IHMC Robotic Exoskeleton Case Study
Services: CNC Milling and Turning, Bead Blasting, Hand Sanding, Anodizing
Material: Brass, Stainless Steel, AL-6061
Quantity: Two complete sets with spares, 18 components per set
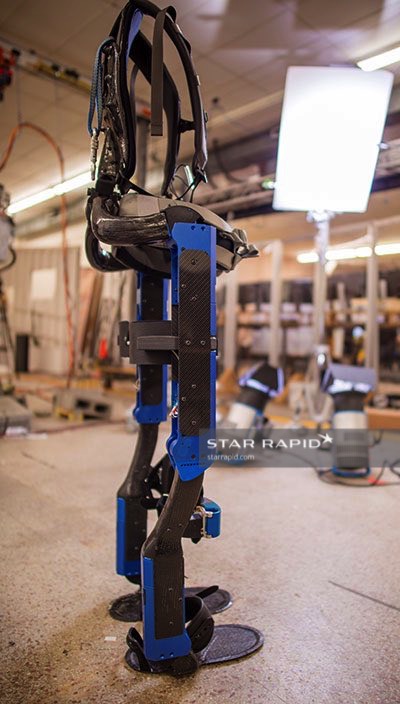
About The Product
The Mina v2 is a powered robotic exoskeleton designed to provide assisted mobility to people with a physical disability. Using microcontrollers, sensors and electric motors with a sophisticated user interface, the Mina v2 will compete in an international robotics Cybathlon in Switzerland in October. We were so excited about this project that we are now proud sponsors of IHMC for this competition. The Cybathlon will showcase Mina’s ability to climb stairs, maneuver through an obstacle course and negotiate uneven terrain.
About The Customer
The Institute for Human and Machine Cognition (IHMC) is a not-for-profit research institute. From artificial intelligence to virtual reality to cybersecurity, they work in a number of disciplines relating to the interactions between humans and machines, with the purpose of enhancing the abilities of both.
Dr. Peter Neuhaus, director of the exoskeleton project, contacted Star Rapid to help them make custom parts.
About The Project
After completing a design for manufacturing review of the project, our team set to work making the components.
A project like this requires that all parts are made to tight tolerances, and that they fit together seamlessly to build the complex three-dimensional geometry required of a moving robotic device. During the course of manufacture, there were a few areas that needed special attention.
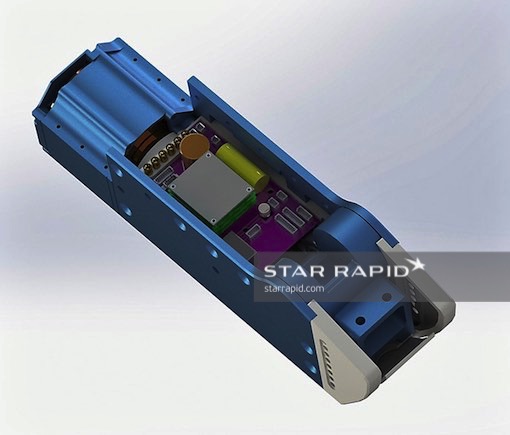
CNC Machining
The main process used to make the steel, brass and aluminum parts for the MinaV2 was CNC machining. Each part was made using a tool and CNC machine appropriate for the level of tolerances and angles required.
A turning center is the best way to make precisely round and concentric parts like this spring mount. Here a stainless steel rod is held firmly in the jaws of the rotating chuck to prevent any unwanted vibration as it’s being turned down to the final size.
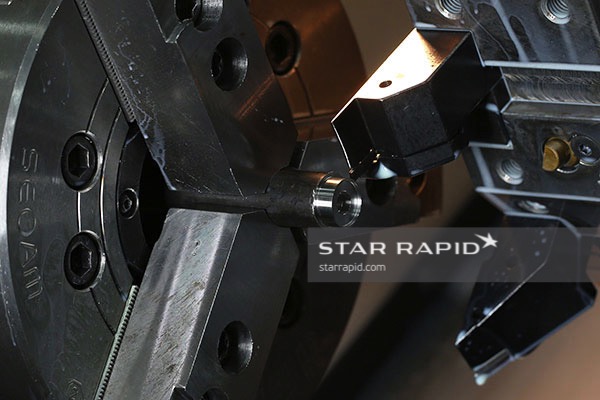
The Challenges When CNC Machining
Challenge 1: Keeping Tight Tolerances
With the need for such tolerances we decided to machine the most complex parts on our 5-axis CNC mill. Having such equipment helps to avoid moving the piece from one holding fixture to another on different machines, which makes it tough to hold tight tolerances.
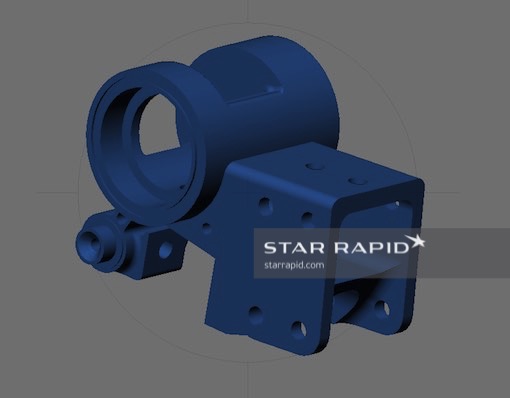
Challenge 2: Holding The Part
This parallel spring mount has multiple faces with rounded edges that make it difficult to hold properly when drilling out the center hole. In the end, we created a special fixture to hold this part securely to maintain the right dimensions.
