- Case Studies
- Primary Fluid Case Study: CNC Machining of Metering Nozzle
Primary Fluid Case Study: CNC Machining of Metering Nozzle
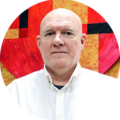
- Star Rapid
- 4 min
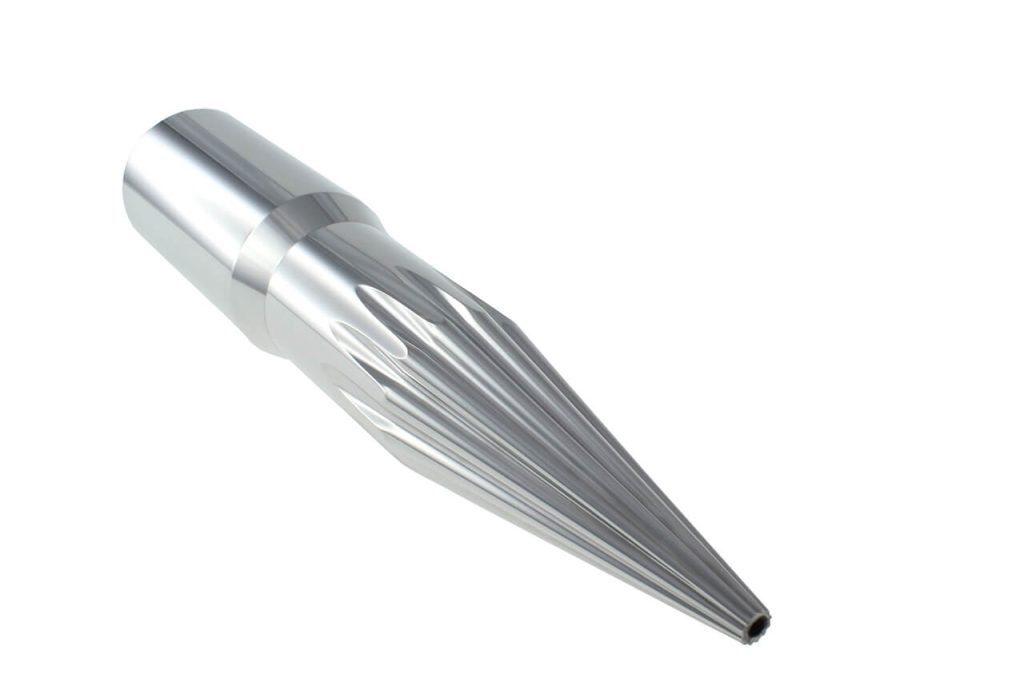
- Case Studies
- Primary Nozzle Case Study
Primary Fluid Case Study: CNC Machining of Metering Nozzle
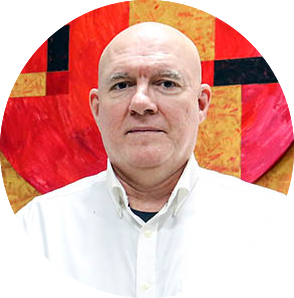
- Star Rapid
- 4 min
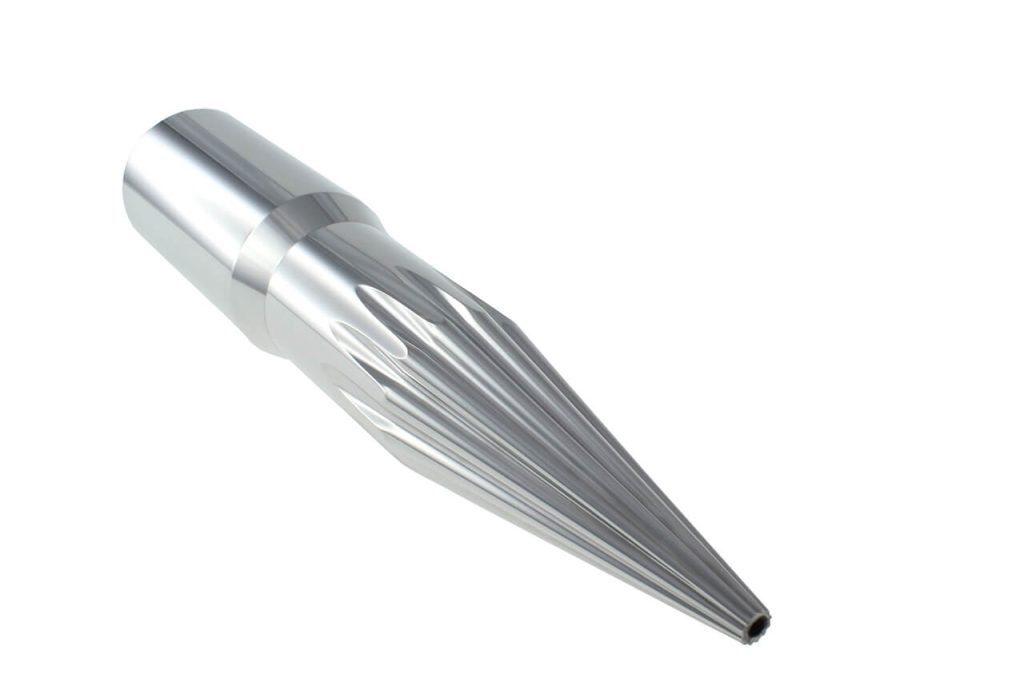
Company
Primary Fluid
ABOUT
A Provider of Components for Fluid Management Applications
Industry
Fluid Metering
Components
Meter Pump Nozzle Prototype in Three Variations
Materials
Stainless Steel
Quantity
3
Lead time
10 Days
Services
Table of Contents
“Star delivered these parts quickly and professionally. The prototypes met the high standard I demand from any supplier and are currently being fine-tuned before the applications for patent are submitted.”
