Stem Cell Isolator Chamber
Services: CNC Machining, Annealing, Polishing
Material: Ultem 1000 Polyetherimide
Color: Natural (amber)
Quantity: 3 sets of 3 parts each
Lead Time: 6 days

The Customer
Biorep, an ISO 13485:2016 certified medical product development company, enables advancements in medical technologies by offering the single source solution for healthcare professionals and researchers worldwide through a collaborative commitment to the design, development, and manufacturing of innovative biomedical products to improve the quality of life for patients.
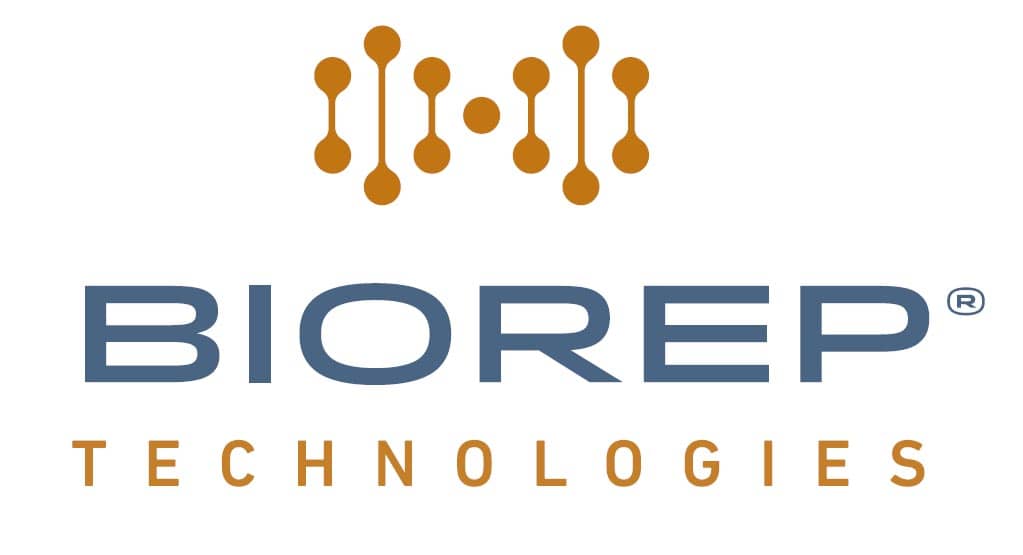
The Product
We were approached by Biorep to help them make a stem cell isolator chamber to support their work with the Cure Alliance. They are a U.S.A. non-profit working together with their Italian counterpart Fondazione Cure Alliance ONLUS. Their group of multidisciplinary scientist, doctors, and technicians are applying their expertise in stem cell research towards creating an IV infusion of umbilical cord stem cells to prevent acute lung inflammation caused by COVID19.
Together with Dr. Camillo Ricordi of the Cure Alliance, engineers at Biorep designed a stem cell isolator that will be used in the second wave of trials which will start after proof of safety and early efficacy with the current trial. Validation runs on the cell products obtained with the stem cell isolator are underway prior to using them clinically.
The Project
Because of the urgent nature of the unprecedented COVID19 outbreak, Biorep Technologies contacted Star Rapid and asked for a rush job to make parts for the stem cell isolators. We at Star want to do our part to support these life-saving efforts, so we quickly rearranged our production schedule and placed an immediate order for Ultem 1000 polyetherimide plastic resin.
While awaiting the arrival and testing of the resin, we also converted Biorep’s 3D CAD files into G-code programs for digital manufacturing.
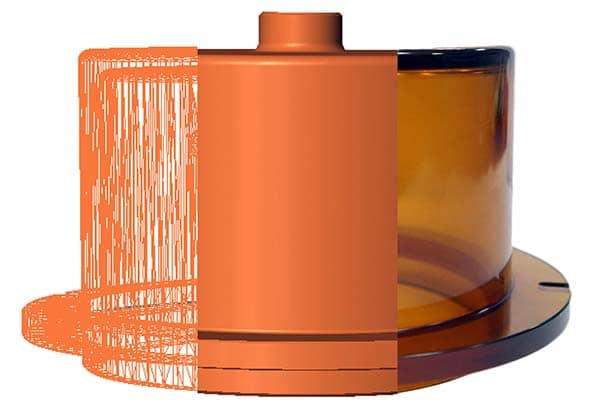
Ultem 1000
Like other polyetherimide resins such as PEEK, Ultem is an engineering grade plastic. That means it’s much stronger and more rigid than most thermoforming plastics. It can resist sustained high temperatures and chemical attack, so it’s useful in medical appliances that are routinely steam sterilized. Although it’s possible to plastic injection mold Ultem, we used CNC milling and turning for this project. This is because the customer only needed a few parts and we had to produce them fast while also maintaining tight tolerances.