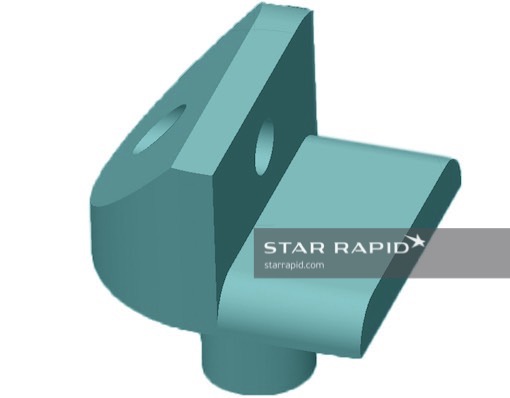
Not all alloys accept the anodizing treatment equally well, but AL-6061 is a good choice and produces nice results. After bead blasting and cleaning, the aluminum has a non-reflective, matte finish. We mount individual parts on trees to keep them from touching one another before going into the anodizing tank.
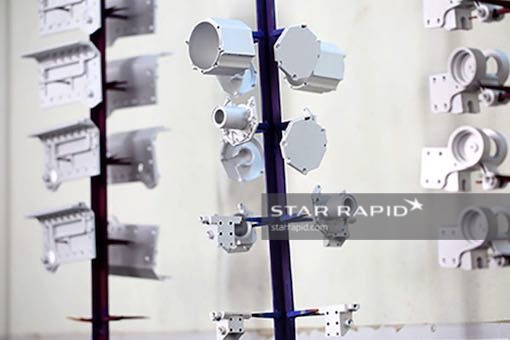
After anodizing, parts have a uniform, semi-gloss dark blue metallic coating.
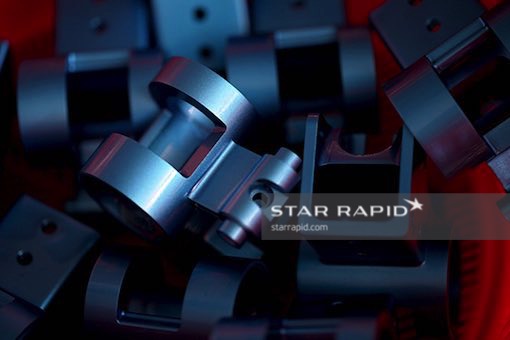
Anodizing adds a thin layer of material onto the surface, about 3~5 microns. This is enough to interfere with close fit tolerances and machine threads, so threaded holes must be cleaned after anodizing, exposing bare metal.
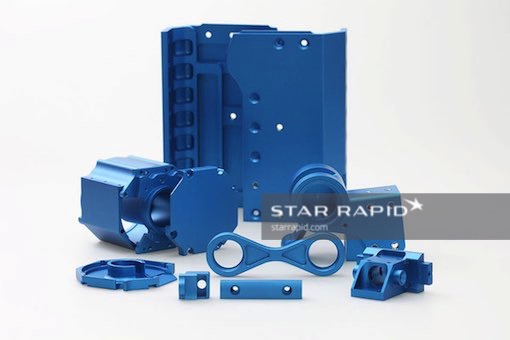
We delivered the parts to the client, where they added all the extra hardware to make a functional unit: O-ring seals, bearings, load cells, motors and control electronics.
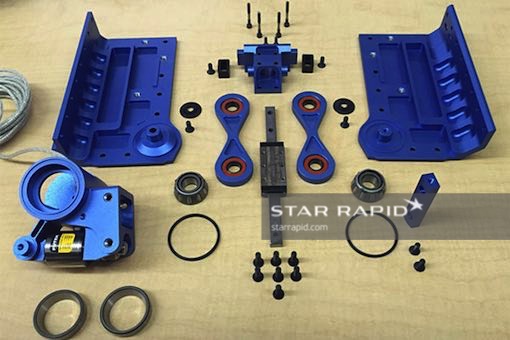
The Finished Product
The finished parts have now been delivered to the team at IHMC and the assembled robotic exoskeleton will undergo extensive testing in preparation for the Cybathlon to be held in October. The Mina V2 was a great project to work on, and we wish them all success in the upcoming competition. We’re proud to have played a small part in bringing to life IHMC’s mission for enhancing human potential through the intelligent application of technology.
If you need help with your next project, contact us for a free quotation and project review.
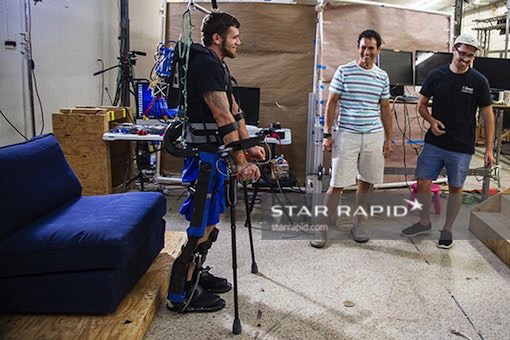