Automated Sun Visor Components Case Study
Services: CNC Machining, EDM, Polishing, Plastic Injection Molding
Materials: Tooling – Al-7075, Plastic Injection – PA66, 15% glass fiber-filled
Lead Time: 12 days
Quantity: 1500~2500 units
About The Product
These parts are an essential part of a larger assembly, used in an automated sun visor as aftermarket equipment on recreational vehicles (RVs). The gear and roller shaft needed to be made from strong engineering plastic that could also withstand prolonged exposure to high temperatures and UV light.
How The Parts Were Made
Preparing The Mold
The customer needed two parts of different sizes and shapes. However, since both parts would be made from the same material and in the same quantity, it made sense to create a single two-cavity mold. This also saved time and money.
The long roller tube was specified with a thickness of only .5mm, making it a particular challenge.
Material Verification
We used aluminum 7075 for the plastic injection mold tooling, which is relatively easy to machine and is good for up to 10K cycles. We verified the raw material using an optical emission spectrometer (OES), which employs X-ray scanning to identify the exact constituency of the metal.
Electrical Discharge Machining And Polishing
We machined a conductive electrode from copper, in the precise size and shape as the feature we want to reproduce in the mold. EDM cuts metal with an electrical charge and it does so quickly and with high fidelity, but the electrode itself is consumed in the process and so is considered sacrificial. We made ten electrodes to form the two cavities.