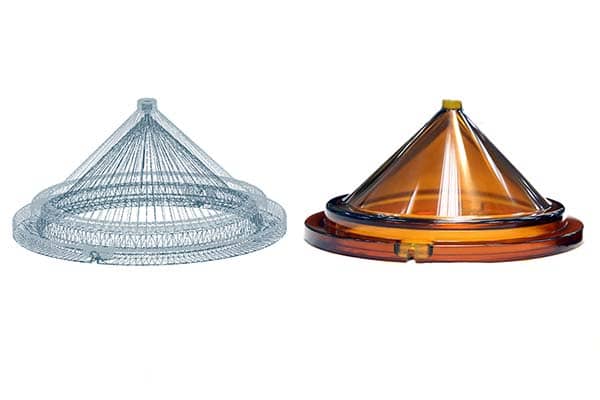
Material Verification
As with all of our projects, we used our advanced metrology equipment to verify that we had the right material. This is especially important for medical devices that must pass rigid FDA guidelines.
Our PolyMax gun employs a laser to compare the molecular signature of the sample with a database of known resin types.
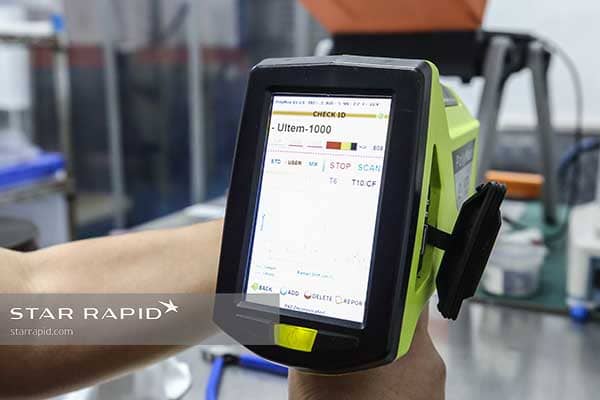
CNC Milling
First the parts were roughed out using a combination of CNC milling and turning.
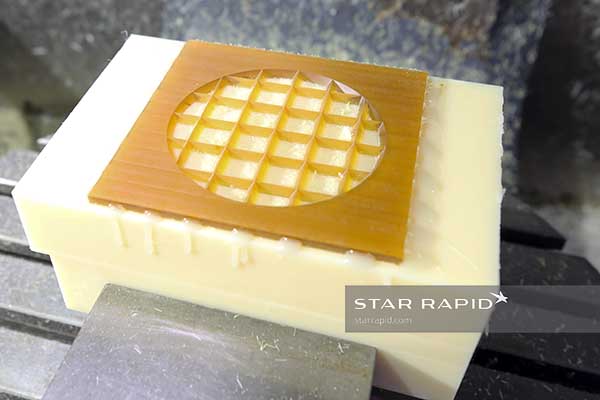
The separator screen was rough milled on our 5-axis CNC milling center, which allowed us to machine all of the beveled faces on the grid very quickly.
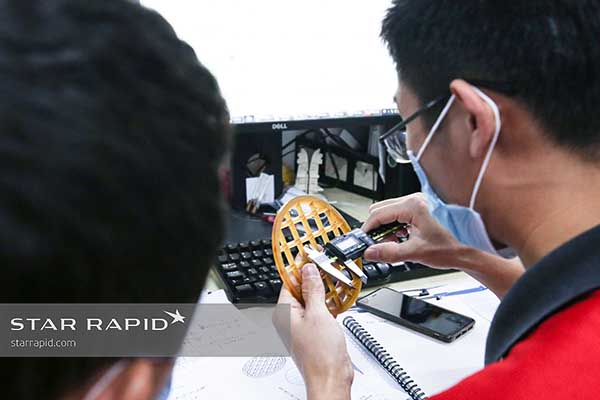
CNC Turning
For the main reservoir, we turned the large plastic blank down on the lathe, while also boring out the central hole.
