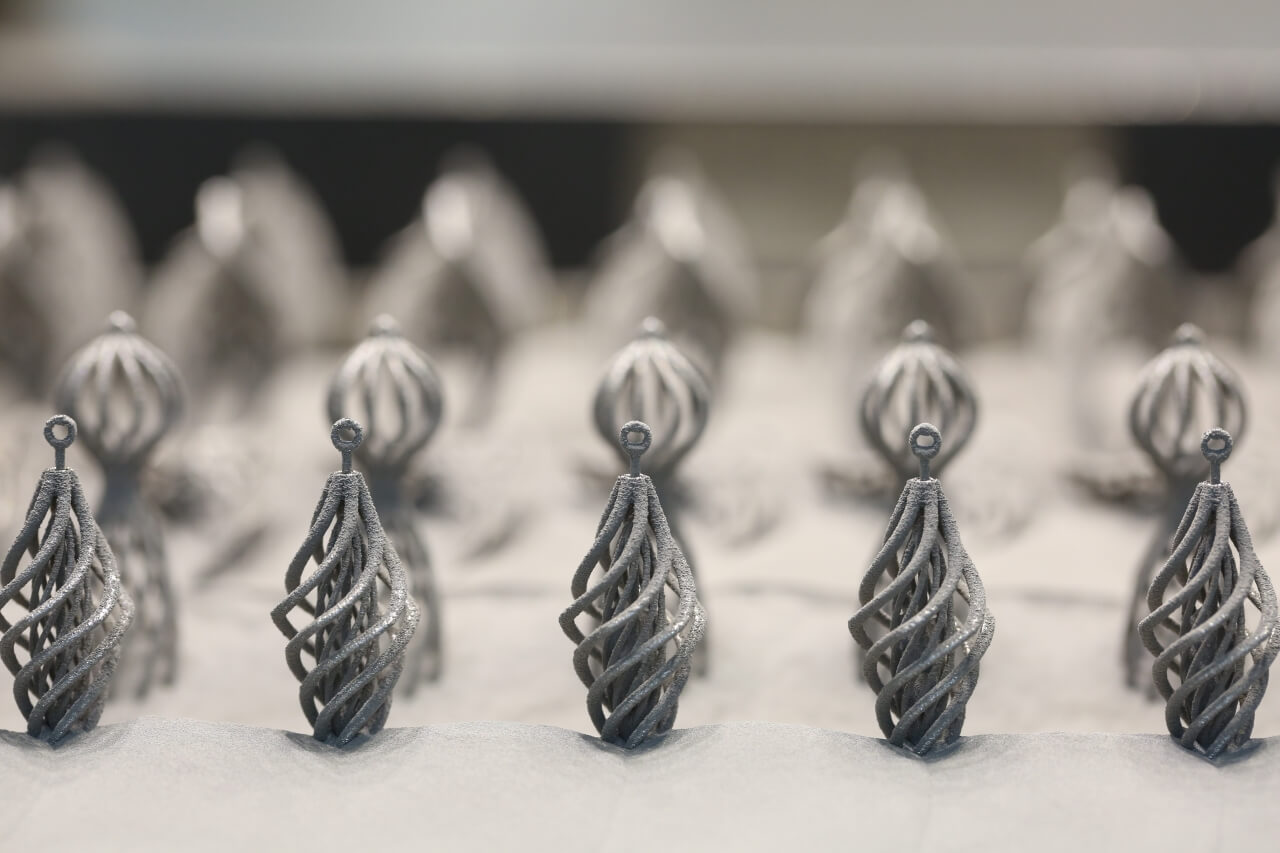
The nature of this very fine powder makes it dangerous if handled improperly. That’s why we have several safety and control measures in place, like operating in a temperature and humidity-controlled environment.
Ti6Al4V is commonly used for jewelry and art crafts mainly due to its strength-to-weight ratio and corrosion resistance. It also has excellent biocompatibility, which makes it comfortable to wear and reduces the risk of allergies.
