Pressure Die Casting a Smart Door Lock and Security Camera For Gate
Services: Pressure Die Casting, Plastic Injection Molding, Compression Molding, Nickel Plating, Hand Polishing, CNC Machining, EDM Machining, Sandblasting
Mold Material
Compression Mold: Series 50 Carbon Steel
Pressure Die Cast Mold: H13 Tool Steel
Plastic Injection Mold: Al-7075
Part Material
Keypad: EPDM Rubber, multiple Shore hardnesses
Lock Housing: Zinc, Aluminum
Cover: Nylon
Plating Material: Nickel
Quantity
Several hundred (for testing)
Lead Time
3 weeks
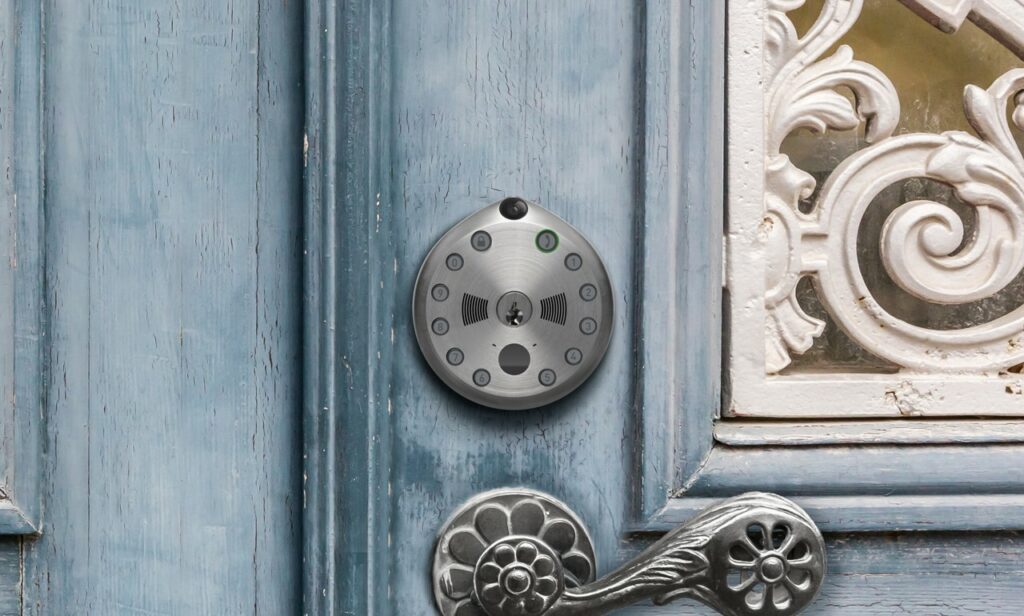
About The Product
The Gate smart lock is the first all-in-one solution for home access. It provides door entry with or without a key, and when paired to a smartphone via the app, the camera and microphone on the lock helps the homeowner see and talk with anyone who comes to the door. This also allows for remote access for a range of purposes such as receiving deliveries.
About The Client
The Gate smart lock was designed by Gate Labs, a group of entrepreneurs dedicated to providing solutions for busy people who increasingly manage their lives via e-commerce, smartphone and computer. For those who can’t make it to the door to receive packages or arrange for in-home services, the Gate lock is the answer.
Product Development
The Gate smart lock took three months of design iterations before the first prototype was made. From that initial prototype, more than ten different designs were tried and tested before arriving at the current version.
A complex product like this needs to not only function perfectly but it must also satisfy a number of aesthetic challenges. Does it look and feel like something high-quality? Is it secure and robust? Will it blend in with different homes, apartments and office designs? One of the reasons that Gate chose to work with Star Rapid is that they were convinced we could provide a sophisticated fit and finish while still keeping the development costs down.
Design for Manufacturing Review
Achieving a great finished result required getting all the details right before the first cut was made. To do this, we completed a design for manufacturing (DFM) review to check that the design was optimized for manufacturing and to address any potential problem areas. As part of the DFM review, our engineers looked over Gate Lab’s 2D and 3D CAD files for the eight separate components.
In some areas we suggested a change to the design or a replacement material. In other areas it was necessary to confirm with the client any process parameters that would affect the finished part, like the location of gate marks and parting lines for injection molding tools. We’ve found that the time spent in a careful and thorough design review will save much more time and money later during manufacturing. Through the DFM review the following feedback was provided for discussion with the client:
Post-Machining
After pressure die casting, several areas on the shell and internal components needed post-machining to achieve the final specifications. We identified a few areas requiring special attention.
Making the Mold Tools
We made six mold tools for eight components: one for compression molding of the membrane rubber keypads; one for plastic injection molding of the plastic cover, and four pressure die casting tools. Note that one complete mold tool consists of a separate cavity side and core side.
Tool One – Compression Molding
Compression Molding Tools. The male and female halves were CNC machined out of #50 carbon spring steel. Several different Shore hardnesses of EPDM rubber were tried, between Shore 30 up to Shore 90, so the client could test which one has the best reception from the market.
Tool Two – Plastic Injection Molding
Tool Three – Pressure Die Casting
Tool Four – Pressure Die Casting
Tool Five – Pressure Die Casting
Are You Working On A Similar Project?
The Gate smart lock is now being environmentally tested and we look forward to seeing this product actively in use and providing a great solution for busy, connected people everywhere. Have you got a great product you can’t wait to launch? Upload your CAD file for a free quotation and let us help you get started changing the future!
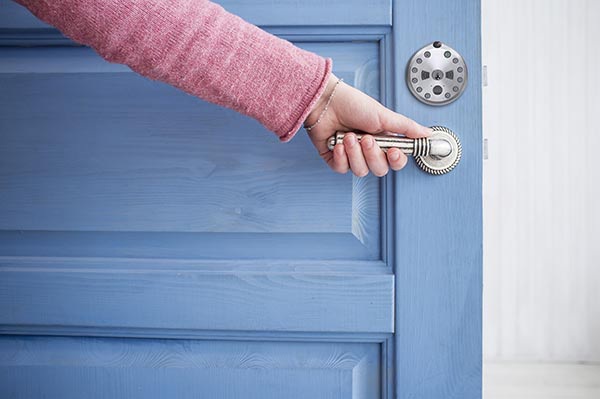