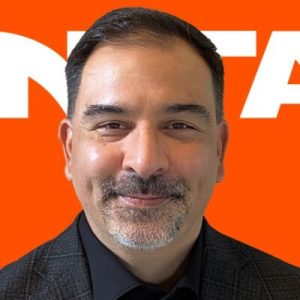
Buyer, Primary Fluids Inc.
Prototyping a Fluid Metering Nozzle (in Just 10 Days)
In industries like water treatment, oil and gas, or pharmaceuticals, even minute deviations in fluid control can affect performance and efficiency of their operational processes. Primary Fluid created a new prototype to enhance precision in these critical environments. It features a complex design, perfectly manufactured by Star Rapid in just 10 days.
The Challenge: Overcoming Precision and Time Challenges
The project presented three main challenges related to the product features and production time:
- Machining a series of grooves along the tapered external nozzle
- Boring an accurate center hole
- Making the prototypes as fast as possible
Agility was key because Primary Fluids was starting the patenting process, and receiving the parts promptly would give them an important competitive advantage.
We selected CNC turning and CNC milling as the primary manufacturing methods since turning is the best way to create cylindrical shapes and bore center holes, and milling is more efficient for making the grooves.
We overcame the challenges of the pump nozzle design by using advanced equipment. An imported lathe allowed precise production in a short time, and fine cutters created excellent surface finishes and eliminated the need for extensive post-finishing.
Skilled operation of such machinery was also crucial. All operators in our factory are experienced in G-Code, the programming language used to control each cutting, drilling, and turning movement. They are experts in setting up, operating, and editing cutting programs whenever necessary.
Our Approach: Making the Metering Nozzle Prototypes
We started by analyzing the design files sent by the client to determine the best method of manufacturing. Then, we performed Positive Material Identification (PMI) to examine the composition of the stainless steel used to make the parts to ensure its compliance with the project requirements.
Next, our specialists programmed the machines using a complex process that involves fully configuring the lathes and mills. They created tool paths; selected cutting tools; set parameters such as speed, feed rate, and cutting depth; and ran simulations to test everything.
Then, the machines were set up with the selected tools, and the solid blank of steel was securely fixed in place. The grooves on the external part of the nozzle were made using one of our CNC mills with a 2mm ball-nose cutter to achieve the necessary tolerances.
We machined three slightly different versions, and we sent all of them for inspection in our quality control department, where our operators verified the part’s dimensions, profile, shape, and finish.
Prototypes only leave our factory after passing this thorough inspection. That’s not an extra feature—it’s standard procedure at Star Rapid.
The Result: Complex Parts Delivered in Just 10 Days
The components were produced from start to finish in just over a week. Primary Fluids received the three pump nozzle prototypes right at their doorstep, with the quality necessary for use in technical tests before submission for patenting in Canada.
This was the result of millions invested in cutting-edge technology. Without imported machines, the best cutting tools, and a state-of-the-art inspection department, it would have been very challenging to deliver high-quality, complex parts in such a short time.
We take pride in these investments because they directly impact our client’s experience and market performance. In this case, using outdated equipment would mean slower production and higher costs, which would lead to poor market timing.
Our commitment to delivering the most advanced solutions to each client is ongoing. Since the production of these parts, we have continued to invest annually in facilities, equipment, and instruments.
Take a virtual tour of our factory in 2024
Want to see firsthand how we leverage these technological capabilities to deliver highly precise parts? Come visit us! Our facilities are located in Zhongshan, just a 90-minute ferry ride from Hong Kong.
“My aim for Star is to position it at the forefront of technological development in the rapid prototyping industry. This process has already seen us invest well over £1million in new machinery and technology during the last two years and will certainly see us invest considerably more in the near future.”
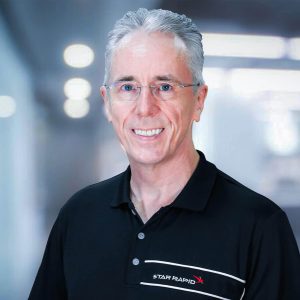
CTO and Founder, Star Rapid
Reliable Prototyping Solutions for Every Project
At Star Rapid, we have more than 20 years of experience in turning complex designs into reality with precision and speed. Whether you are creating prototypes for technical testing, showcasing in a showroom, or fine-tuning a design, our rapid prototyping solutions are ideal for producing functional, market-ready parts.
Contact us now for a free quote and start working with an international team that can help you achieve perfection in your next product launch.
Rest assured, your parts will be made using the most advanced technologies available on the market, from raw material verification to the manufacturing and inspection of the finished pieces.