Our Approach: 3D Metal Printing and Surface Finishing
Production was relatively straightforward once the design suggestions were approved. Our two-step approach was simple, yet effective.
- 3D metal printing using a direct metal laser melting (DMLM) machine.
- Surface finishing using hand polishing and applying a physical vapor deposition (PVD) coating to the pieces.
We prioritized a high level of attention to detail, both to identify opportunities for improvement and to ensure rapid production and efficient material usage.
Metal 3D Printing
For this project, we used our Renishaw AM250 printer. This state-of-the-art direct metal laser melting (DMLM) machine uses a 200W ytterbium laser to fully melt metal powders into dense solids.
The first step was to input the designs into the control software, where they were sliced into thousands of discrete 2D layers. Then, we could start printing layer by layer.
All jobs begin on a build platform that can move up or down on the vertical axis. Once the first layer was fused to this platform, it was then lowered by the thickness of one layer to prepare for the next. Additional powder was recoated over each layer by a wiper blade.
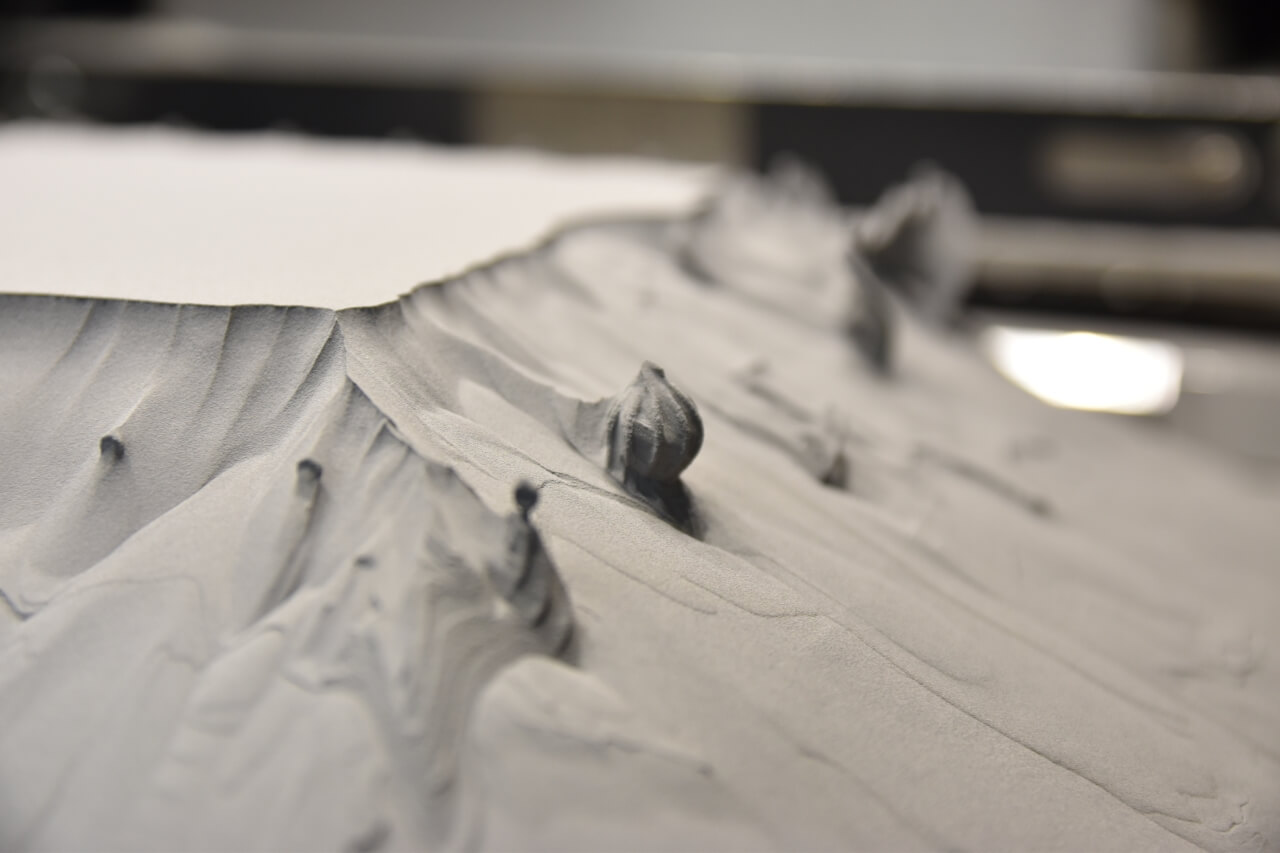
This all happened inside a sealed chamber filled with inert argon gas to prevent rapid oxidation and potential explosions. It’s especially important when working with reactive powders like titanium and aluminum.