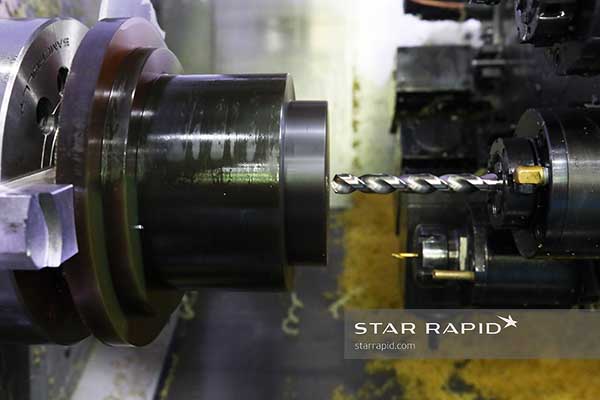
CNC turning centers have moveable turrets that can also machine inside diameters with undercuts, using “live” tools that rotate independently of the main spindle.
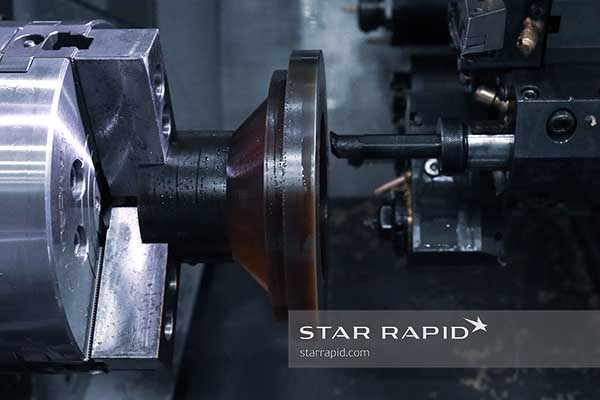
Annealing
The first pass on the machine established the major dimensions of the part, but it also left behind a rough surface finish with clearly visible tooling marks.
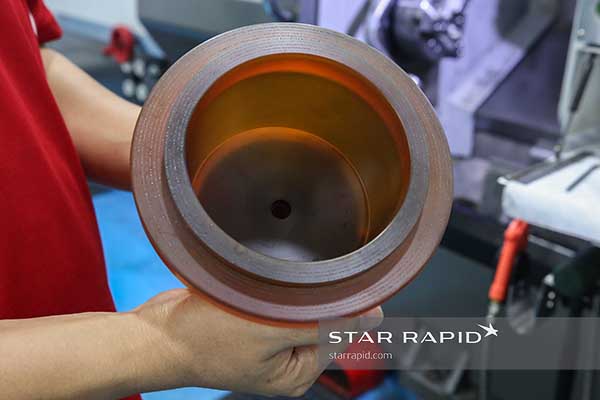
This is actually what we want, because our purpose was to first remove as much mass as possible. The displacement of this material creates stress in the walls of the container that must be relieved.
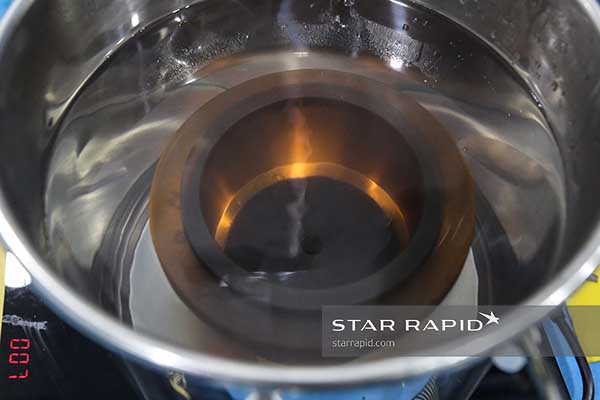
Therefore after rough machining the parts were annealed, or heated and cooled in a controlled manner. Here the water was brought to boiling and then allowed to cool back to ambient room temperature. This relieves the stress so the part won’t crack after repeated heating cycles while in use.