After machining, the surface of the cavity was carefully polished by hand. This texture was transferred to the plastic when it was molded.
Machined Inserts
Inserts are sections of the mold tool which can be removed separately from the main tool. They allow certain features to be molded correctly, but they also add complication and expense. Hand loaded inserts allowed us to keep costs down and also to stay on our tight schedule. Hand loading is slower than automated sliders, but for a relatively small order this is an acceptable compromise.
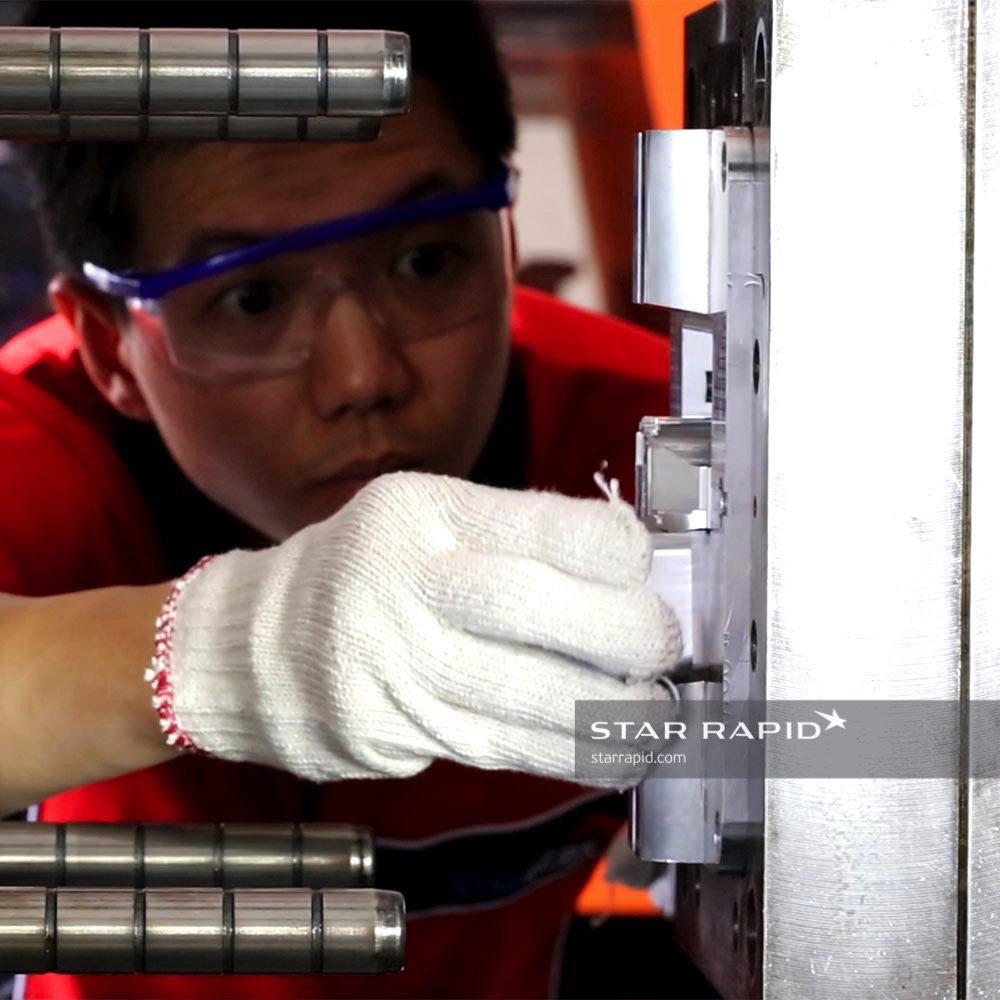
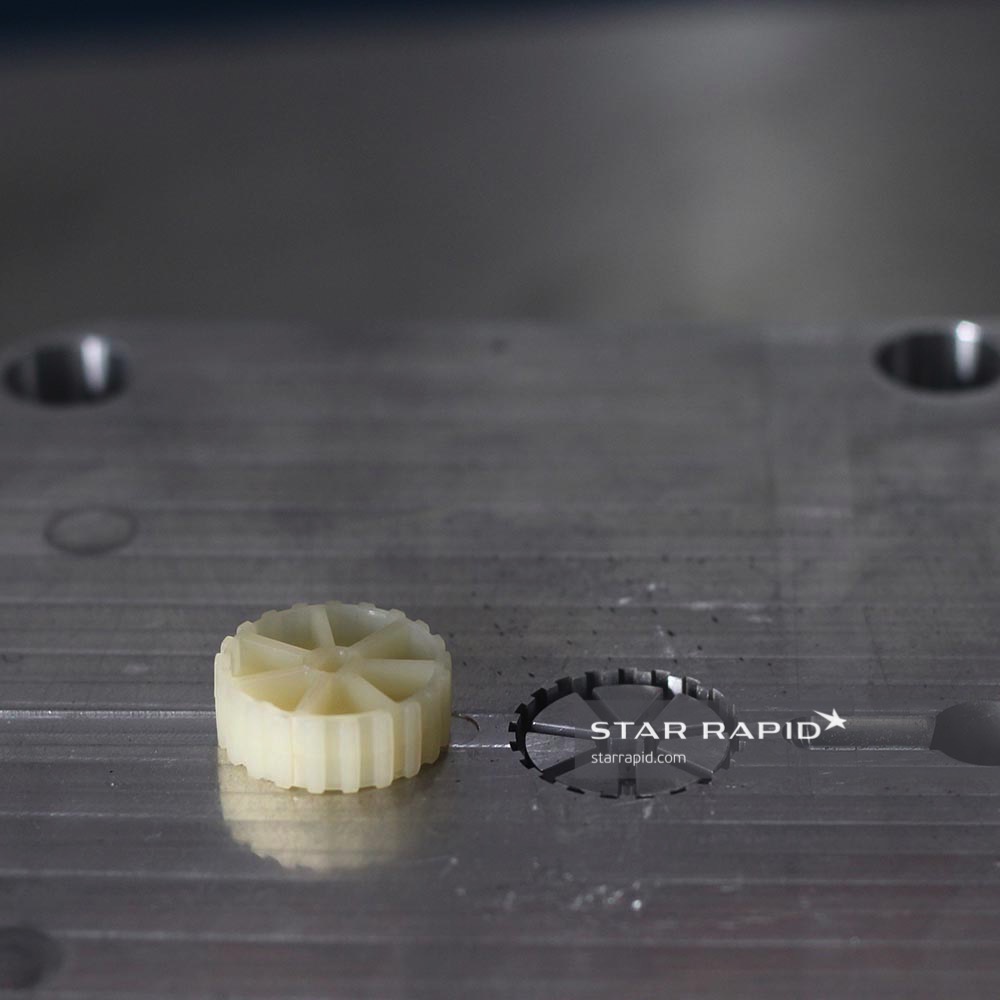
Plastic Injection Molding
The dies consist of a core half and a cavity half. Both of these are put into our standard fixtures or “Master Unit Dies”. We chose to inject PA66 +15% glass filled plastic. This is one variety of nylon, strong and temperature resistant. It also readily accepts paint if the customer desires.
To achieve the required 0.5mm wall thickness, careful attention was paid to the mold tool design, including cooling channels, so that the part would not be warped.
After injection, the parts turned out perfectly and the customer was delighted that we did all of this in 12 days!
To see how we can apply the same level of service to your next project, contact us today for a free quotation and design review!