Note the part’s orientation. Production was arranged to make maximum use of the build volume by placing different shapes on the same platform. This limits the number of supports needed while preserving the part’s geometry.
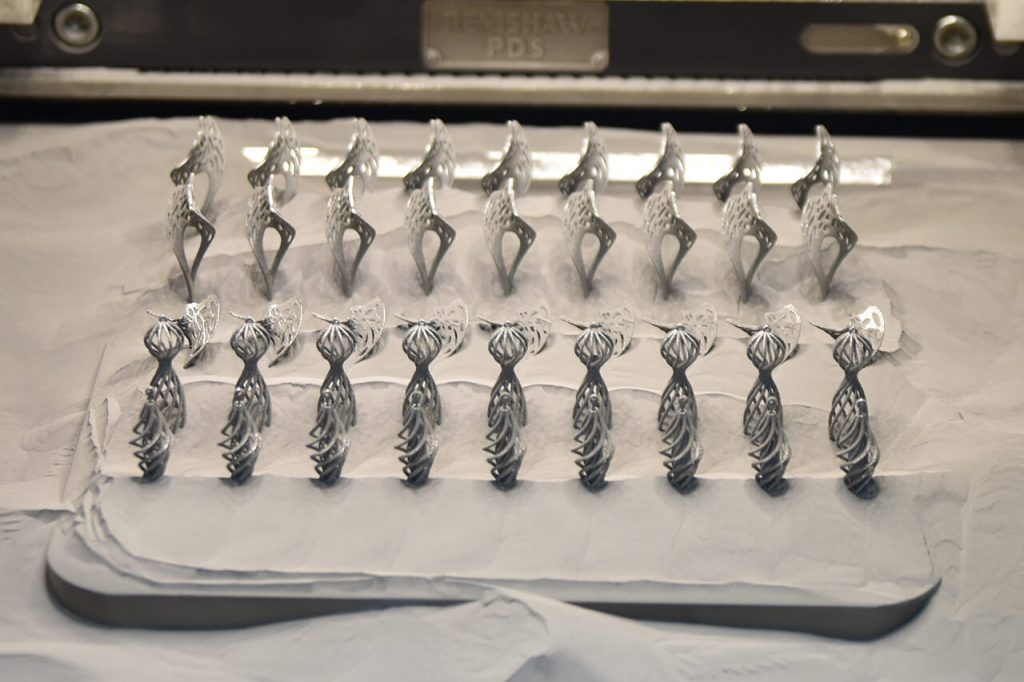
As the layers were printed, excess powder was carefully brushed away, revealing the rough-shaped parts. This excess material can be sieved, dried, and reused for other builds in the future. Each piece was removed from the plate by cutting or grinding them free, and while this is a relatively easy task for small jewelry, it can be challenging for larger creations.
Once the printing was complete, the items still had a rough appearance, as you can see below. That’s where post-machining or processing comes in. In this case, the jewelry was set to be polished and coated.
Surface Finishing
After being inspected, the pieces went to our finishing department where they were polished using hand and machine tools by our craftsmen.
They first deburred the parts, removing rough or sharp edges left from the printing process, and then sanded them to smooth out the surfaces. Next, the parts were buffed to achieve a high-quality finish.