After annealing, the parts were then re-mounted onto the lathe for final turning.

Notice that the part was glued to a temporary base for mounting on the chuck. This prevents damage to the relatively soft plastic.
Finishing
Once the final dimensions were verified, the surface finish was given a high gloss in our model shop.
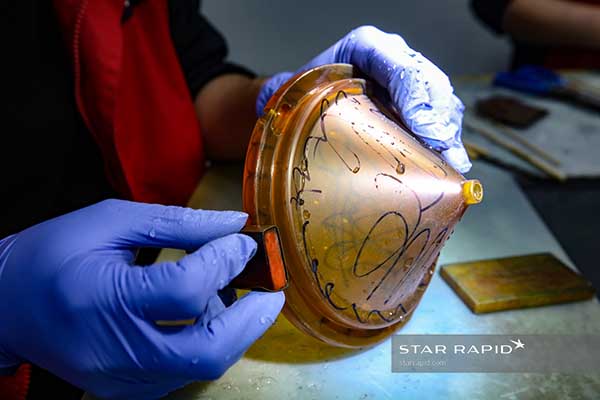
We used a black marker to indicate areas that still hadn’t been touched up yet.
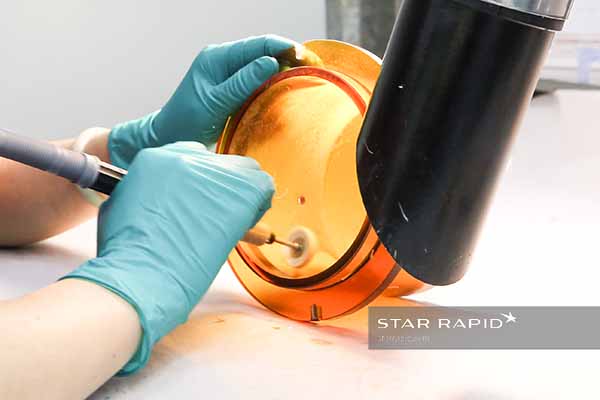
After fine sanding, we further improved the surface with polishing and buffing to achieve optical clarity.
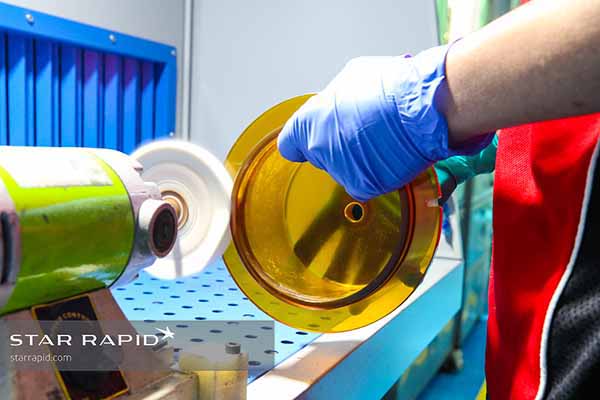
A gloss finish is good not just for cosmetic reasons. Smooth, glass-like surfaces are easier to clean and will not trap biological material used in this medical application.
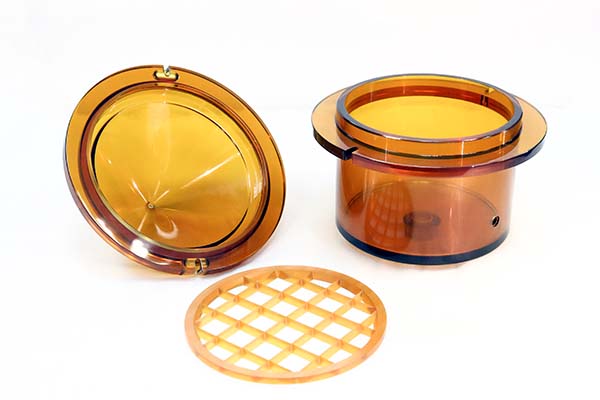
From receiving the order to shipping the parts took us less than one week, and these units are now in the field being tested.
We were able to do this because of our lean manufacturing system and a robust supply chain that was able to provide the right raw materials without delay. Check out more product development case studies below. You can be assured that you will receive the same manufacturing excellence applied to your next project when you upload your CAD files for a free quotation and project review.