Most of the accessories were hand-polished, except for a spinning earring design. Some parts were difficult to reach, so they were placed into a tumbler to be polished with fine abrasive sand before plating.
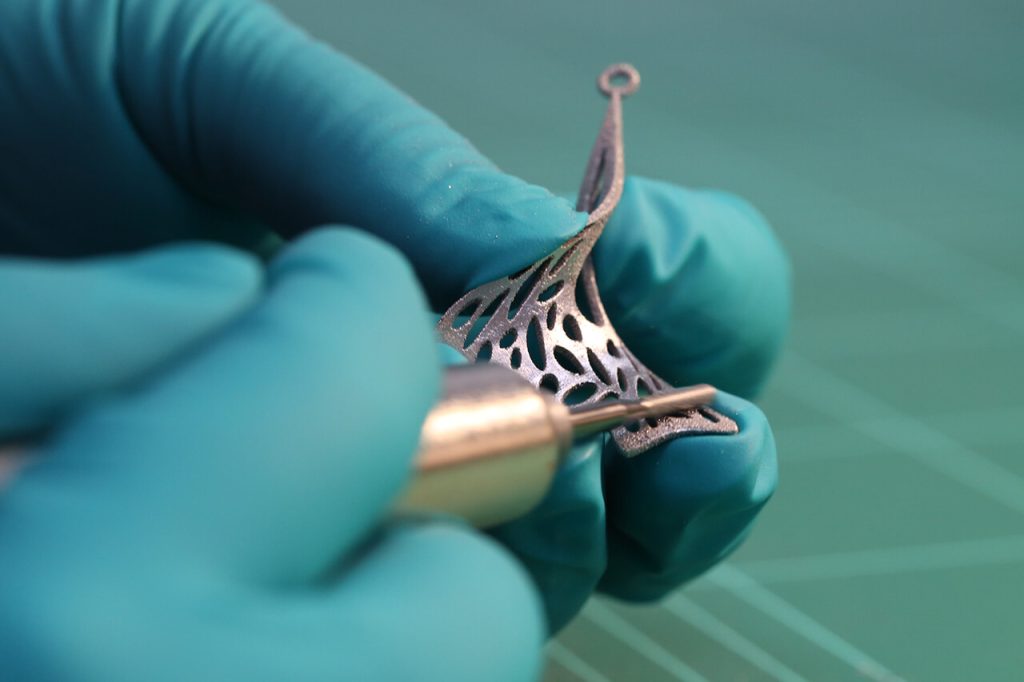
The pieces were cleaned and sent out for a physical vapor deposition (PVD) coating that condenses on the jewelry to form a uniform and durable finish. The coating gives the jewelry its unique color and protects it against corrosion over time.
The Result: A Jewelry Collection Ready for the Runway
They were released with the following names:
- Butterfly Ring and Earrings, featuring delicate forms.
- Giro Earring and Double Twist necklace, boasting bold and elegant shapes.
The Importance of Production Partnerships
After releasing the products, Veronica Nunes shared her feedback about the process in an exclusive interview. She noted learning a lot from working with additive manufacturing and shared hopes of making new collections using this method.
Veronica said she chose Star Rapid because:
- Our product design for 3D printing is more complex than for traditional jewelry processes.
- It allowed her to create unique items with complex shapes, small holes and openings, and moving parts.
- The process was relatively inexpensive and easy to modify as needed.
In her interview, Veronica highlighted the partnership between designer and manufacturer when creating beautiful accessories – which she described as “small wearable pieces of art.”
It’s exciting to see a client so satisfied after manufacturing because it’s the result of communication at every step of the way, careful engineering, and years of engineering expertise.
Star Rapid no longer offers metal 3D printing services, but we remain fully committed to helping customers reach their product development goals by offering a variety of rapid prototyping and low-volume manufacturing services.
Upload your CAD files today for a free quote tomorrow. No matter the size or scope of your project, you’ll receive the same professional service and meticulous attention to detail that sets us apart.